Productiecapaciteit
Het bedrijf is al 20 jaar nauw betrokken bij de gietindustrie. Het onderzoeks- en ontwikkelingscentrum is een technologiecentrum van twee verdiepingen met een bouwoppervlakte van meer dan 1.200 vierkante meter. Het is een provinciaal centrum voor bedrijfstechnologie en industrieel ontwerp. Het technologiecentrum is uitgerust met een geïmporteerde ARL2460-spectrometer voor directe aflezing, een meetinstrument voor het verzadigingsmagnetisatiesysteem, een WFW-600 universele materiaaltestmachine, een JB30B-impacttestmachine, een tester voor koelkarakteristieken, een optische metallografische microscoop, een zanddetector en andere geavanceerde testinstrumenten en apparatuur thuis. en in het buitenland, met innovatieve ontwerpmogelijkheden. Verticale productielijn, productielijn voor verloren schuim, gieten van koude kernschalen, productielijn voor 3D-printen. Productonderzoek en -ontwikkeling strekt zich uit van 0,5 kg tot 8000 kg, wat overeenkomt met de vormlijn voor batchproducten en de handmatige lijn voor zware producten uit één stuk. Er zijn graveermachines die houten mallen kunnen graveren, en 3D-printapparatuur die zandkernen kan printen om te gieten, waardoor de openingstijd van de mal wordt verkort. Het bedrijf is geslaagd voor de 1SO9001-certificering van het kwaliteitssysteem en het productieproces is uitgerust met professioneel inspectie-, eindinspectie- en verzendingsinspectiepersoneel. Het dekkingspercentage van de eindinspectie van het product bereikt 100%, wat effectief de kwaliteit en stabiliteit van de producten van het bedrijf garandeert.
-
20
20 jaar ervaring in de gieterijbranche
-
1200M2
Bouwoppervlakte van meer dan 1.200 vierkante meter
-
100%
De dekkingsgraad van de producteindinspectie bereikt 100%
-
DISA verticale vormlijn
Productiecapaciteit: doorgaans tussen de 100 en 150 gietstukken per uur, afhankelijk van de gietgrootte en complexiteit.
Matrijsgrootte: Matrijzen geschikt voor kleine tot middelgrote gietstukken, met een maximale matrijsgrootte van circa 335 x 335 mm.
Vormmethode: Verticaal gieten, met behulp van DISA's hogedrukgiettechnologie. -
Verloren schuimvormlijn
Productiecapaciteit: Meestal tussen de 50 en 100 gietstukken per uur, afhankelijk van de grootte en complexiteit van het gietstuk.
Vormgrootte: Geschikt voor groter verloren schuim, meestal kan de maximale vormgrootte 500 x 500 mm of groter bedragen.
Gietmethode: verloren schuimgieten, waarbij gebruik wordt gemaakt van gassmeltend verloren schuim bij hoge temperatuur, geschikt voor het produceren van complexe vormen en gietstukken met hoge precisie. -
V-methode productielijn
Productiecapaciteit: Het gewicht van de geproduceerde gietstukken per uur bedraagt ongeveer 10-20 ton (afhankelijk van de gietgrootte en procesparameters)
Gietgrootte: de maximale grootte kan 3000 mm x 2000 mm x 1500 mm bereiken (kan worden aangepast aan de behoeften)
Aantal mallen: ontwerp met meerdere mallen, kan worden geconfigureerd volgens productiebehoeften. -
Accumulatiekettingstraalproductielijn
Straalcapaciteit: Elke straalmachine heeft een straalcapaciteit van 180-200 kg per minuut
Vermogen straalmachine: Elke straalmachine heeft een vermogen van 11-15 kW en het totale vermogen is 88-120 kW
Straalsnelheid: 70-80 m/s. -
Productielijn voor het vormen van koude kernschalen
Productiecapaciteit: De productiecapaciteit ligt doorgaans tussen de 30-60 gietstukken per uur, afhankelijk van de grootte en complexiteit van het gietstuk.
Matrijsgrootte: Geschikt voor middelgrote tot grote matrijzen, meestal kan de maximale matrijsgrootte 400 x 400 mm of groter bedragen.
Gietmethode: Koudkerngieten, met behulp van het koude kernschaalproces, geschikt voor het produceren van zeer nauwkeurige en complexe gietstukken.
Automatiseringsniveau: Het heeft een hoog automatiseringsniveau, inclusief automatische functies voor het laden van mallen, vormen, gieten, koelen en ontvormen. -
Productielijn voor warmtebehandeling van gastunnelovens
Ovenstructuur: vuurvaste stenen met hoge sterkte, schaal is staalplaat met hoge sterkte
Ovengrootte: aangepast aan specifieke behoeften, doorgaans 1,5 meter tot 3 meter hoog, 1 meter tot 2,5 meter breed
Ovenvolume: ongeveer 3 kubieke meter. -
Onbemand magazijn intelligent controle stereoscopisch opslagsysteem
WMS (Warehouse Management System): Biedt functies zoals voorraadbeheer, orderverwerking, pickinstructies, opslag en uitgaande activiteiten
WCS (Warehouse Control System): realtime monitoring van de bedrijfsstatus van geautomatiseerde apparatuur en optimalisatie van de apparatuurplanning
Bedieningsinterface: touchscreen of computerbesturingsinterface, ondersteunt bewaking en beheer op afstand. -
Zal verticale productielijn
Productiecapaciteit: 90-120 sets per uur (afhankelijk van specifieke productieomstandigheden)
Vormgrootte: standaardformaat is 450 mm x 600 mm x 150-350 mm (breedte x lengte x hoogte), kan worden aangepast aan de behoeften
Vormsnelheid: 20-25 seconden/vorm -
Middelhoge frequentie oven
Smeltcapaciteit: Afhankelijk van de grootte van de oven, meestal tussen 5 ton en 15 ton
Smelttijd: ongeveer 1-2 uur (afhankelijk van het materiaal en de capaciteit)
Maximale smelttemperatuur: 1600°C tot 1800°C (afhankelijk van het specifieke materiaal) -
Robotpolijstwerkstation
Type slijpgereedschap: elektrische of pneumatische slijpmachine (optioneel)
Slijpsnelheid: instelbaar, doorgaans van 1000 tot 5000 tpm
Aantal schuurkoppen: Enkel of meervoudig (afhankelijk van configuratie) -
3D-printapparatuur
Grootte hoofdmachine: 9000 × 1900 × 1950 mm (lengte × breedte × hoogte). De volledige doosafdruktijd bedraagt ongeveer 12 uur. De standaardconfiguratie bestaat uit twee werkende zandbakken, waarmee 24 uur per dag ononderbroken kan worden afgedrukt.
De binnenmaat van de werkende zandbak is 1800 × 1000 × 730 mm (lengte × breedte × hoogte), wat voldoet aan de printbehoeften van de meeste gietzandvormen.
