Capacité de production
L'entreprise est profondément impliquée dans l'industrie du moulage depuis 20 ans. Le centre de recherche et développement est un centre technologique de deux étages avec une superficie de construction de plus de 1 200 mètres carrés. Il s'agit d'un centre provincial de technologie d'entreprise et de design industriel. Le centre technologique est équipé d'un spectromètre à lecture directe ARL2460 importé, d'un instrument de mesure du système de magnétisation de saturation, d'une machine d'essai de matériaux universelle WFW-600, d'une machine d'essai d'impact JB30B, d'un testeur de caractéristiques de refroidissement, d'un microscope métallographique optique, d'un détecteur de sable et d'autres instruments et équipements de test avancés à la maison. et à l'étranger, avec des capacités de conception innovantes. Ligne de production verticale, ligne de production de mousse perdue, moulage de coques à noyau froid, ligne de production d'impression 3D. La recherche et le développement de produits couvrent de 0,5 kg à 8 000 kg, correspondant à la ligne de moulage pour les produits en lots et à la ligne manuelle pour les produits lourds monoblocs. Il existe des machines à graver capables de graver des moules en bois et des équipements d'impression 3D capables d'imprimer des noyaux de sable à couler, réduisant ainsi le temps d'ouverture du moule. La société a passé la certification du système qualité 1SO9001 et le processus de production est équipé d'un personnel d'inspection professionnel, d'inspection finale et d'inspection des expéditions. Le taux de couverture de l'inspection finale des produits atteint 100 %, ce qui garantit efficacement la qualité et la stabilité des produits de l'entreprise.
-
20
20 ans d'expérience dans le secteur de la fonderie
-
1200M.2
Superficie du bâtiment de plus de 1 200 mètres carrés
-
100%
Le taux de couverture de l'inspection finale du produit atteint 100 %
-
Ligne de moulage verticale DISA
Capacité de production : généralement de l’ordre de 100 à 150 pièces moulées par heure, en fonction de la taille et de la complexité de la pièce moulée.
Taille du moule : moules adaptés aux pièces moulées de petite à moyenne taille, avec une taille maximale de moule d'environ 335 x 335 mm.
Méthode de moulage : moulage vertical, utilisant la technologie de moulage haute pression de DISA. -
Ligne de moulage de mousse perdue
Capacité de production : généralement de l’ordre de 50 à 100 pièces moulées par heure, en fonction de la taille et de la complexité de la pièce moulée.
Taille du moule : convient aux mousses perdues plus grandes, généralement la taille maximale du moule peut atteindre 500 x 500 mm ou plus.
Méthode de moulage : moulage de mousse perdue, utilisant de la mousse perdue fondant au gaz à haute température, capable de produire des formes complexes et des moulages de haute précision. -
Ligne de production de méthode V
Capacité de production : Le poids des pièces moulées produites par heure est d'environ 10 à 20 tonnes (en fonction de la taille de la pièce moulée et des paramètres du processus).
Taille de coulée : La taille maximale peut atteindre 3000 mm x 2000 mm x 1500 mm (peut être personnalisée selon les besoins)
Nombre de moules : La conception de plusieurs moules peut être configurée en fonction des besoins de production. -
Ligne de production de grenaillage à chaîne d'accumulation
Capacité de grenaillage : chaque grenailleuse a une capacité de grenaillage de 180 à 200 kg par minute
Puissance de la grenailleuse : chaque grenailleuse a une puissance de 11 à 15 kW et la puissance totale est de 88 à 120 kW.
Vitesse de grenaillage : 70-80 m/s. -
Ligne de production de moulage de coques à noyau froid
Capacité de production : La capacité de production se situe généralement entre 30 et 60 pièces moulées par heure, en fonction de la taille et de la complexité de la pièce moulée.
Taille du moule : convient aux moules de taille moyenne à grande, généralement la taille maximale du moule peut atteindre 400 x 400 mm ou plus.
Méthode de coulée : Coulée à noyau froid, utilisant le procédé de coque à noyau froid, capable de produire des pièces moulées complexes et de haute précision.
Niveau d'automatisation : Il dispose d'un haut niveau d'automatisation, y compris des fonctions automatiques de chargement, de formage, de coulée, de refroidissement et de démoulage des moules. -
Ligne de production de traitement thermique de four tunnel à gaz
Structure du four : briques réfractaires à haute résistance, coque en tôle d'acier à haute résistance
Taille du four : personnalisée en fonction des besoins spécifiques, généralement de 1,5 mètre à 3 mètres de haut, de 1 mètre à 2,5 mètres de large
Volume du four : environ 3 mètres cubes. -
Système de stockage stéréoscopique de contrôle intelligent d'entrepôt sans pilote
WMS (Warehouse Management System) : Fournit des fonctions telles que la gestion des stocks, le traitement des commandes, les instructions de préparation, l'entreposage et les opérations sortantes.
WCS (Warehouse Control System) : Suivi en temps réel de l'état de fonctionnement des équipements automatisés et optimisation de la planification des équipements
Interface de fonctionnement : écran tactile ou interface de contrôle par ordinateur, prend en charge la surveillance et la gestion à distance. -
La ligne de production verticale sera-t-elle
Capacité de production : 90 à 120 ensembles par heure (selon les conditions de production spécifiques)
Taille du moulage : la taille standard est de 450 mm x 600 mm x 150-350 mm (largeur x longueur x hauteur), peut être personnalisée selon les besoins.
Vitesse de moulage : 20-25 secondes/moule -
Four moyenne fréquence
Capacité de fusion : Selon la taille du four, généralement entre 5 tonnes et 15 tonnes
Temps de fusion : environ 1 à 2 heures (selon le matériau et la capacité)
Température de fusion maximale : 1600°C à 1800°C (selon le matériau spécifique) -
Poste de travail de polissage robotisé
Type d'outil de meulage : Meuleuse électrique ou pneumatique (en option)
Vitesse de meulage : réglable, allant généralement de 1 000 à 5 000 tr/min
Nombre de têtes de meulage : Unique ou multiple (selon la configuration) -
Matériel d'impression 3D
Taille principale de la machine : 9 000 × 1 900 × 1 950 mm (longueur × largeur × hauteur). Le temps d’impression de la boîte complète est d’environ 12 heures. La configuration standard est constituée de deux bacs à sable fonctionnels, qui permettent une impression ininterrompue 24 heures sur 24.
La taille intérieure du bac à sable de travail est de 1 800 × 1 000 × 730 mm (longueur × largeur × hauteur), ce qui répond aux besoins d'impression de la plupart des moules en sable de coulée.
