Capacidade de produção
A empresa está profundamente envolvida na indústria de fundição há 20 anos. O centro de pesquisa e desenvolvimento é um centro tecnológico de dois andares com área de construção de mais de 1.200 metros quadrados. É um centro provincial de tecnologia empresarial e design industrial. O centro de tecnologia está equipado com espectrômetro de leitura direta ARL2460 importado, instrumento de medição do sistema de magnetização de saturação, máquina de teste de material universal WFW-600, máquina de teste de impacto JB30B, testador de características de resfriamento, microscópio metalográfico óptico, detector de areia e outros instrumentos e equipamentos de teste avançados em casa e no exterior, com capacidades de design inovadoras. Linha de produção vertical, linha de produção de espuma perdida, fundição de núcleo frio, linha de produção de impressão 3D. A pesquisa e desenvolvimento de produtos abrange de 0,5 kg a 8.000 kg, correspondendo à linha de moldagem para produtos em lote e à linha manual para produtos pesados de peça única. Existem máquinas de gravação que podem gravar moldes de madeira e equipamentos de impressão 3D que podem imprimir núcleos de areia para vazamento, reduzindo o tempo de abertura do molde. A empresa passou na certificação do sistema de qualidade 1SO9001 e o processo de produção está equipado com pessoal de inspeção profissional, inspeção final e inspeção de remessa. A taxa de cobertura da inspeção final do produto chega a 100%, o que efetivamente garante a qualidade e estabilidade dos produtos da empresa.
-
20
20 anos de experiência na indústria de fundição
-
1200M2
Área construída de mais de 1.200 metros quadrados
-
100%
A taxa de cobertura da inspeção final do produto chega a 100%
-
Linha de moldagem vertical DISA
Capacidade de produção: Normalmente na faixa de 100-150 peças fundidas por hora, dependendo do tamanho e da complexidade da peça fundida.
Tamanho do molde: Moldes adequados para peças fundidas de pequeno a médio porte, com tamanho máximo de molde de aproximadamente 335 x 335 mm.
Método de Moldagem: Moldagem vertical, utilizando a tecnologia de moldagem de alta pressão da DISA. -
Linha de moldagem de espuma perdida
Capacidade de produção: Geralmente na faixa de 50-100 peças fundidas por hora, dependendo do tamanho e da complexidade da peça fundida.
Tamanho do molde: Adequado para espuma perdida maior, geralmente o tamanho máximo do molde pode chegar a 500 x 500 mm ou maior.
Método de fundição: Fundição de espuma perdida, utilizando espuma perdida por fusão a gás em alta temperatura, capaz de produzir formas complexas e peças fundidas de alta precisão. -
Linha de produção do método V
Capacidade de produção: O peso das peças fundidas produzidas por hora é de cerca de 10-20 toneladas (dependendo do tamanho da peça fundida e dos parâmetros do processo)
Tamanho da peça fundida: O tamanho máximo pode chegar a 3.000 mm x 2.000 mm x 1.500 mm (pode ser personalizado de acordo com a necessidade)
Número de moldes: Design de vários moldes, pode ser configurado de acordo com as necessidades de produção. -
Linha de produção de jateamento de corrente de acumulação
Capacidade de jateamento: Cada máquina de jateamento tem uma capacidade de jateamento de 180-200 kg por minuto
Potência da máquina de jateamento: Cada máquina de jateamento tem uma potência de 11-15 kW e a potência total é de 88-120 kW
Velocidade de jateamento: 70-80 m/s. -
Linha de produção de moldagem de núcleo frio
Capacidade de produção: A capacidade de produção é geralmente entre 30-60 peças fundidas por hora, dependendo do tamanho e complexidade da peça fundida.
Tamanho do molde: Adequado para moldes de médio a grande porte, geralmente o tamanho máximo do molde pode atingir 400 x 400 mm ou maior.
Método de fundição: Fundição de núcleo frio, usando processo de núcleo frio, capaz de produzir peças fundidas complexas e de alta precisão.
Nível de automação: Possui alto nível de automação, incluindo funções automáticas de carregamento de molde, conformação, vazamento, resfriamento e desmoldagem. -
Linha de produção de tratamento térmico de forno de túnel de gás
Estrutura do forno: Tijolos refratários de alta resistência, casca é placa de aço de alta resistência
Tamanho do forno: Personalizado de acordo com necessidades específicas, geralmente de 1,5 metros a 3 metros de altura, 1 metro a 2,5 metros de largura
Volume do forno: cerca de 3 metros cúbicos. -
Sistema de armazenamento estereoscópico de controle inteligente de armazém não tripulado
WMS (Warehouse Management System): Fornece funções como gerenciamento de estoque, processamento de pedidos, instruções de separação, armazenamento e operações de saída
WCS (Sistema de Controle de Armazém): Monitoramento em tempo real do status operacional de equipamentos automatizados e otimização da programação de equipamentos
Interface de operação: Tela sensível ao toque ou interface de controle de computador, suporta monitoramento e gerenciamento remotos. -
A linha de produção vertical
Capacidade de produção: 90-120 conjuntos por hora (dependendo das condições específicas de produção)
Tamanho da moldagem: O tamanho padrão é 450 mm x 600 mm x 150-350 mm (largura x comprimento x altura), pode ser personalizado de acordo com as necessidades
Velocidade de moldagem: 20-25 segundos/molde -
Forno de média frequência
Capacidade de fusão: Dependendo do tamanho do forno, geralmente entre 5 toneladas e 15 toneladas
Tempo de fusão: Cerca de 1-2 horas (dependendo do material e da capacidade)
Temperatura máxima de fusão: 1600°C a 1800°C (dependendo do material específico) -
Estação de trabalho de polimento robótica
Tipo de ferramenta de moagem: Moedor elétrico ou pneumático (opcional)
Velocidade de moagem: Ajustável, normalmente variando de 1.000 a 5.000 RPM
Número de cabeças de retificação: Simples ou múltiplas (dependendo da configuração) -
Equipamento de impressão 3D
Tamanho principal da máquina: 9000 × 1900 × 1950 mm (comprimento × largura × altura). O tempo de impressão da caixa completa é de cerca de 12 horas. A configuração padrão é de duas caixas de areia funcionais, que podem atingir impressão ininterrupta de 24 horas.