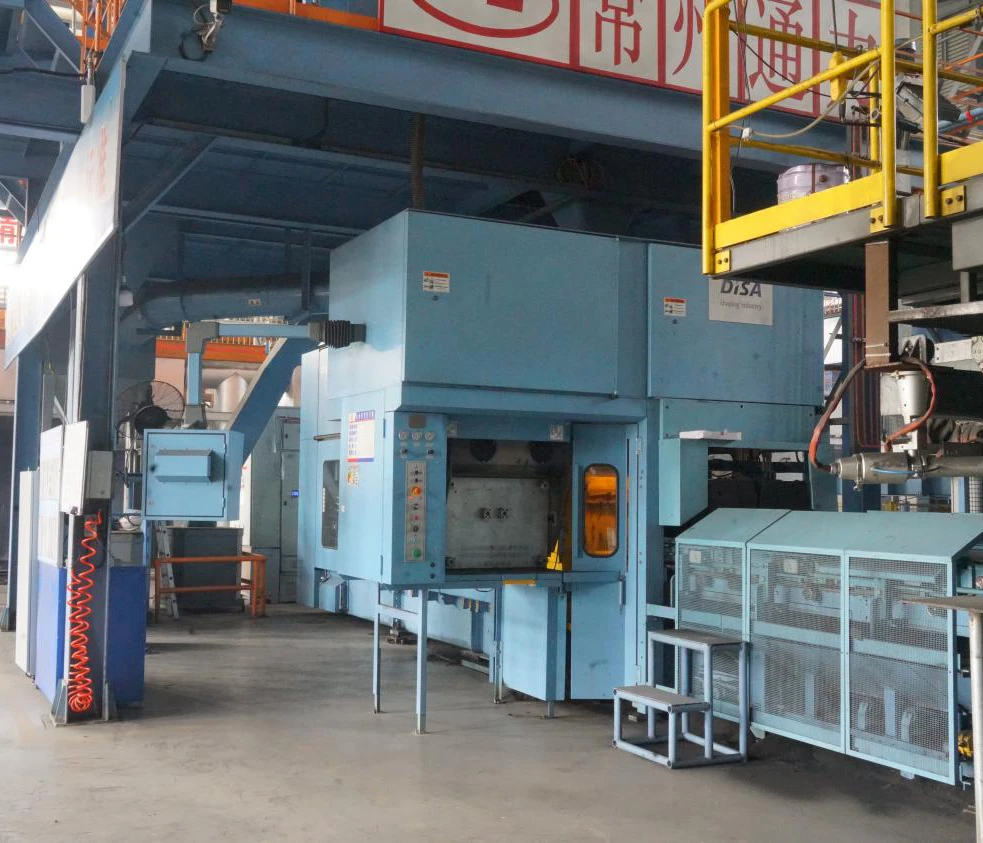
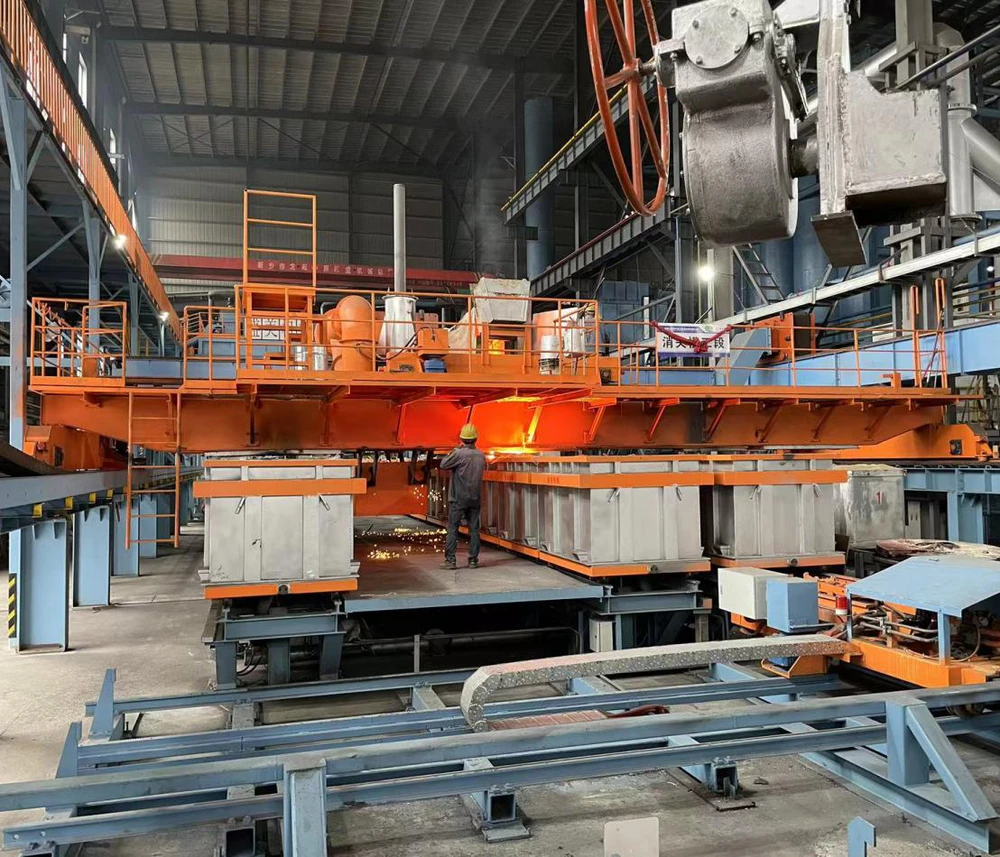
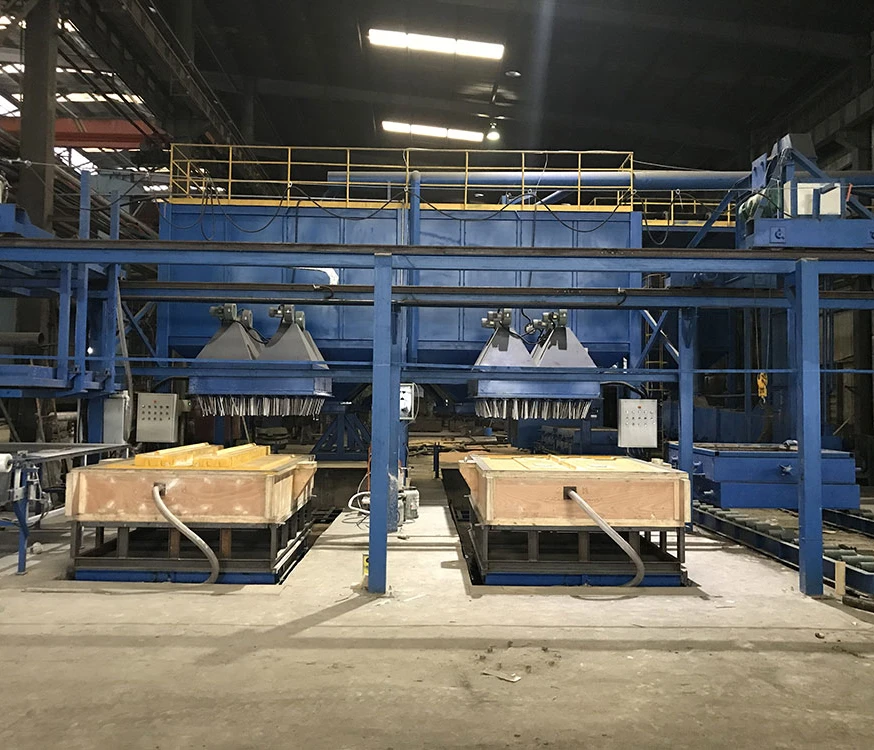
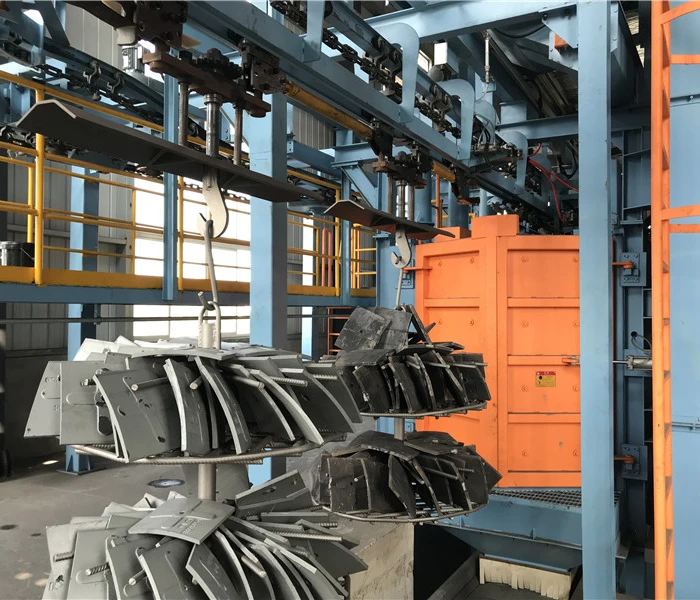
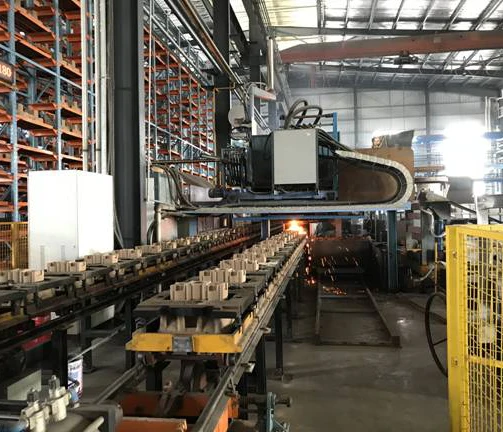
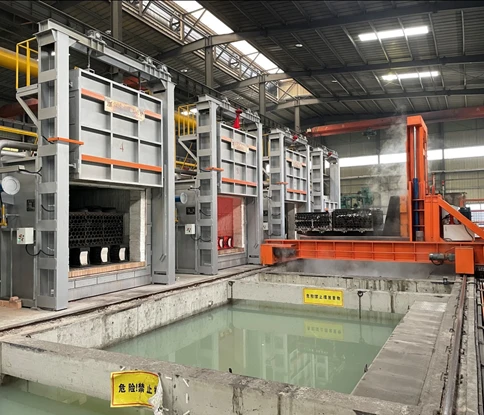
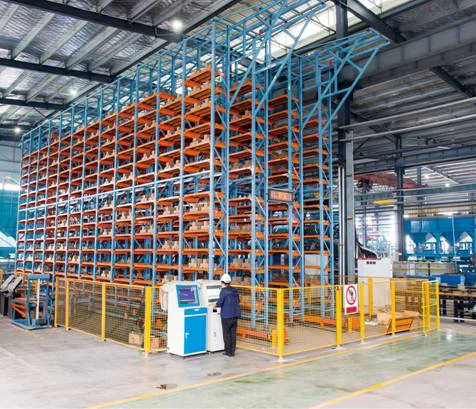
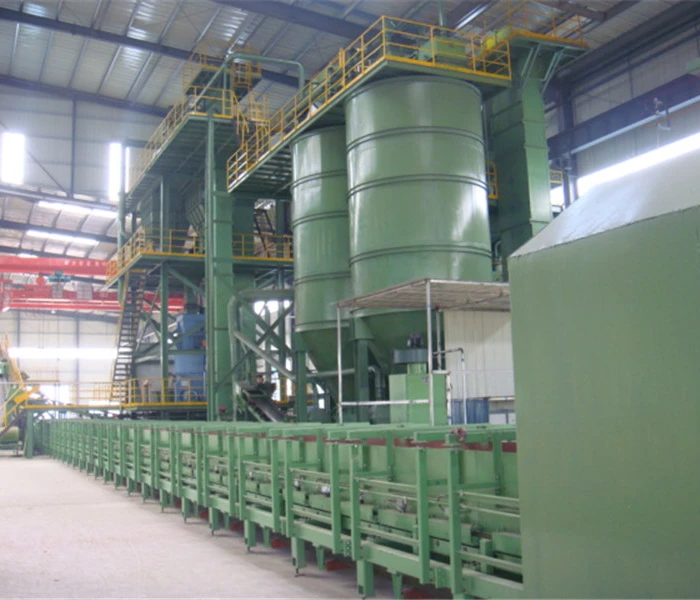
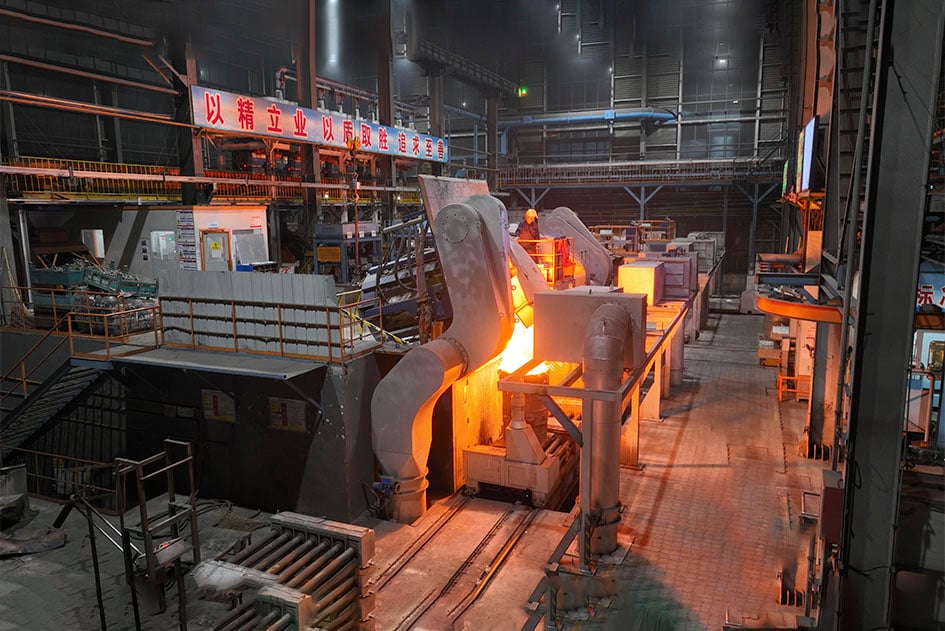
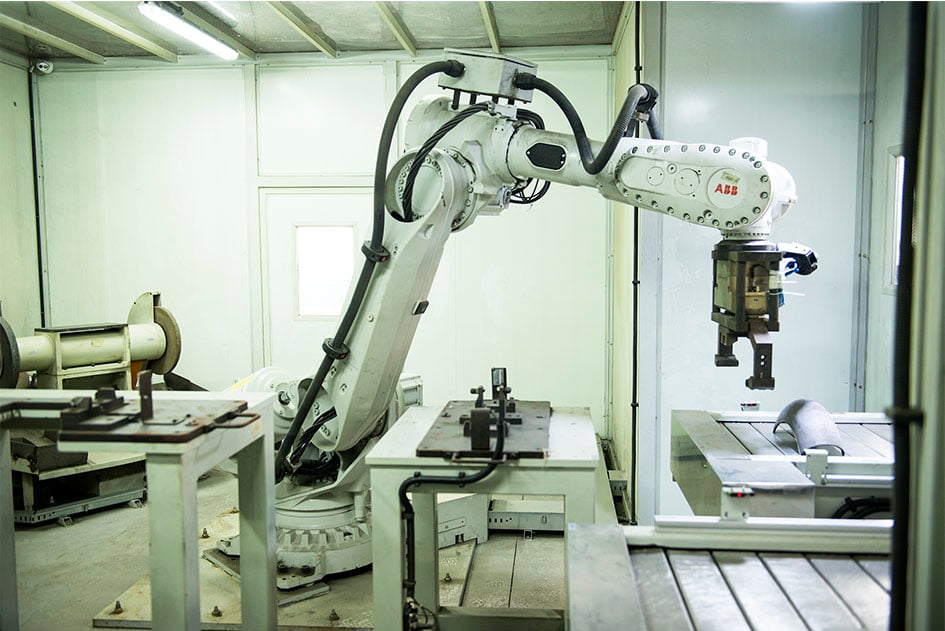
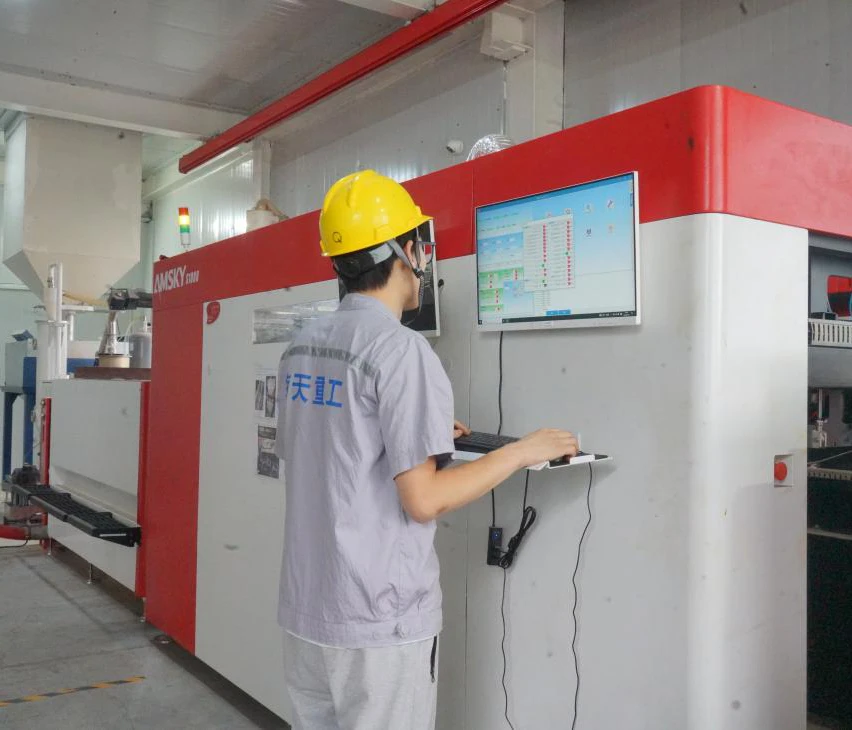
TESTAPPARATUUR
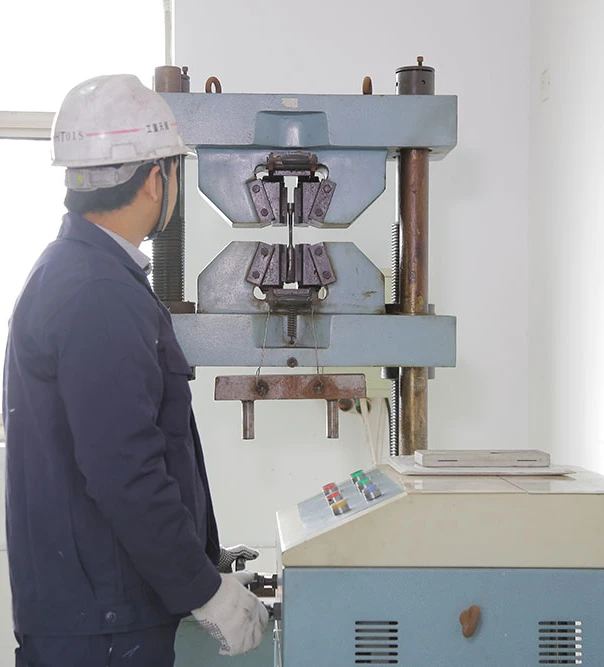
Apparatuur voor trekproeven

Apparatuur voor het testen van impactenergie
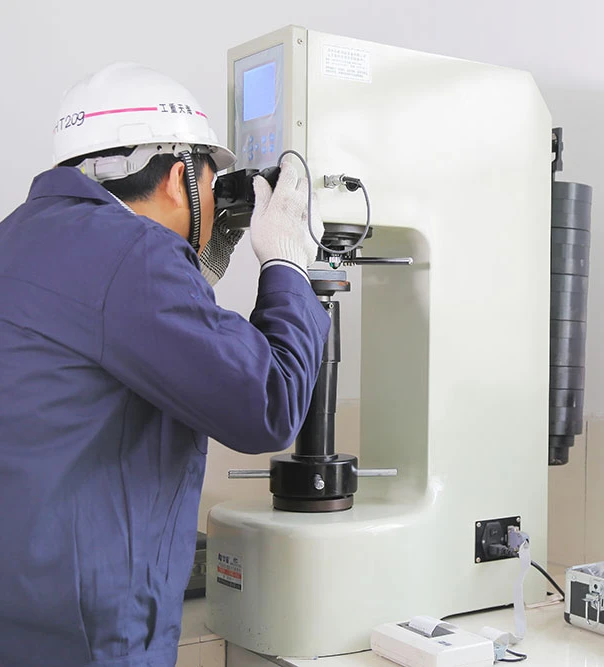
Apparatuur voor het testen van de hardheid van Brinell