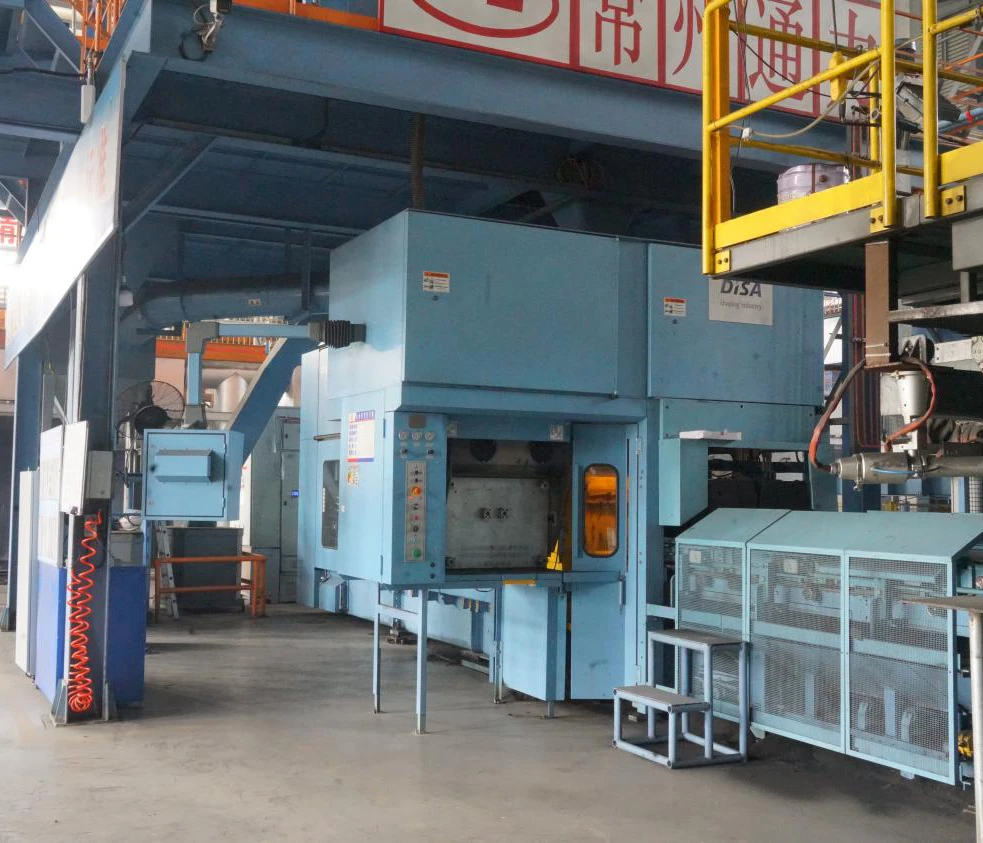
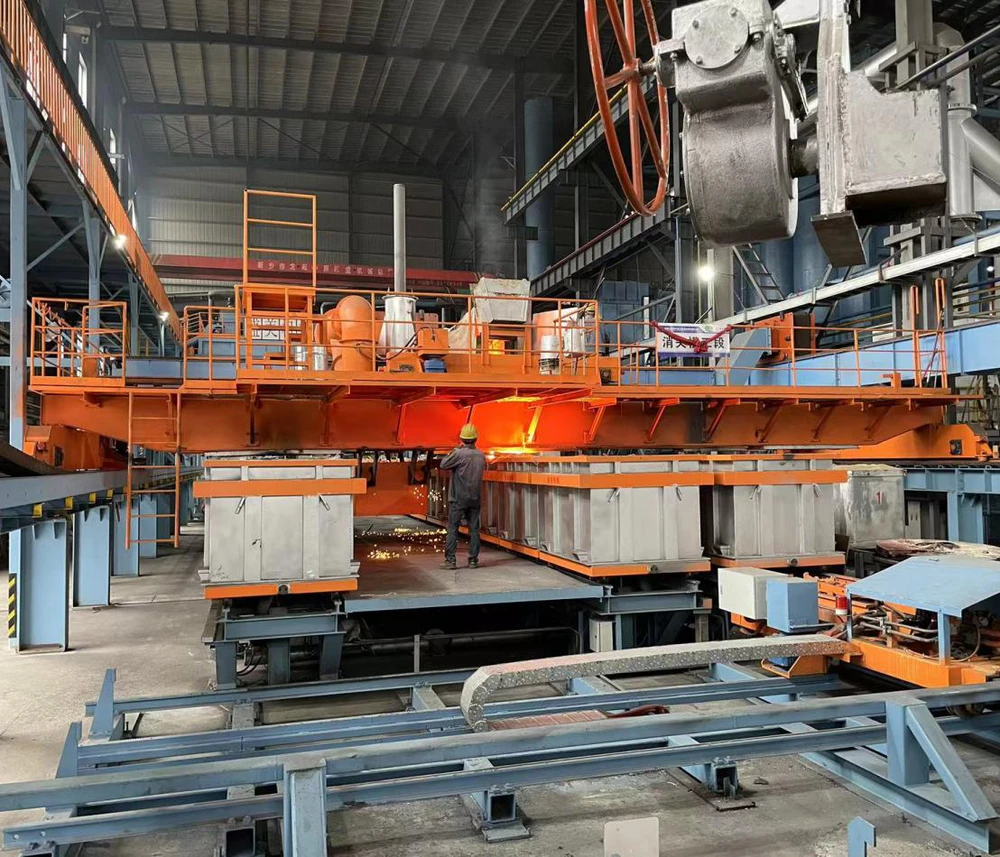
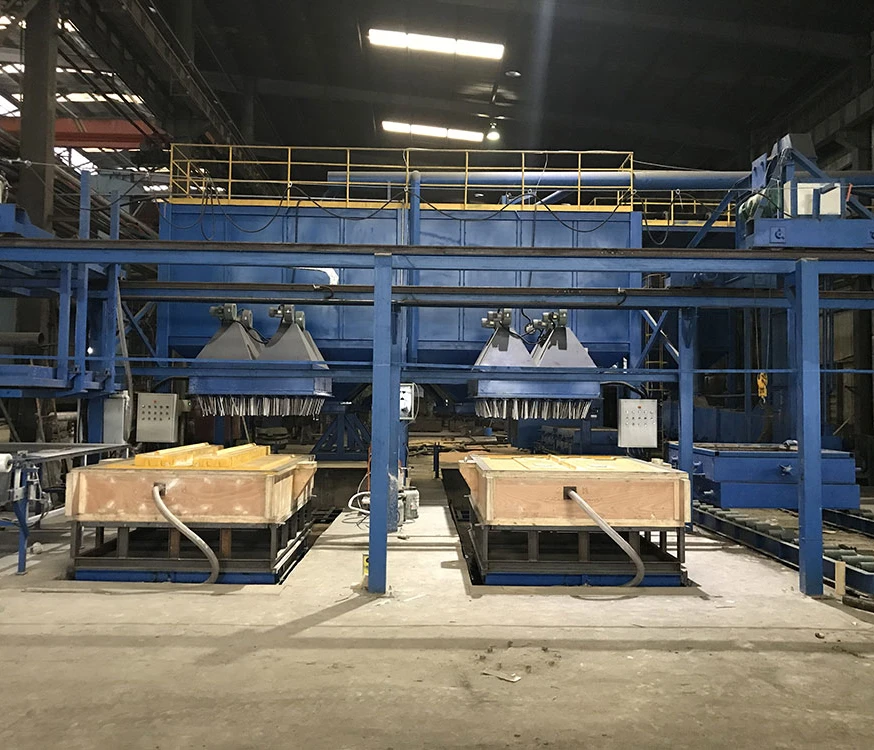
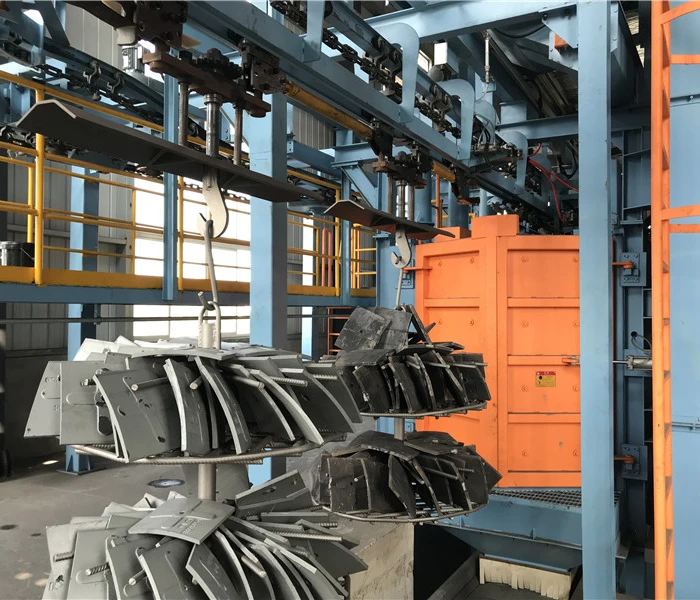
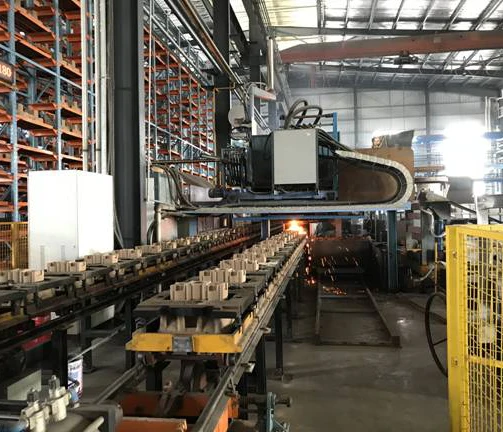
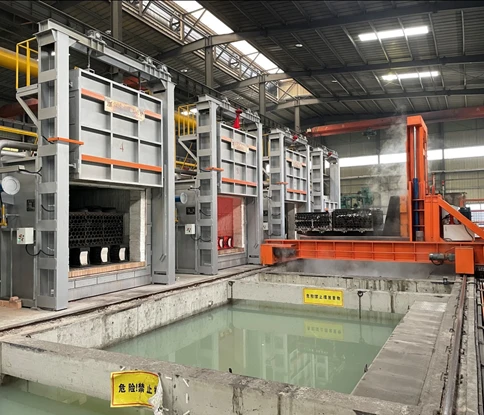
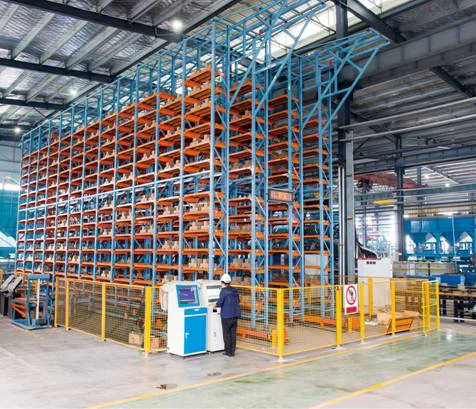
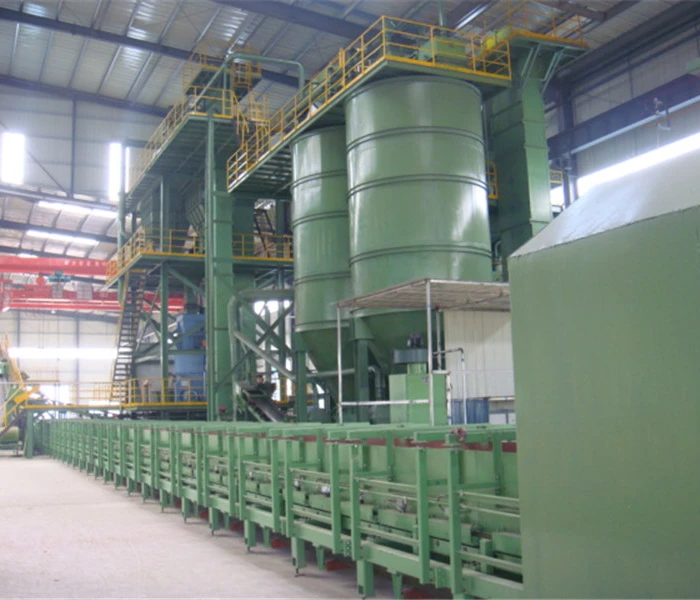
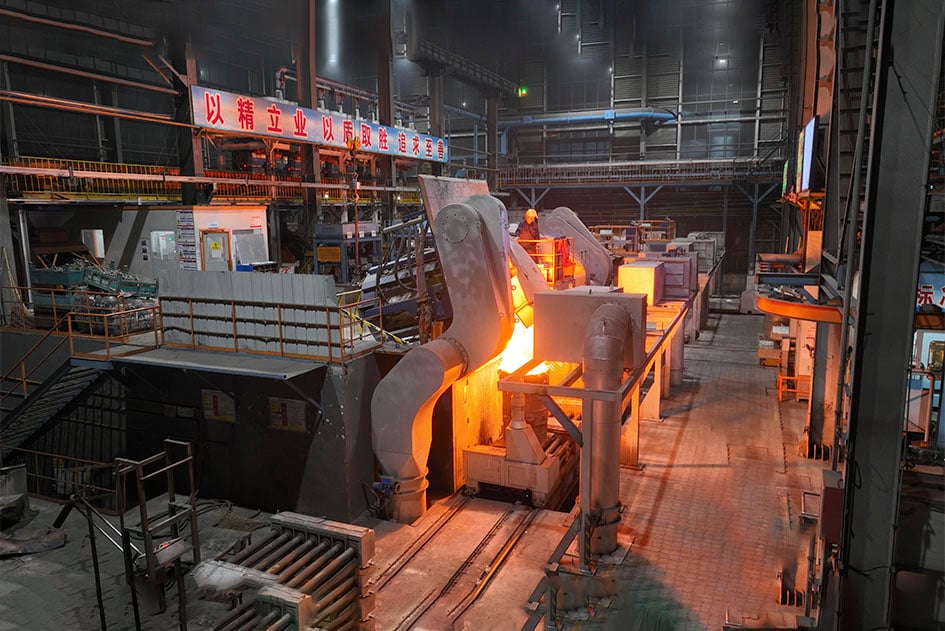
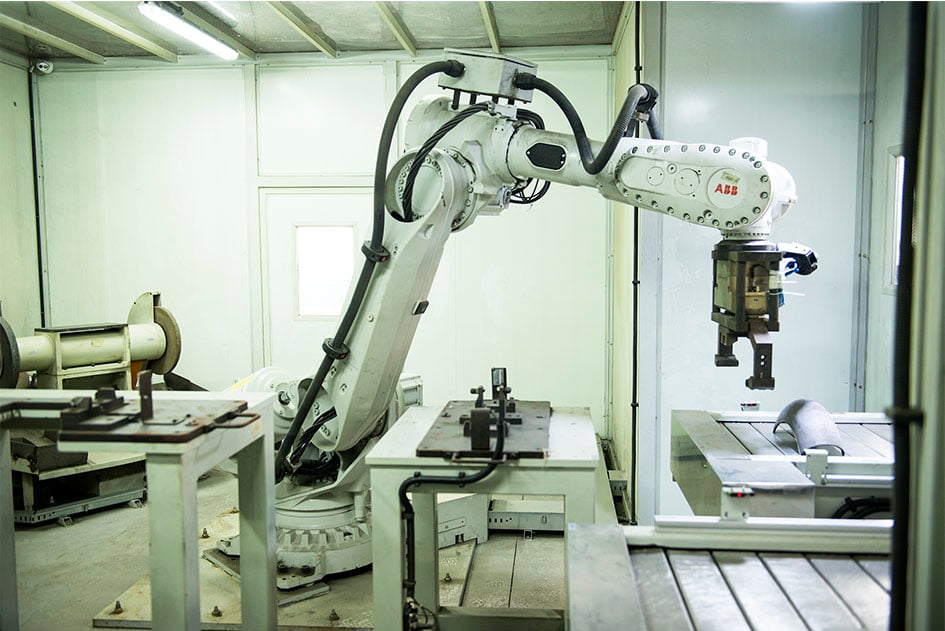
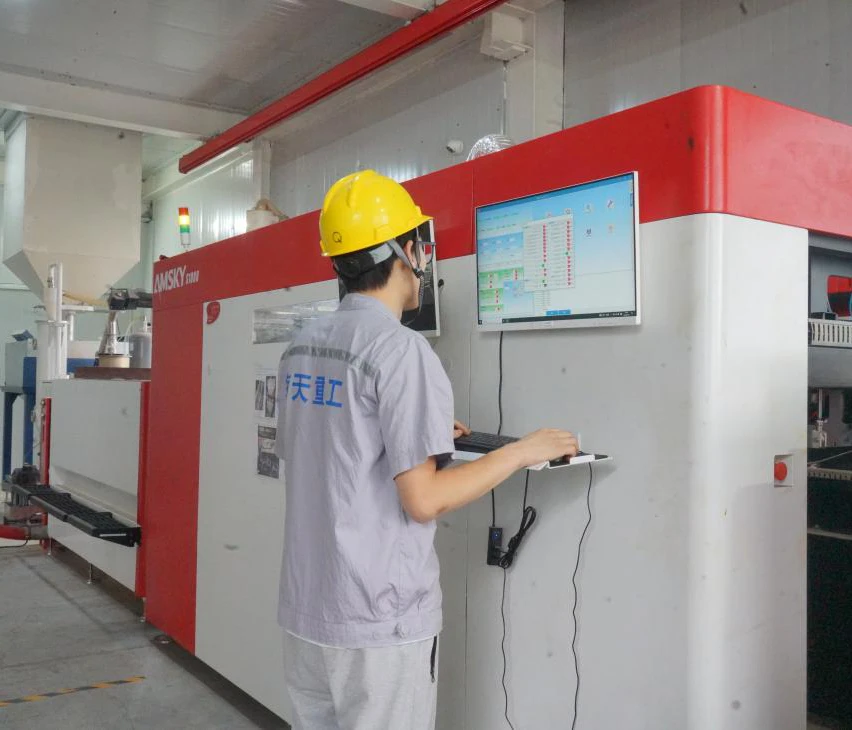
ÉQUIPEMENT D'ESSAI
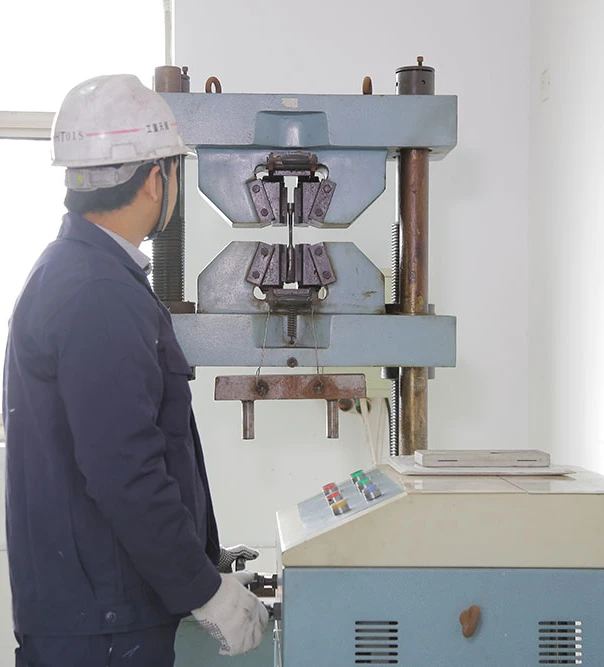
Équipement d'essai de traction

Équipement de test d'énergie d'impact
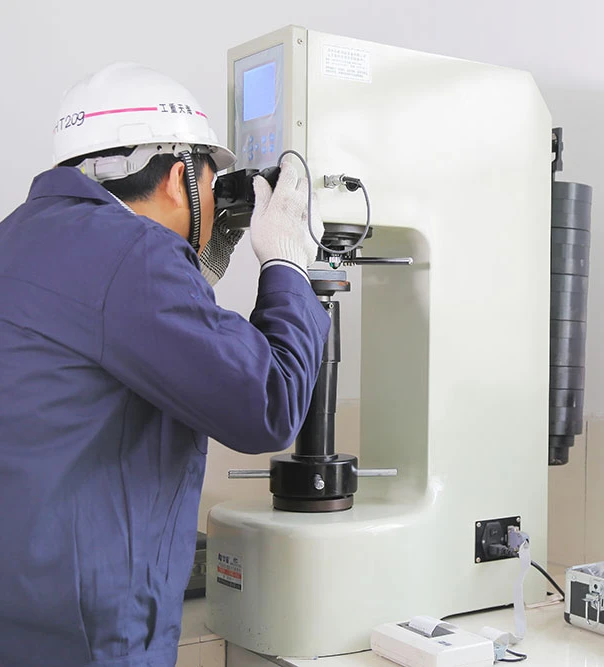
Équipement d'essai de dureté Brinell
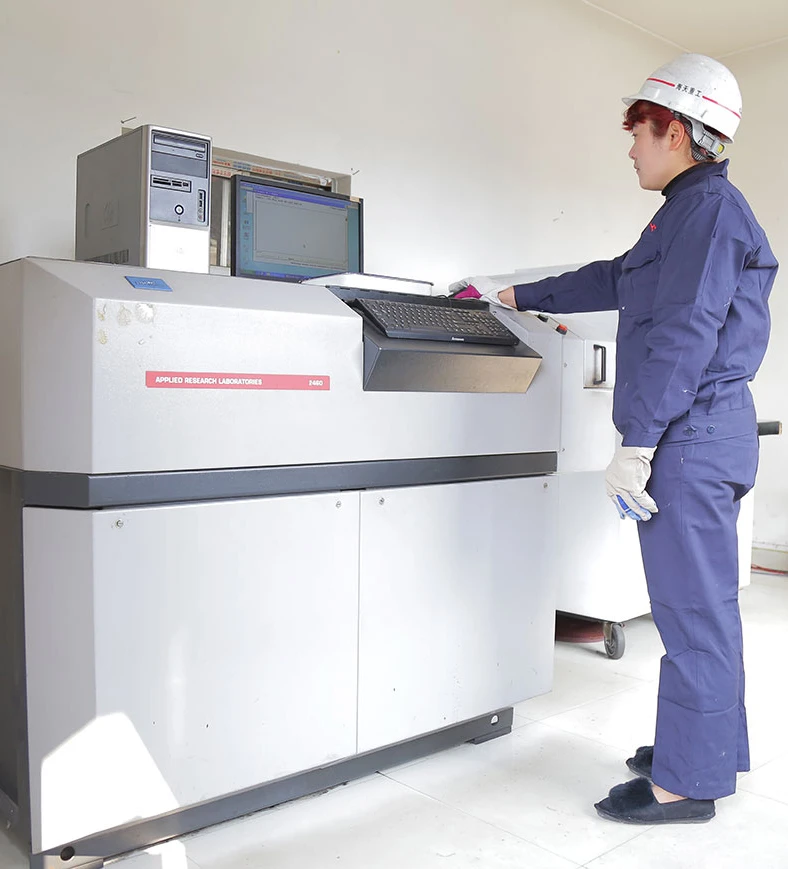