O tamanho interno da caixa de areia de trabalho é 1800 × 1000 × 730 mm (comprimento × largura × altura), o que atende às necessidades de impressão da maioria dos moldes de areia para fundição.
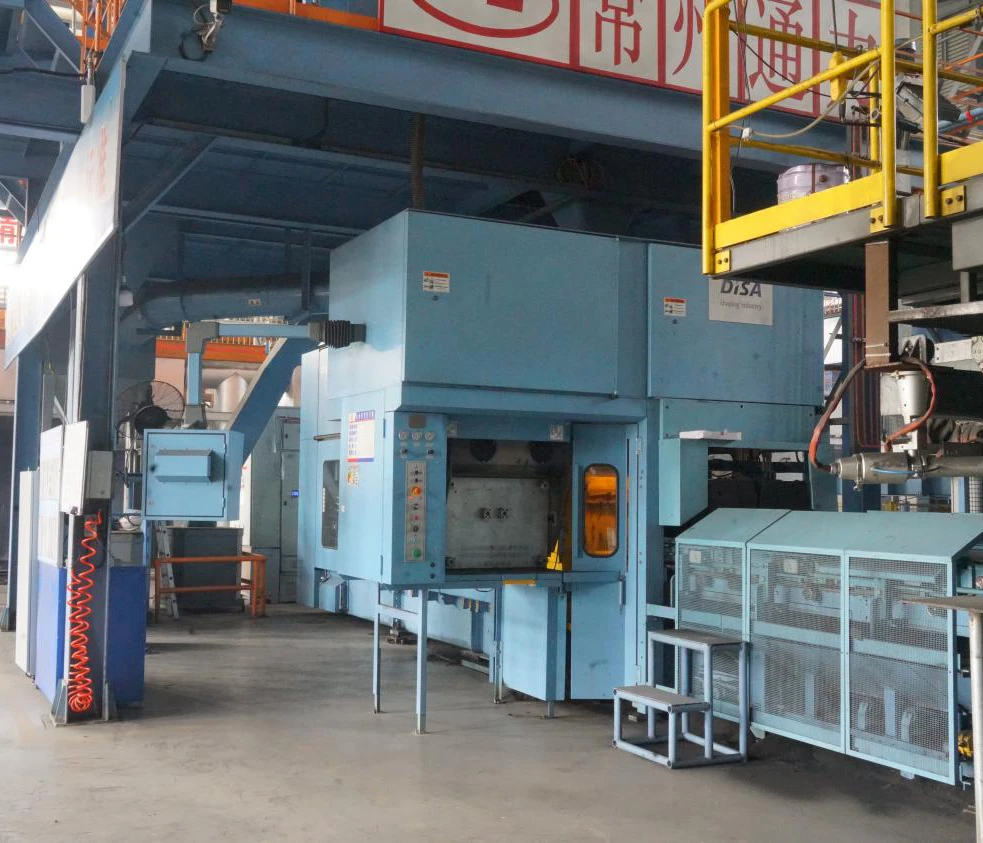
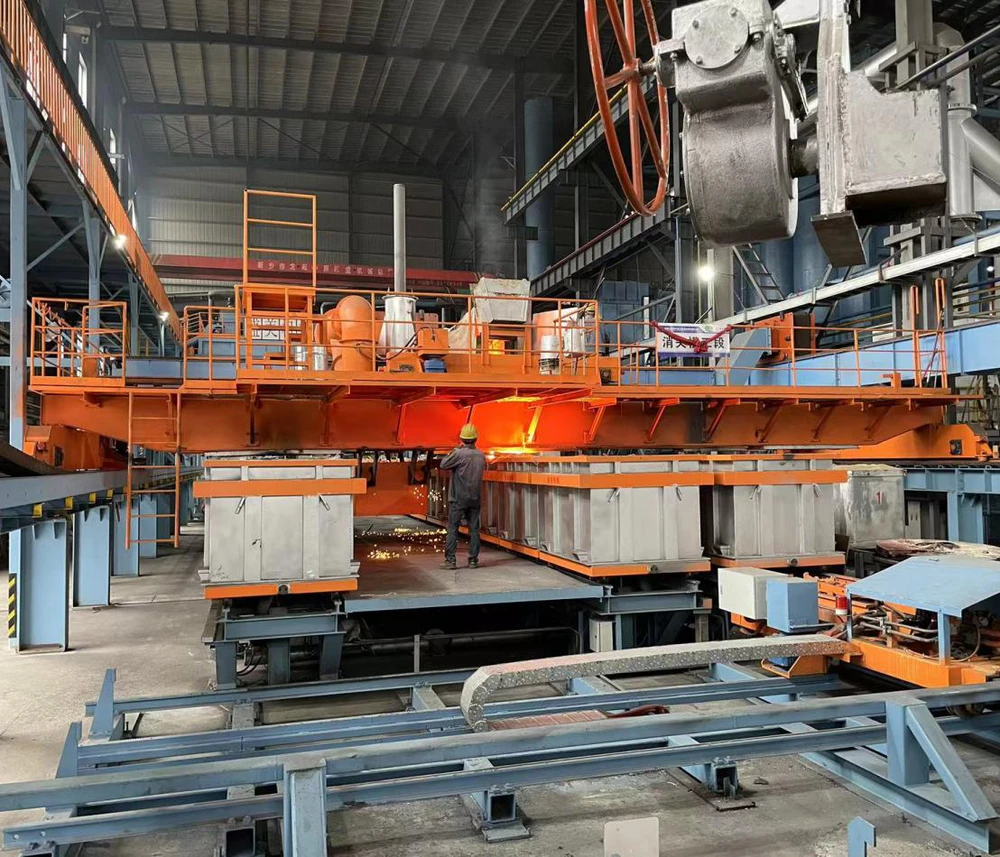
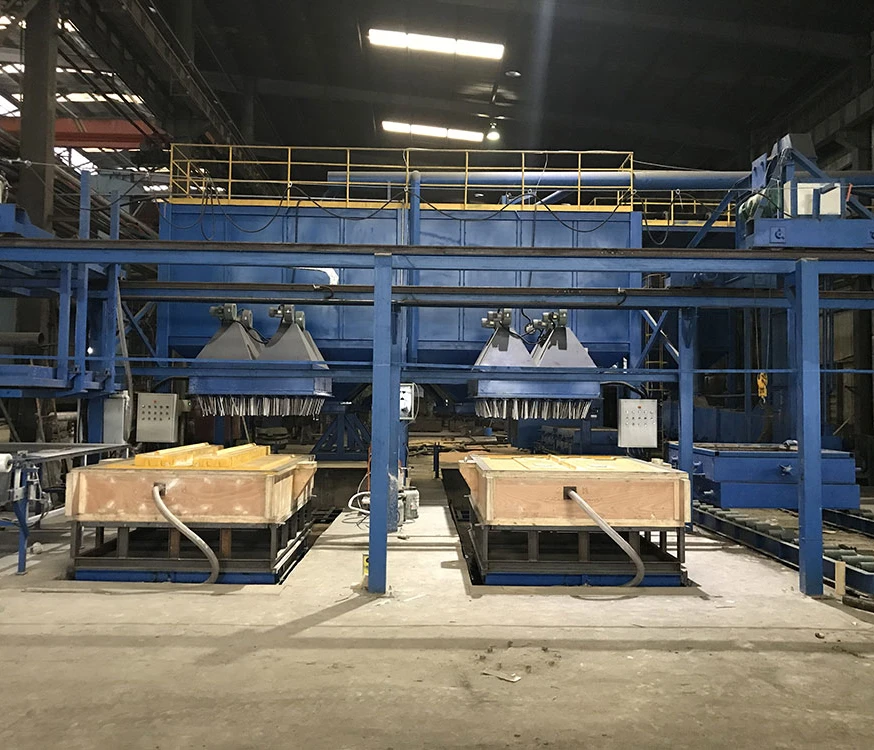
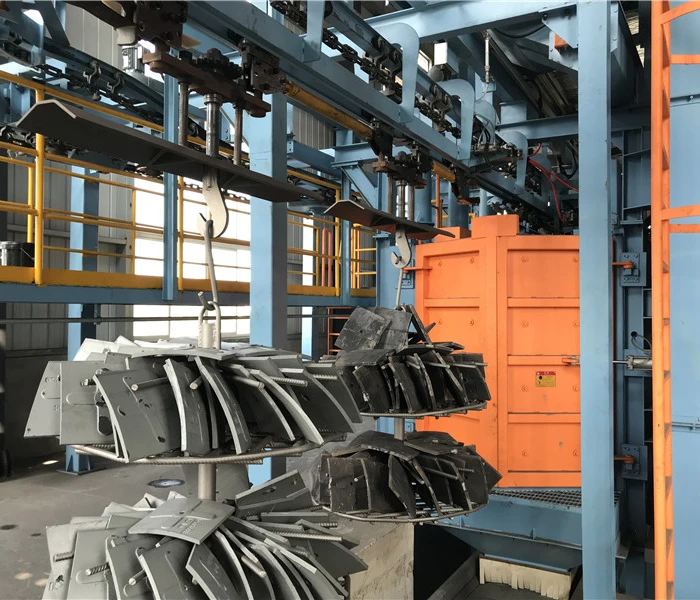
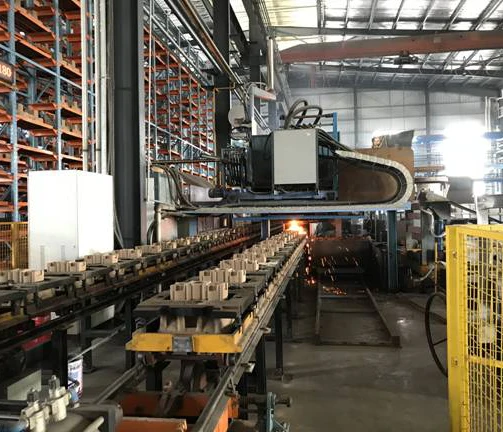
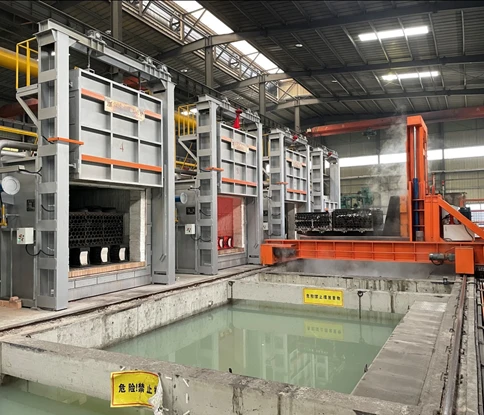