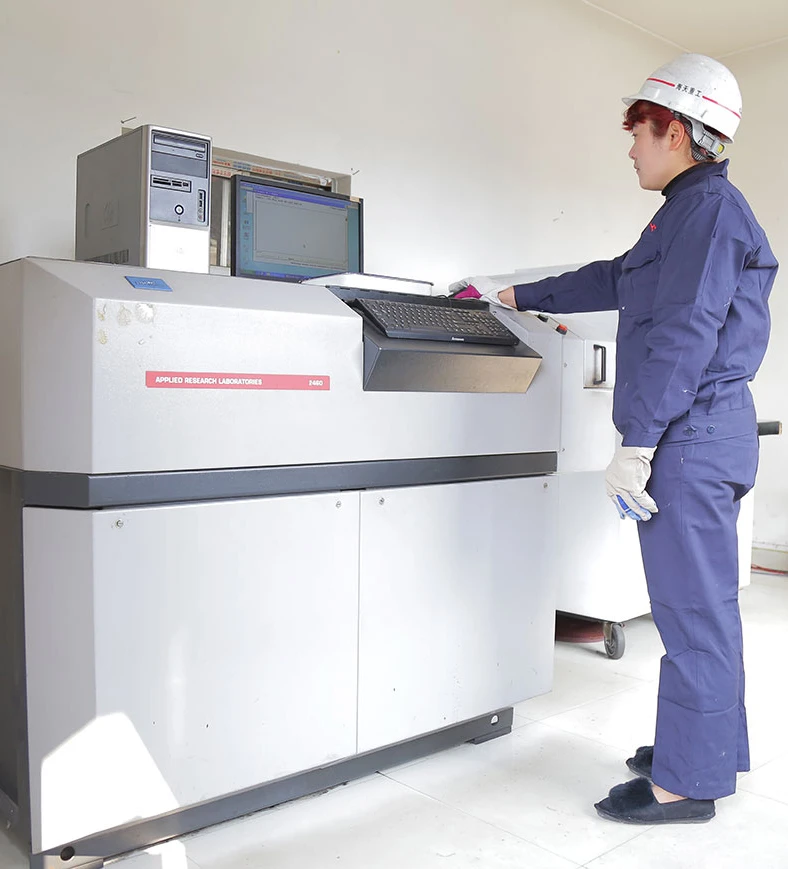
Detectieapparatuur voor spectrometercomponenten
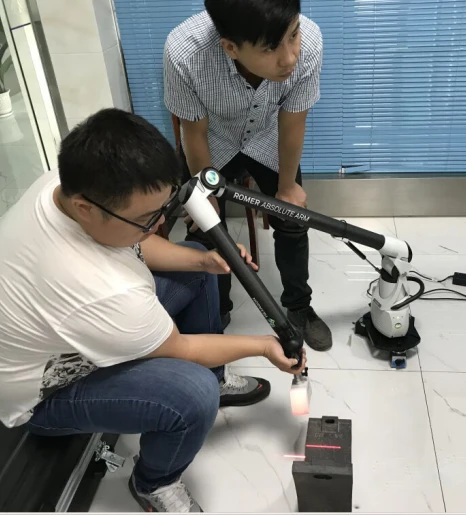
Triangulatiecoördinatenmeetmachine
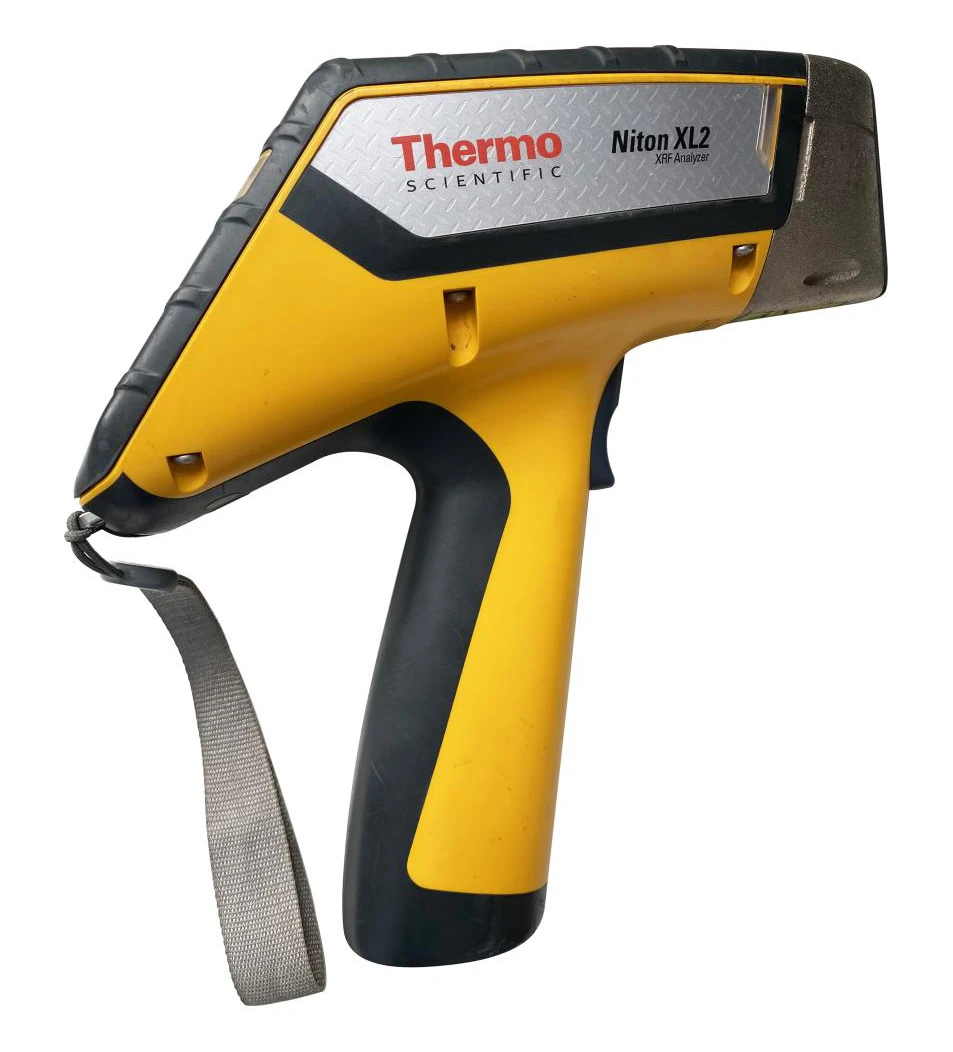
Handbediende spectrometer
PROCESVERLOOP
-
01
Selectie van grondstoffen
Bij het productieproces van slijtvaste onderdelen is de selectie van grondstoffen cruciaal. We selecteren zorgvuldig hoogwaardige legeringsmaterialen om ervoor te zorgen dat ze een uitstekende slijtvastheid en sterkte hebben, waardoor een solide basis wordt gelegd voor de kwaliteit van de producten.
-
02
Smeltproces