Équipement de détection de composants spectrométriques
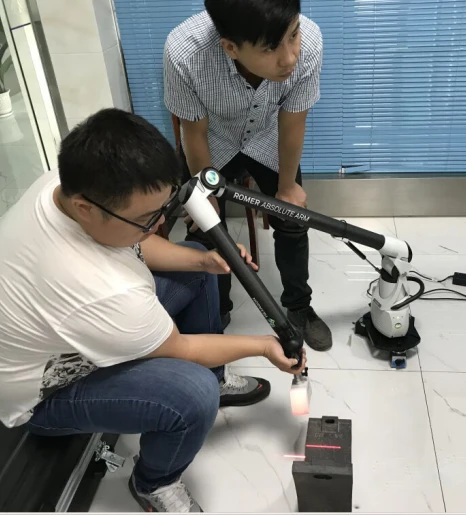
Machine de mesure de coordonnées par triangulation
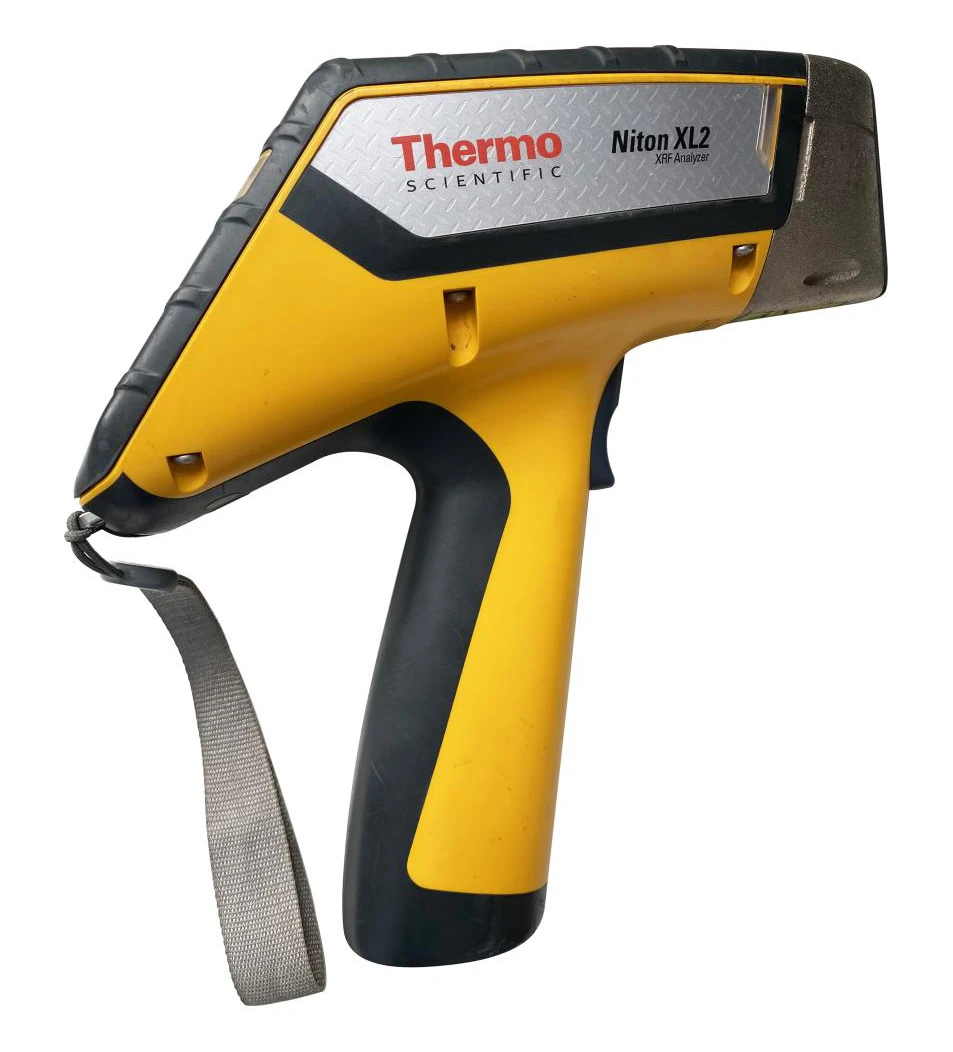
Spectromètre portatif
FILUX DE PROCESSUS
-
01
Sélection des matières premières
Dans le processus de fabrication de pièces résistantes à l’usure, le choix des matières premières est crucial. Nous sélectionnons soigneusement des matériaux en alliage de haute qualité pour garantir qu'ils présentent une excellente résistance à l'usure et une excellente résistance, établissant ainsi une base solide pour la qualité des produits.
-
02
Processus de fusion
Une fois que les matières premières strictement proportionnées entrent dans le four, nous utilisons une technologie de fusion avancée pour garantir que la composition et la température du métal en fusion atteignent l'état optimal, fournissant ainsi un flux de métal uniforme et stable pour le moulage du produit.
-
03
Coulée et moulage
Grâce au processus de coulée exquis, le métal en fusion est injecté dans le moule pour se solidifier et se mouler dans une forme et une taille spécifiques. Nos artisans ont été formés professionnellement et maîtrisent divers processus de moulage complexes pour garantir que la forme et la taille des produits sont précises et que la qualité est stable.
-
04
Grenaillage et meulage
Après démoulage, le produit subit un processus de meulage fin pour éliminer les défauts de surface et les bavures, rendant sa surface lisse et plate. Nos artisans utilisent des techniques délicates et de superbes compétences pour prendre soin de chaque produit et lui donner une apparence et une texture parfaites.
-
05
Processus de traitement thermique
Après le processus de traitement thermique, la structure et les performances du produit sont encore stabilisées et améliorées. Selon les exigences spécifiques du produit, nous utilisons différents processus de traitement thermique pour lui donner une excellente résistance à l'usure, à la résistance et à la corrosion, et nous adapter aux besoins de divers environnements de travail difficiles.