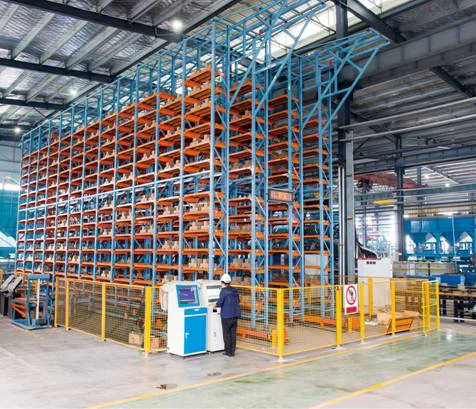
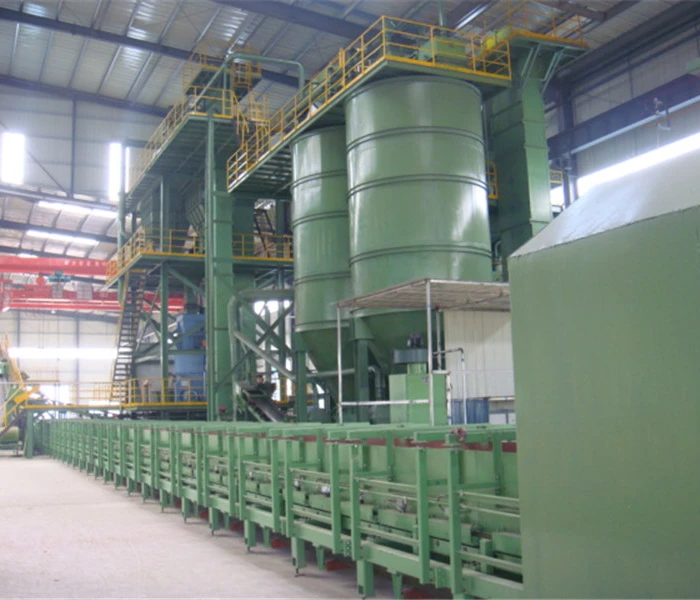
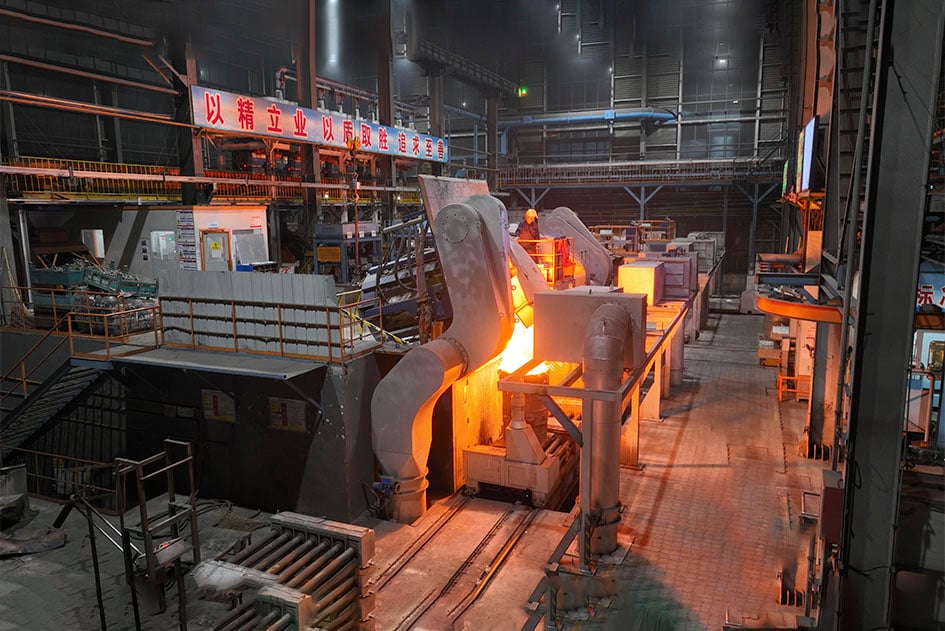
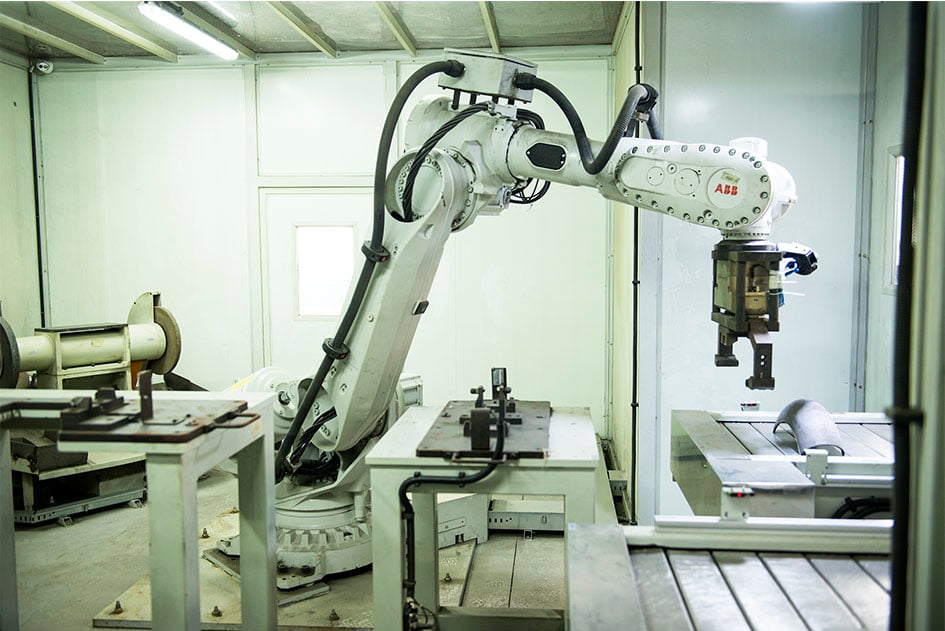
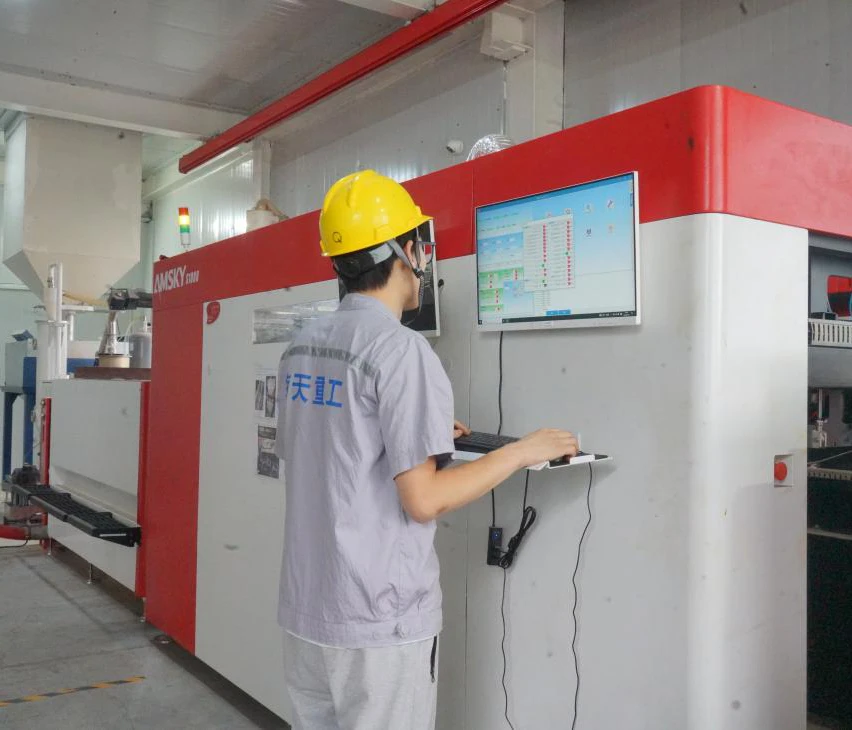
EQUIPAMENTO DE TESTE
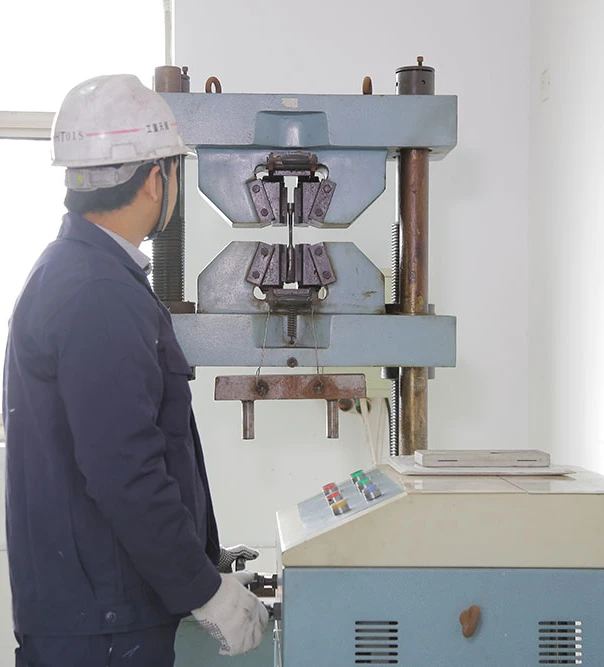
Equipamento de teste de tração

Equipamento de teste de energia de impacto
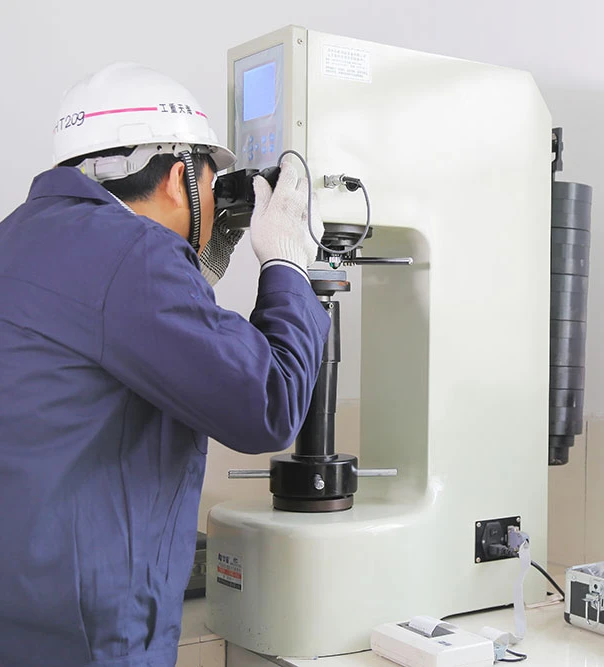
Equipamento de teste de dureza Brinell