Nadat de strikt geproportioneerde grondstoffen de oven binnenkomen, gebruiken we geavanceerde smelttechnologie om ervoor te zorgen dat de samenstelling en temperatuur van het gesmolten metaal de optimale staat bereiken, waardoor een uniforme en stabiele metaalstroom ontstaat voor het vormen van het product.
-
03
Gieten en vormen
Door het voortreffelijke gietproces wordt het gesmolten metaal in de mal geïnjecteerd om te stollen en in een specifieke vorm en maat te vormen. Onze vakmensen zijn professioneel opgeleid en zijn bedreven in verschillende complexe vormprocessen om ervoor te zorgen dat de vorm en maat van de producten nauwkeurig zijn en de kwaliteit stabiel is.
-
04
Stralen en slijpen
Na het uit de vorm halen ondergaat het product een fijn maalproces om oppervlaktedefecten en bramen te verwijderen, waardoor het oppervlak glad en vlak wordt. Onze vakmensen gebruiken delicate technieken en uitstekende vaardigheden om elk product te verzorgen en het een perfect uiterlijk en textuur te geven.
-
05
Warmtebehandelingsproces
Na het warmtebehandelingsproces worden de structuur en prestaties van het product verder gestabiliseerd en verbeterd. Afhankelijk van de specifieke vereisten van het product gebruiken we verschillende warmtebehandelingsprocessen om het een uitstekende slijtvastheid, sterkte en corrosieweerstand te geven en zich aan te passen aan de behoeften van verschillende zware werkomgevingen.