-
06
Peinture et inspection
Le produit est peint, ce qui non seulement embellit l'apparence, mais améliore également la résistance à la corrosion et à l'usure de sa surface. Après cela, il passe par un processus d'inspection strict pour garantir que tous les indicateurs du produit répondent aux exigences standard et offrent aux clients des garanties de produit fiables.
-
07
Entrée et livraison en entrepôt
Enfin, le produit est soumis à un contrôle de qualité strict et est stocké en toute sécurité dans l'entrepôt, prêt à être livré à tout moment. Une fois que nous recevons la commande du client, nous effectuerons la livraison dans les délais, en quantité et en qualité pour garantir que le produit soit livré au client en toute sécurité et à temps.
CONTRÔLE QUALITÉ PENDANT LA PRODUCTION
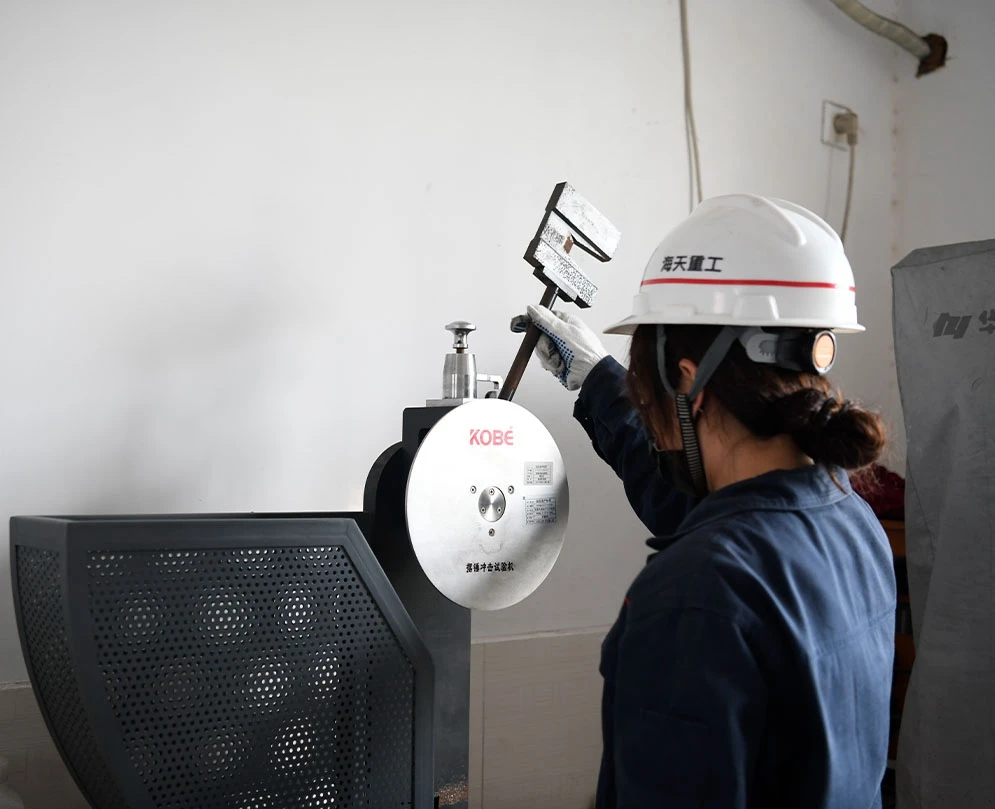