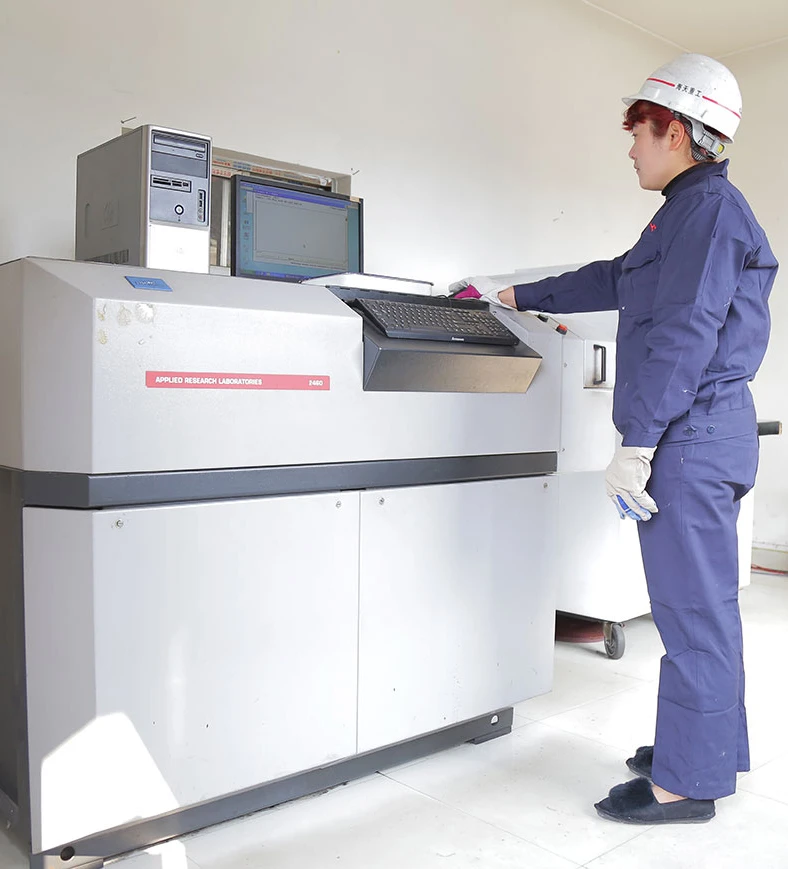
Equipamento de detecção de componentes espectrômetros
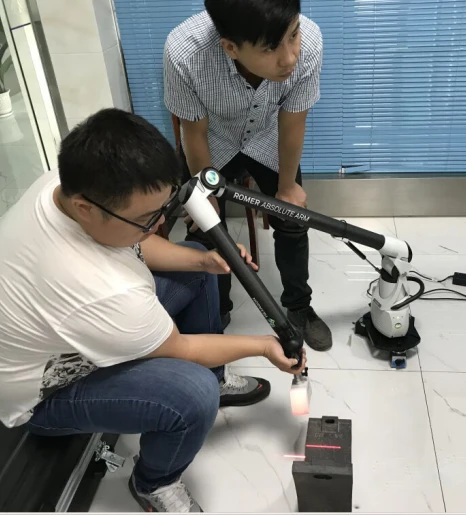
Máquina de medição de coordenadas de triangulação
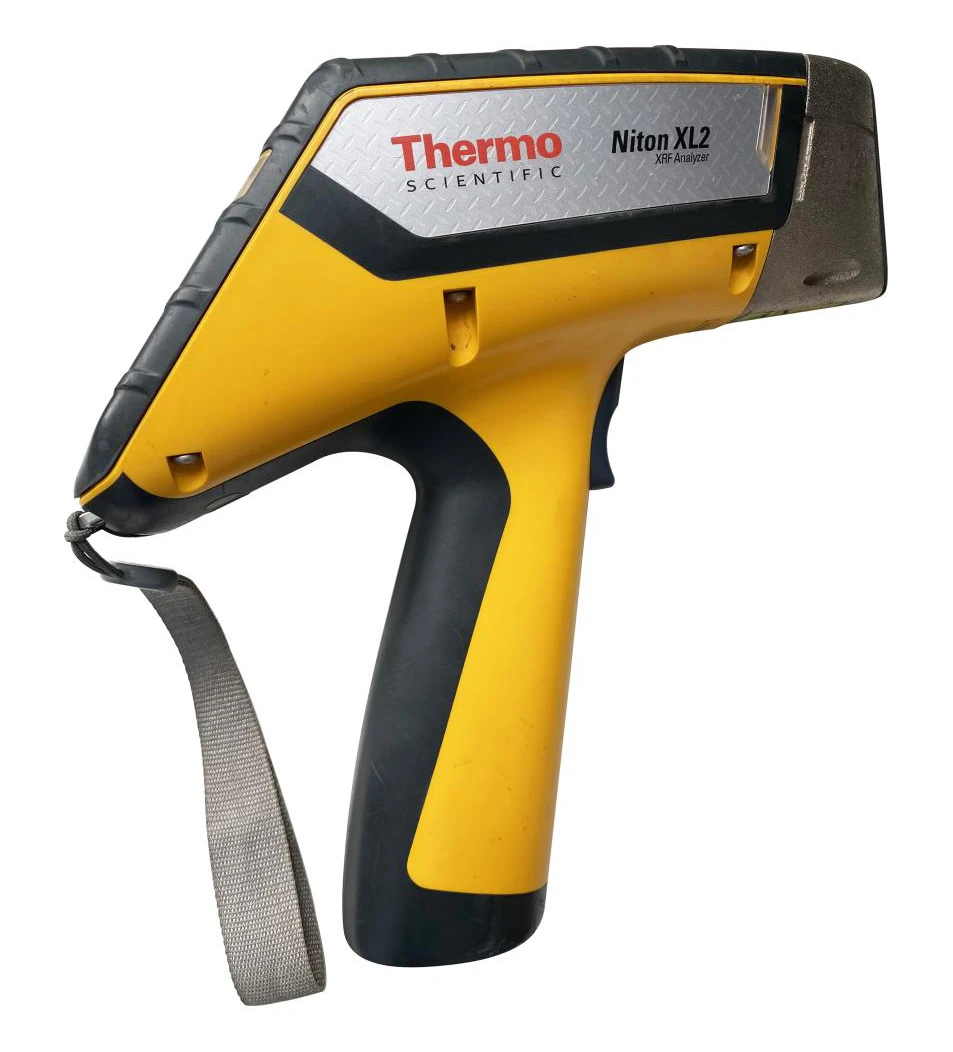
Espectrômetro portátil
FIIO DO PROCESSO
-
01
Seleção de matéria-prima
No processo de fabricação de peças resistentes ao desgaste, a seleção das matérias-primas é crucial. Selecionamos cuidadosamente materiais de liga de alta qualidade para garantir que tenham excelente resistência ao desgaste e resistência, estabelecendo uma base sólida para a qualidade dos produtos.
-
02
Processo de fusão
Depois que as matérias-primas estritamente proporcionadas entram no forno, usamos tecnologia de fundição avançada para garantir que a composição e a temperatura do metal fundido atinjam o estado ideal, proporcionando fluxo de metal uniforme e estável para a moldagem do produto.
-
03
Fundição e moldagem
Através do requintado processo de fundição, o metal fundido é injetado no molde para solidificar e moldar em um formato e tamanho específicos. Nossos artesãos foram treinados profissionalmente e são proficientes em vários processos complexos de moldagem para garantir que a forma e o tamanho dos produtos sejam precisos e a qualidade estável.