-
06
Schilderen en inspectie
Het product is geverfd, wat niet alleen het uiterlijk verfraait, maar ook de corrosieweerstand en slijtvastheid van het oppervlak verbetert. Daarna doorloopt het een strikt inspectieproces om ervoor te zorgen dat alle indicatoren van het product aan de standaardvereisten voldoen en klanten betrouwbare productgaranties bieden.
-
07
Magazijninvoer en levering
Ten slotte ondergaat het product een strenge kwaliteitscontrole en wordt het veilig opgeslagen in het magazijn, zodat het op elk moment kan worden afgeleverd. Zodra we de bestelling van de klant hebben ontvangen, zullen we de levering op tijd, kwantiteit en kwaliteit voltooien om ervoor te zorgen dat het product veilig en op tijd bij de klant wordt afgeleverd.
KWALITEITSCONTROLE TIJDENS DE PRODUCTIE
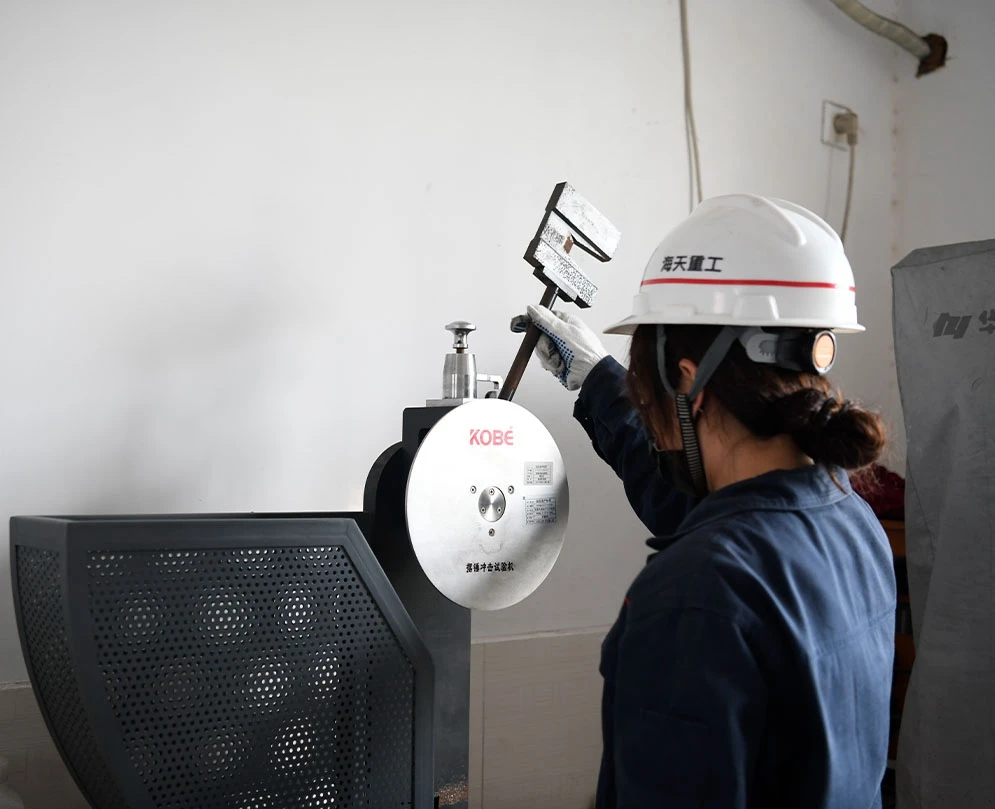