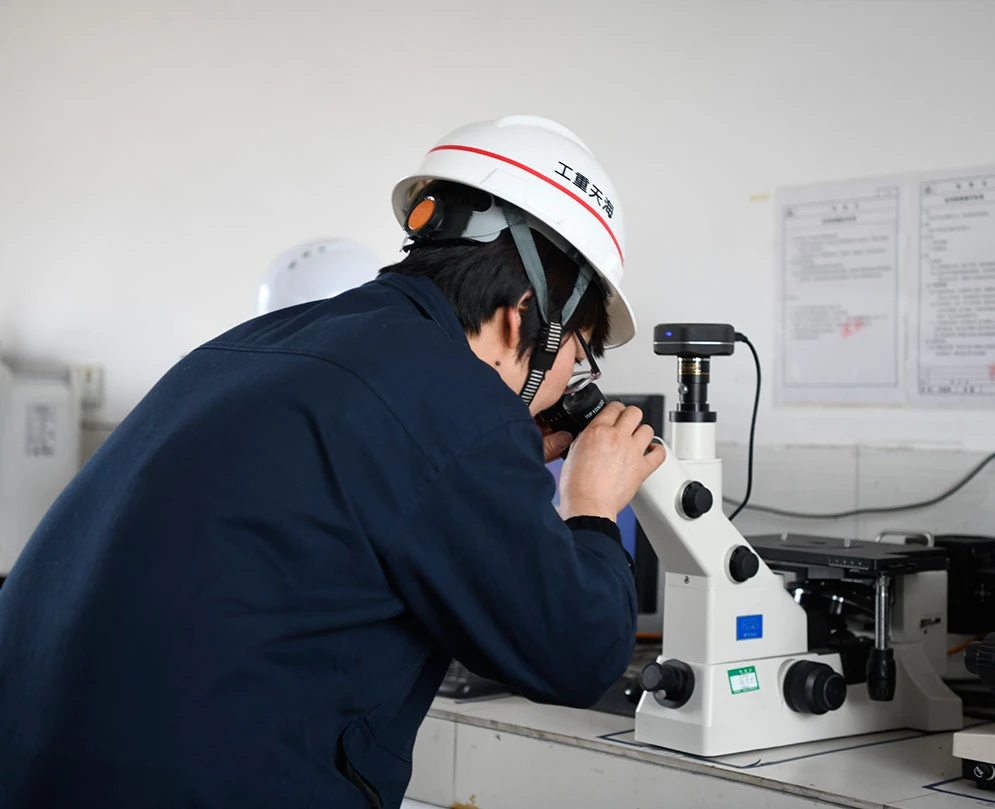
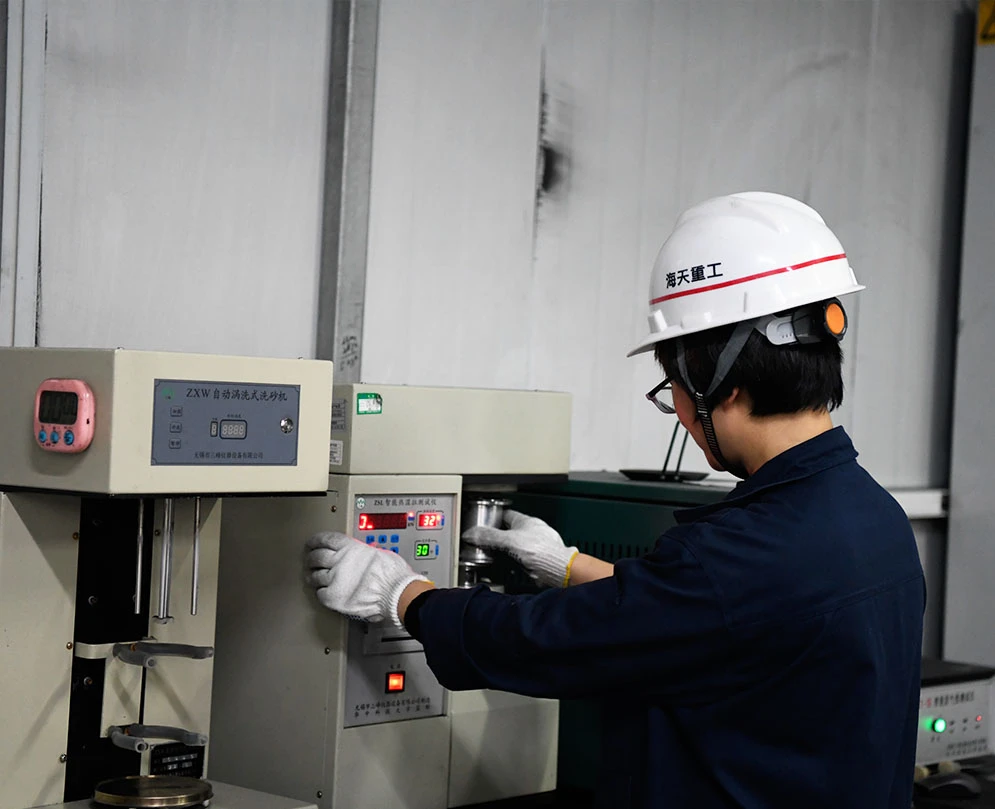
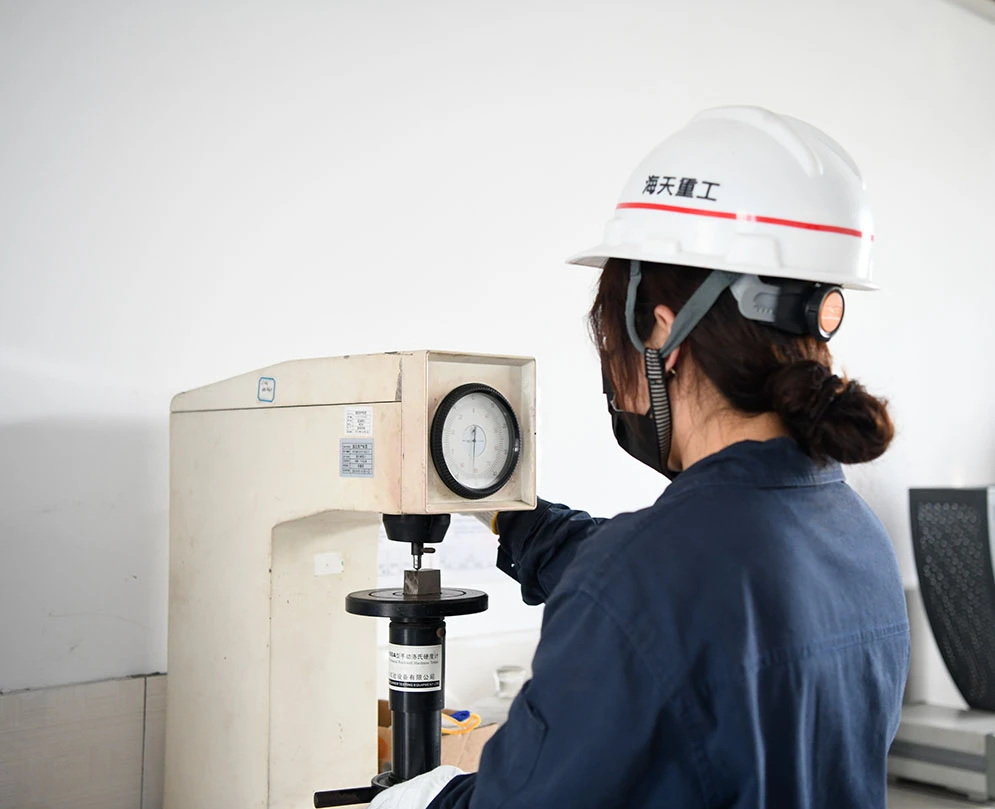
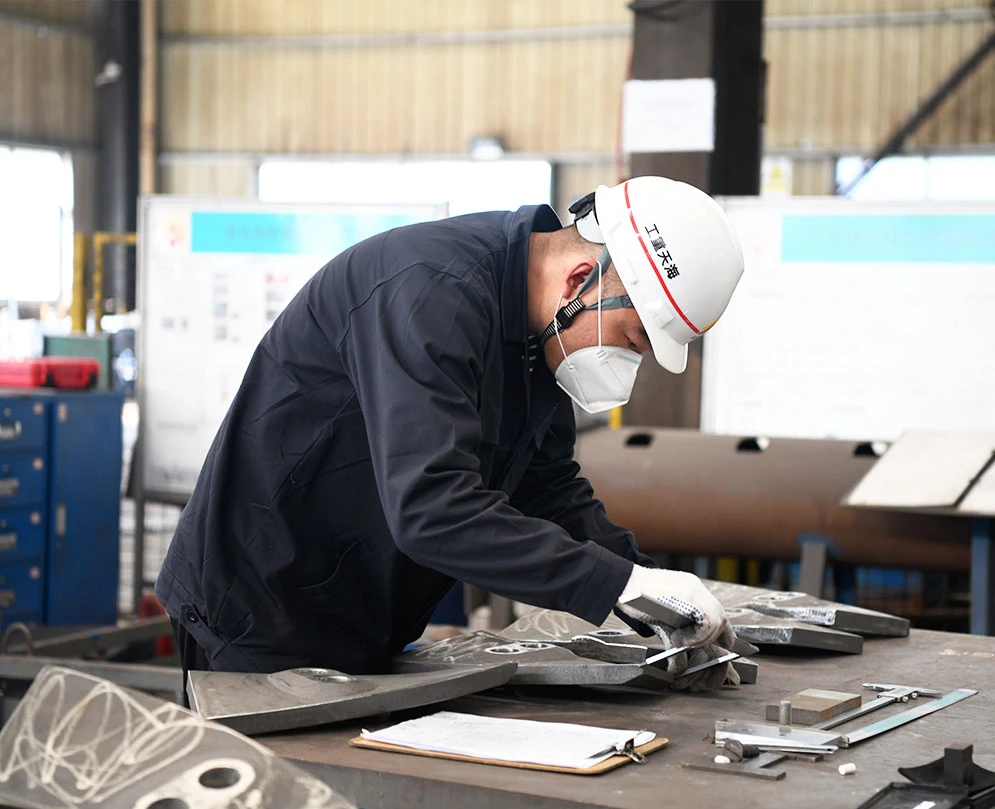
-
Contrôle des paramètres de processus
Contrôle de la température : surveillez la température pendant la fusion, le coulage et le traitement thermique pour garantir que le métal est traité dans la plage de température appropriée afin de garantir la qualité du produit.
Contrôle du temps : Contrôlez le temps de chaque processus pour garantir que chaque processus est entièrement exécuté sans excès pour éviter les défauts.
Contrôle de la pression : pendant le processus de coulée et de moulage, la taille et la répartition de la pression sont contrôlées par aspiration à travers une membrane transparente pour assurer l'uniformité et la stabilité du liquide métallique remplissant le moule.