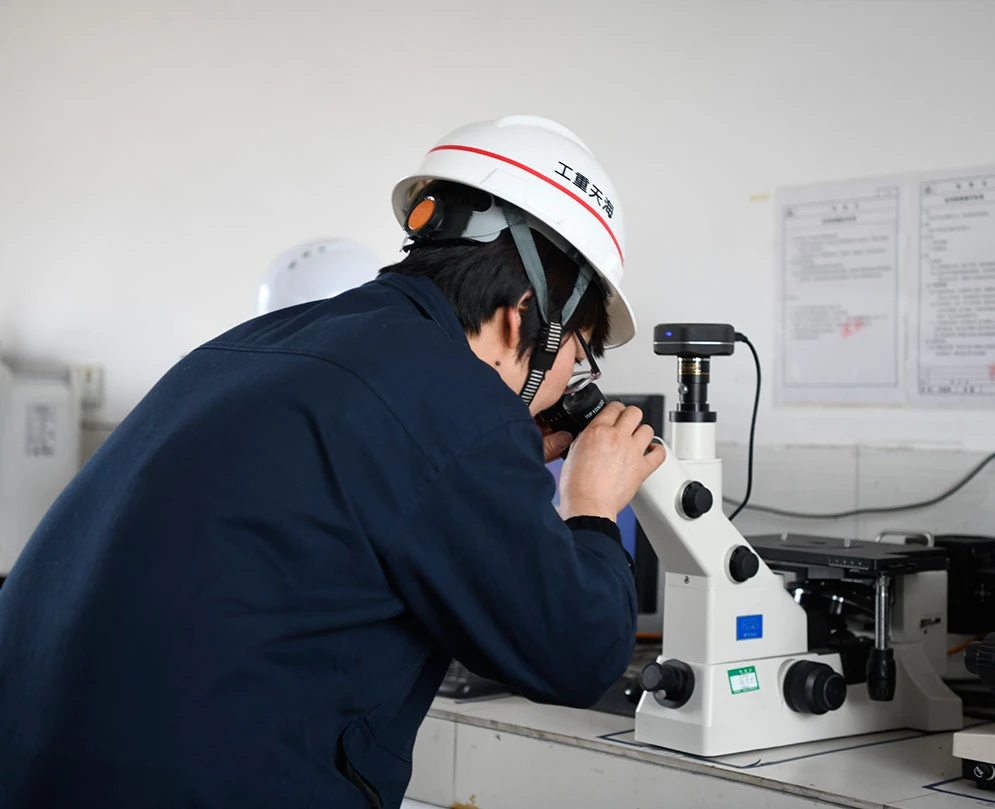
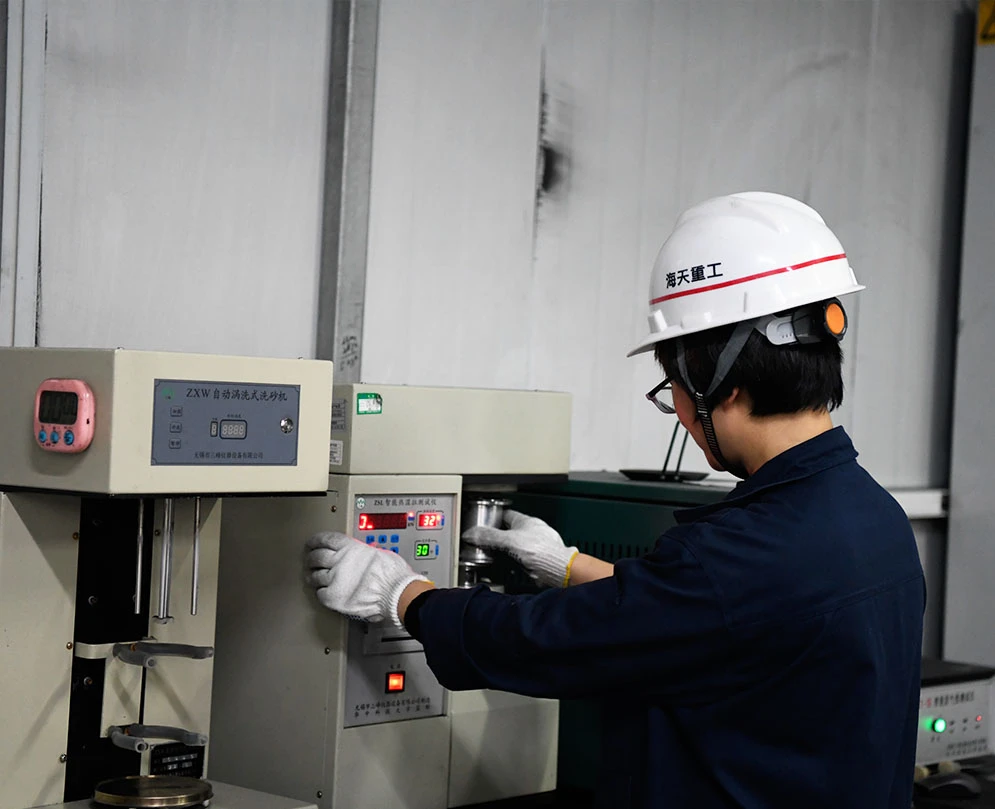
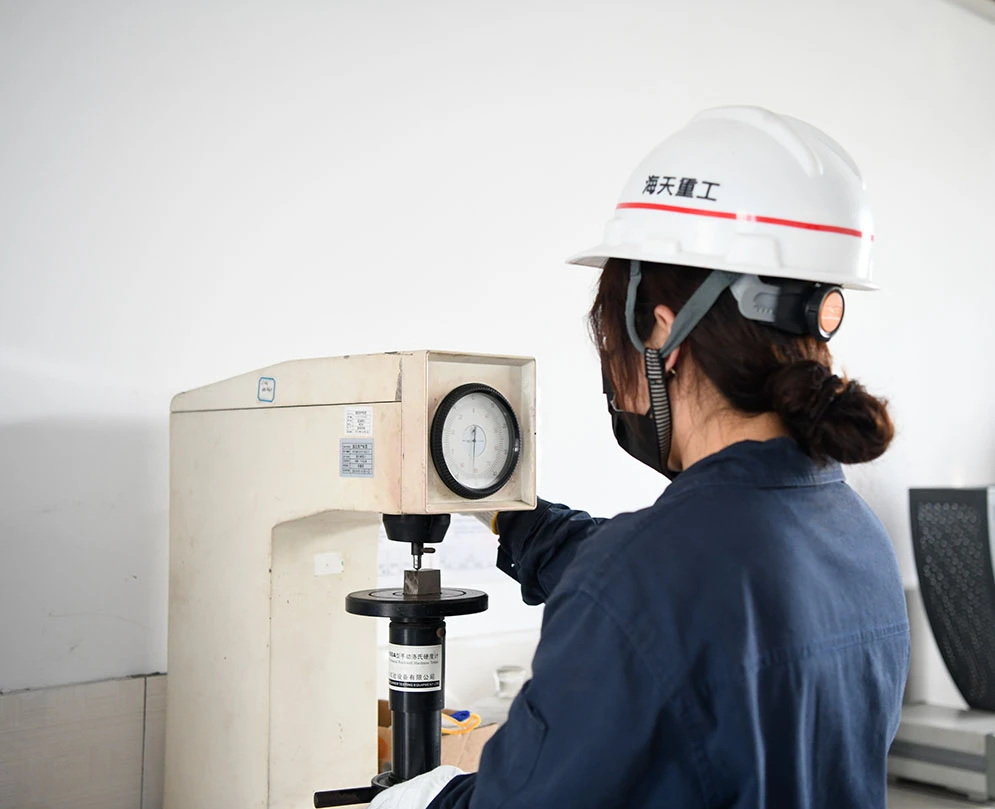
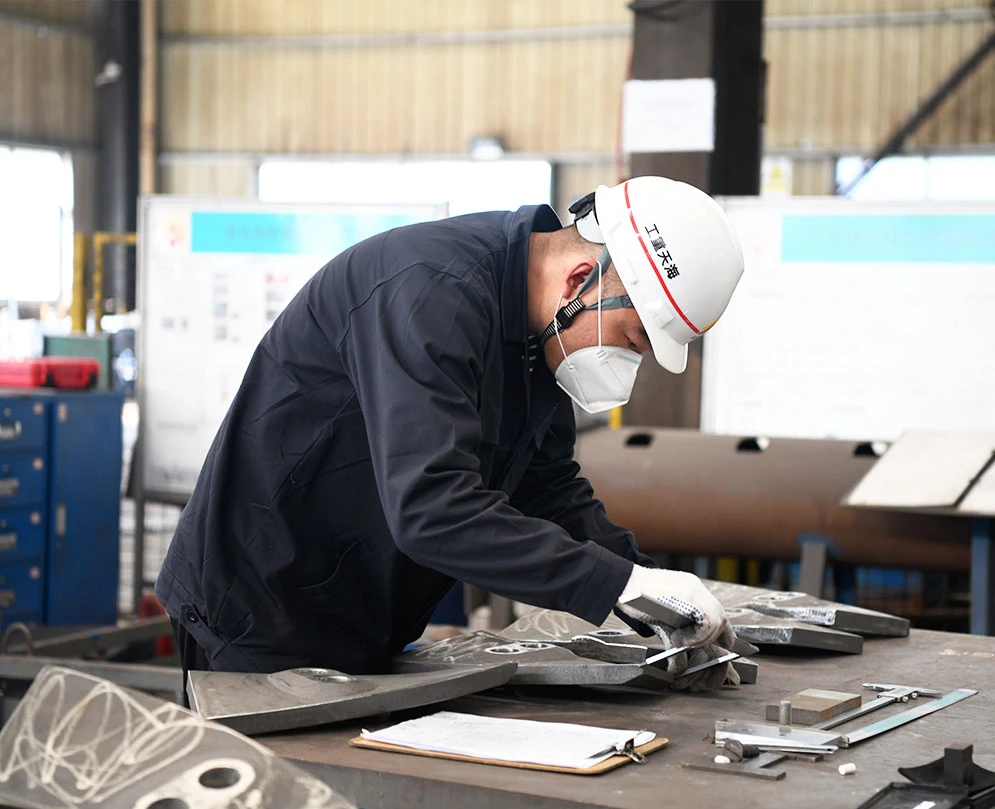
-
Controle van procesparameters
Temperatuurcontrole: Bewaak de temperatuur tijdens het smelten, gieten en warmtebehandeling om ervoor te zorgen dat het metaal binnen het juiste temperatuurbereik wordt behandeld om de productkwaliteit te garanderen.
Tijdcontrole: controleer de tijd van elk proces om ervoor te zorgen dat elk proces volledig wordt uitgevoerd zonder overdaad, om defecten te voorkomen.
Drukcontrole: Tijdens het giet- en vormproces worden de grootte en de drukverdeling gecontroleerd door vacuüm te trekken door een transparant membraan om de uniformiteit en stabiliteit van de metaalvloeistof die de mal vult te garanderen.