-
Application de l'équipement de test
Détection au microscope métallurgique : Observez et analysez la structure métallique pour détecter s'il existe des défauts tels que des pores et des inclusions à l'intérieur du métal.
Détection par ultrasons : utilisez la technologie par ultrasons pour détecter les défauts à l'intérieur du produit, tels que les fissures, les inclusions, etc., afin de garantir la qualité et la fiabilité du produit.
Test de dureté : Testez la dureté du produit pour évaluer si sa résistance à l'usure et ses propriétés mécaniques répondent aux exigences.
-
Équipement de production automatisé
Système de contrôle automatisé : utilisez des systèmes de contrôle automatisés avancés pour surveiller le processus de production, obtenir un contrôle et un ajustement précis des paramètres de production et améliorer la cohérence et la stabilité du produit.
-
Contrôle qualité manuel
Inspection des techniciens de processus : les techniciens de processus inspectent régulièrement la chaîne de production pour s'assurer que l'équipement fonctionne normalement et que les paramètres de production répondent aux exigences.
Supervision des opérations de l'opérateur de processus : superviser le fonctionnement de l'opérateur de processus pour garantir que l'opération est standardisée et précise, et réduire l'impact des erreurs opérationnelles sur la qualité du produit.
-
Analyse et amélioration des données
Collecte et analyse de données de qualité : collectez diverses données de qualité dans le processus de production, effectuez des analyses statistiques, trouvez les problèmes à temps et prenez des mesures d'amélioration.
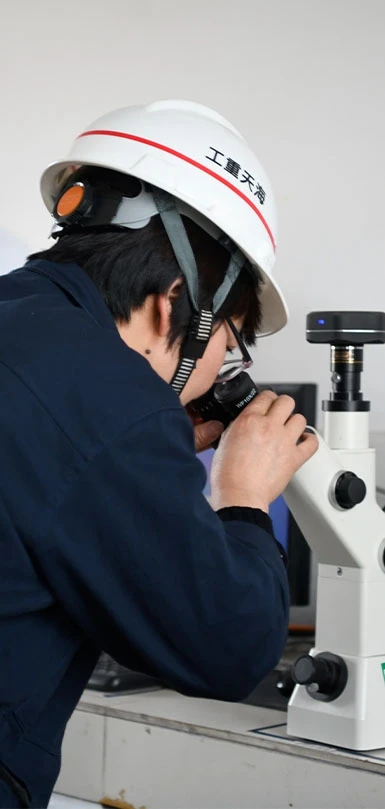
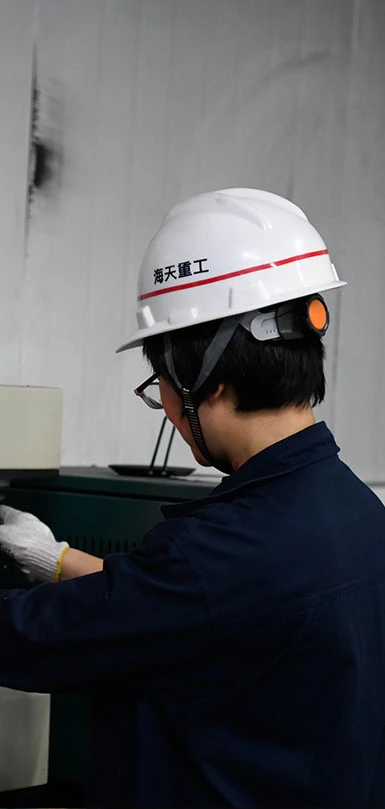
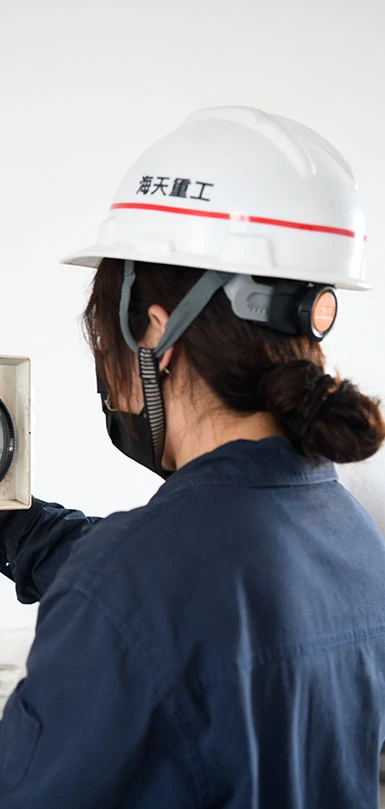
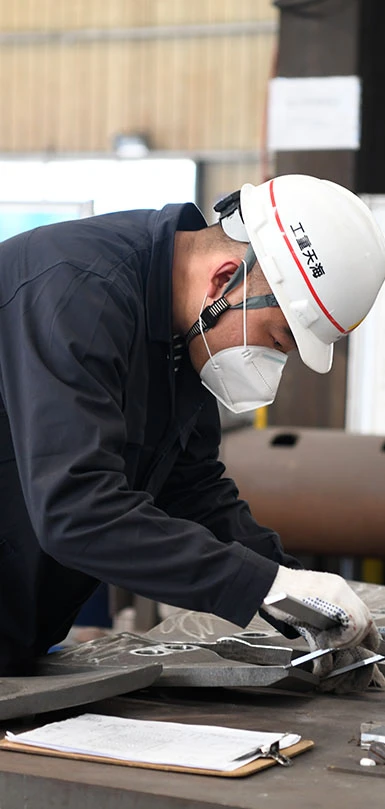
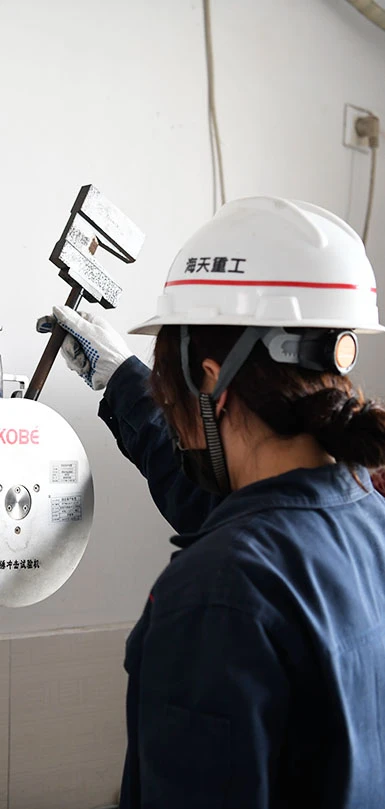
Si vous êtes intéressé par nos produits ou si vous avez des questions, n'hésitez pas à nous contacter.
Nous fournirons des services de conseil professionnels et des solutions personnalisées en fonction de vos besoins.
ENVOYER UNE DEMANDE MAINTENANTCoordonnées
Tél : 0555-71661667166199
Télécopie : 0555-6971198
Site web: https://www.htwearparts.com
E-mail: info@mashthi.com
Code postal : 243141
Adresse : parc industriel de Xinshi, district de Bowang, ville de Ma'anshan, province d'Anhui, Chine