-
Toepassing van testapparatuur
Metallurgische microscoopdetectie: Observeer en analyseer de metaalstructuur om te detecteren of er defecten zoals poriën en insluitsels in het metaal aanwezig zijn.
Ultrasone detectie: Gebruik ultrasone technologie om defecten in het product te detecteren, zoals scheuren, insluitsels, enz., om de kwaliteit en betrouwbaarheid van het product te garanderen.
Hardheidstest: Test de hardheid van het product om te beoordelen of de slijtvastheid en mechanische eigenschappen aan de eisen voldoen.
-
Geautomatiseerde productieapparatuur
Geautomatiseerd controlesysteem: Gebruik geavanceerde geautomatiseerde controlesystemen om het productieproces te bewaken, nauwkeurige controle en aanpassing van productieparameters te bereiken en de productconsistentie en stabiliteit te verbeteren.
-
Handmatige kwaliteitscontrole
Inspectie van procestechnici: Procestechnici inspecteren regelmatig de productielijn om er zeker van te zijn dat de apparatuur normaal werkt en dat de productieparameters aan de vereisten voldoen.
Toezicht op de werking van de procesoperator: houdt toezicht op de werking van de procesoperator om ervoor te zorgen dat de werking gestandaardiseerd en nauwkeurig is, en om de impact van operationele fouten op de productkwaliteit te verminderen.
-
Data-analyse en verbetering
Verzameling en analyse van kwaliteitsgegevens: Verzamel verschillende kwaliteitsgegevens in het productieproces, voer statistische analyses uit, vind tijdig problemen en neem verbeteringsmaatregelen.
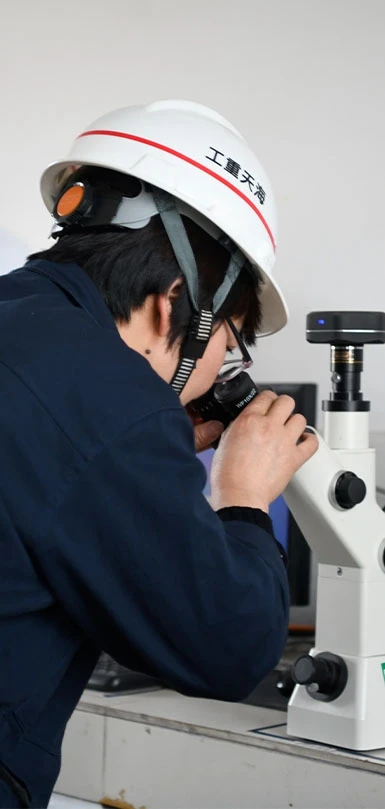
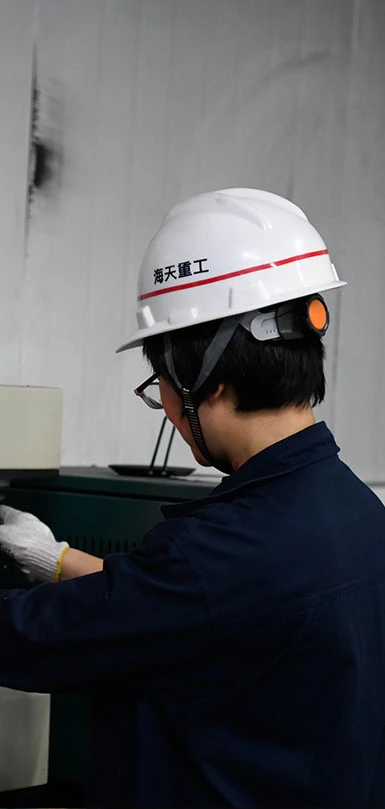
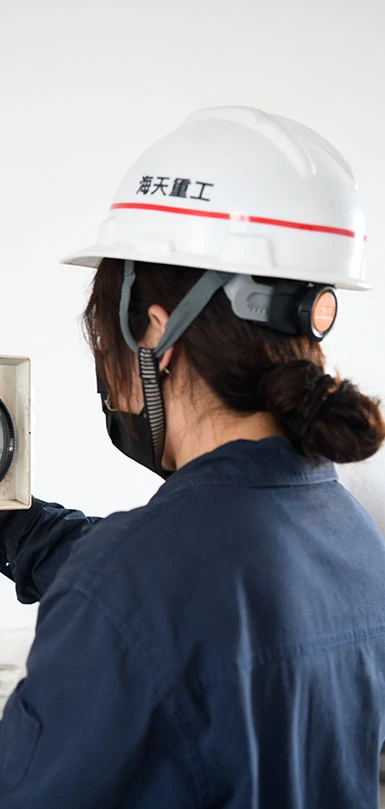
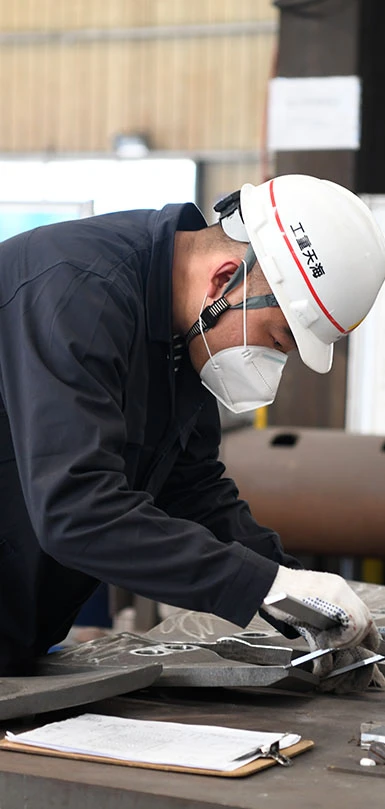
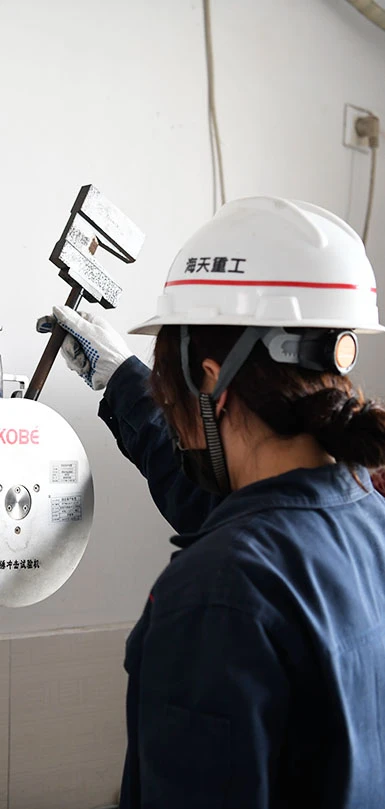
Bent u geïnteresseerd in onze producten of heeft u vragen, neem dan gerust contact met ons op.
Wij bieden professionele adviesdiensten en oplossingen op maat volgens uw behoeften.
STUUR NU EEN AANVRAAGContactgegevens
Telefoon: 0555-71661667166199
Fax: 0555-6971198
Website: https://www.htwearparts.com
E-mail: info@mashthi.com
Postcode: 243141
Adres: Xinshi Industrial Park, Bowang District, Ma'anshan City, provincie Anhui, China