-
04
Jateamento e moagem
Após a desmoldagem, o produto passa por um processo de lixamento fino para remover defeitos superficiais e rebarbas, tornando sua superfície lisa e plana. Nossos artesãos utilizam técnicas delicadas e excelentes habilidades para cuidar de cada produto e dar-lhe aparência e textura perfeitas.
-
05
Processo de tratamento térmico
Após o processo de tratamento térmico, a estrutura e o desempenho do produto são ainda mais estabilizados e melhorados. De acordo com os requisitos específicos do produto, utilizamos diferentes processos de tratamento térmico para que ele tenha excelente resistência ao desgaste, resistência e resistência à corrosão, e se adapte às necessidades dos diversos ambientes de trabalho agressivos.
-
06
Pintura e inspeção
O produto é pintado, o que não só embeleza a aparência, mas também melhora a resistência à corrosão e ao desgaste de sua superfície. Depois disso, passa por um rigoroso processo de inspeção para garantir que todos os indicadores do produto atendam aos requisitos da norma e forneçam aos clientes garantias confiáveis do produto.
-
07
Entrada e entrega no armazém
Por fim, o produto passa por rigoroso controle de qualidade e fica armazenado com segurança no armazém, pronto para ser entregue a qualquer momento. Assim que recebermos o pedido do cliente, concluiremos a entrega no prazo, quantidade e qualidade para garantir que o produto seja entregue ao cliente com segurança e dentro do prazo.
CONTROLE DE QUALIDADE DURANTE A PRODUÇÃO
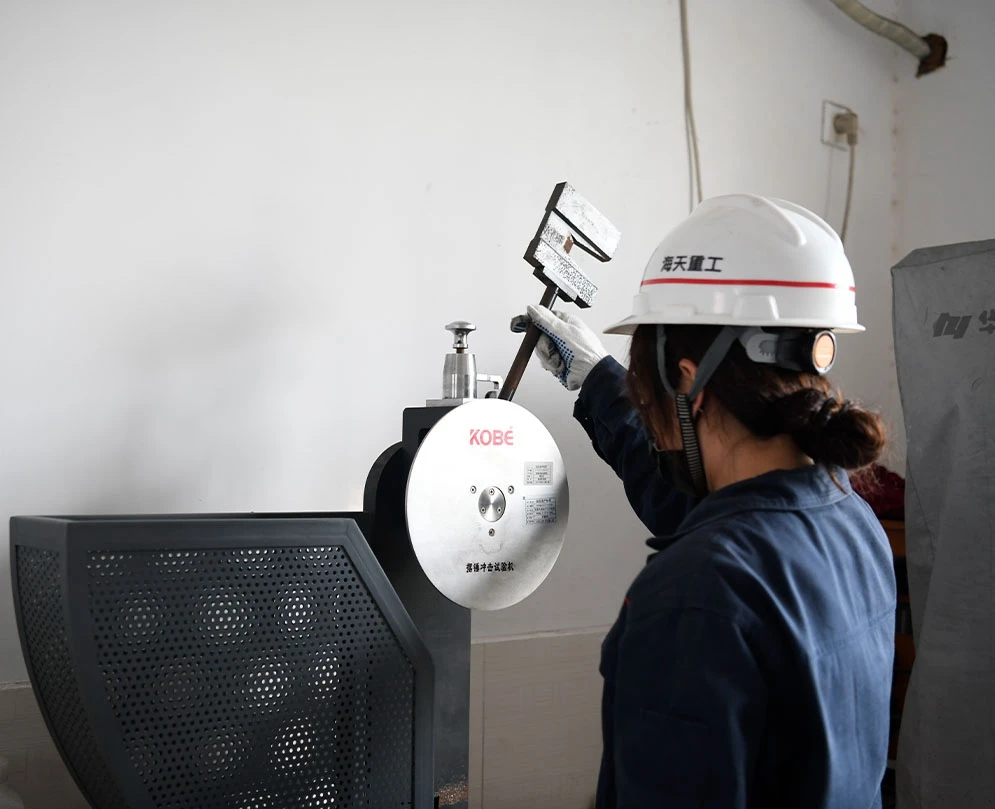
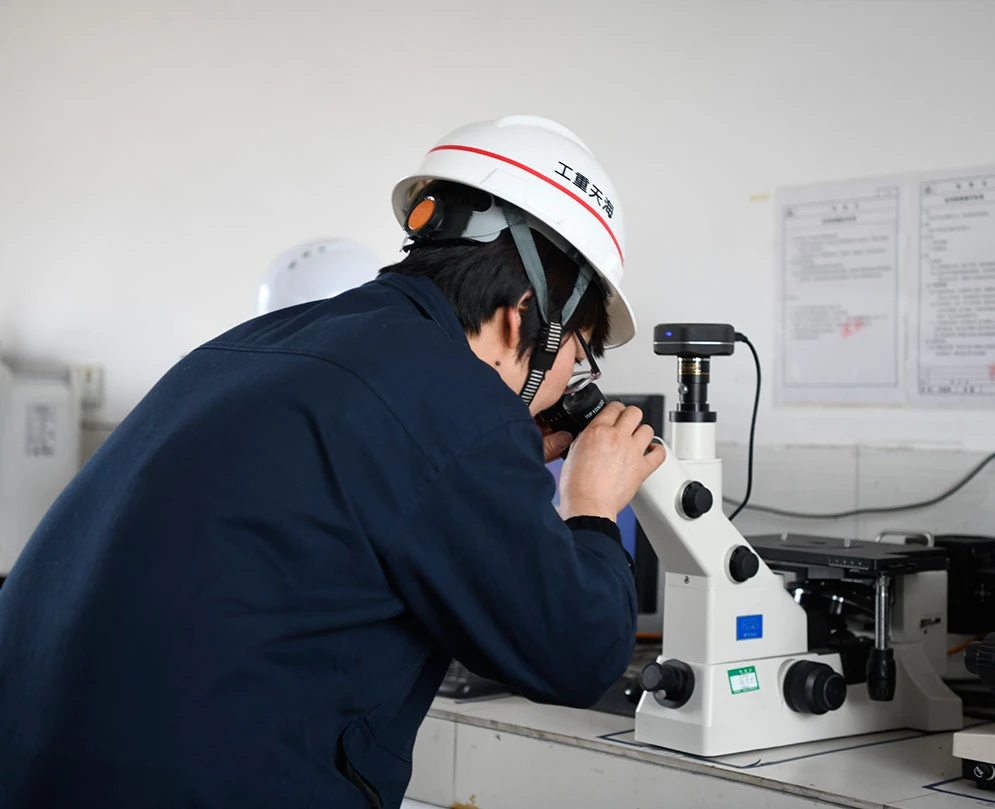
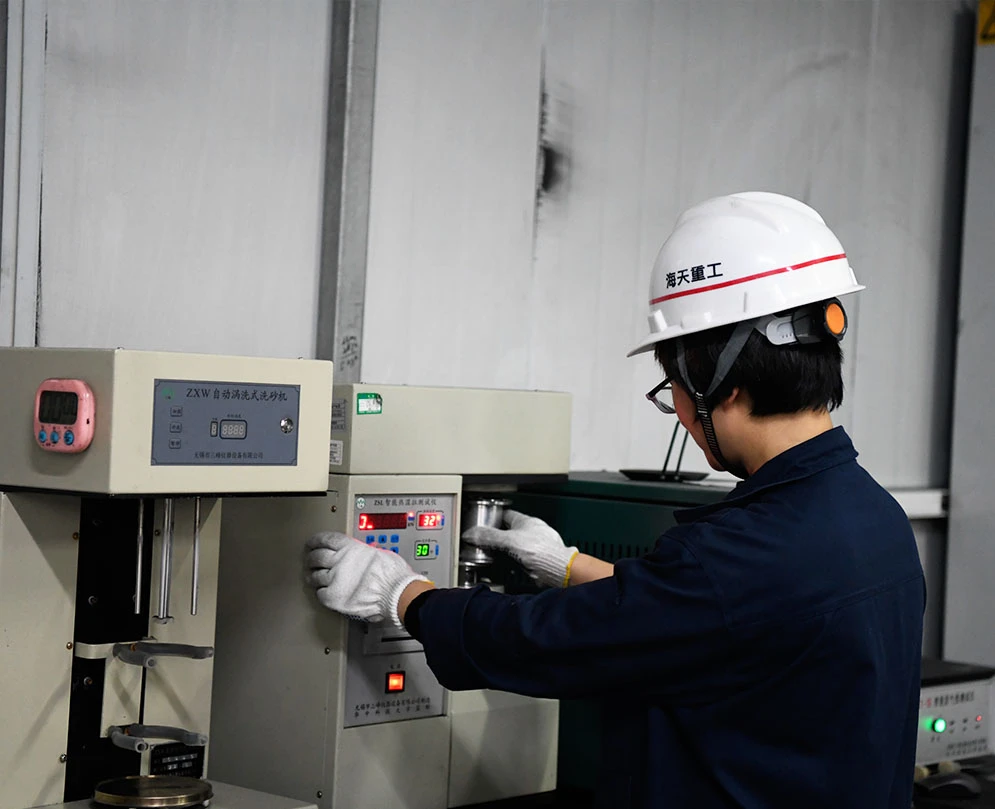
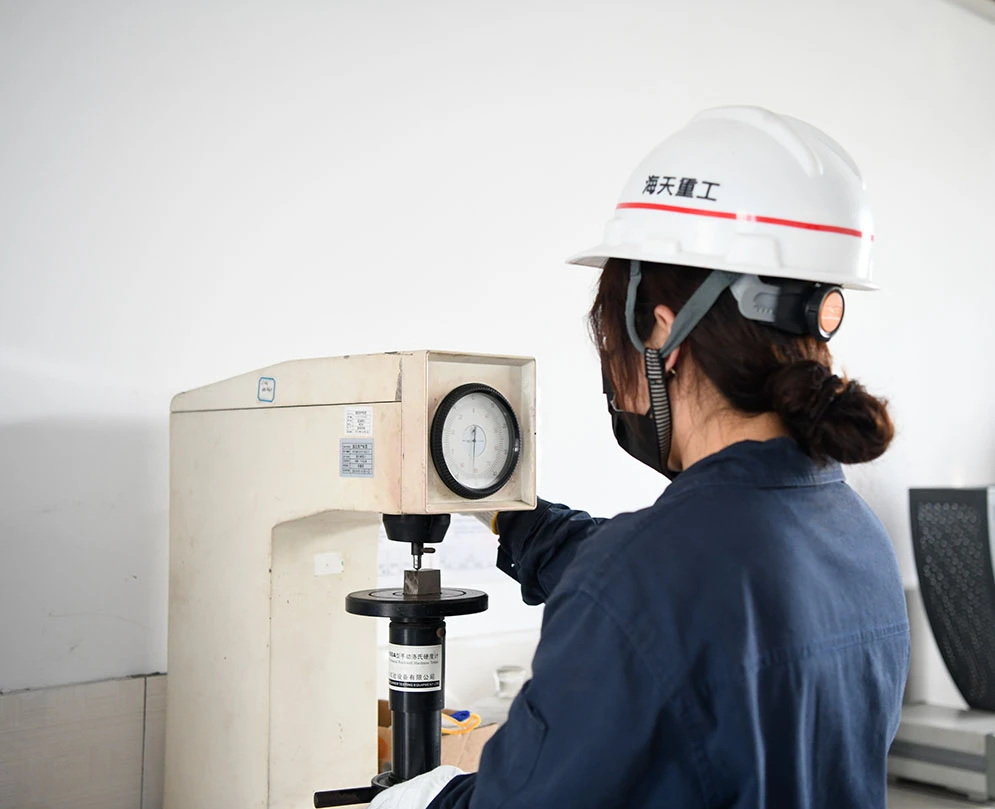
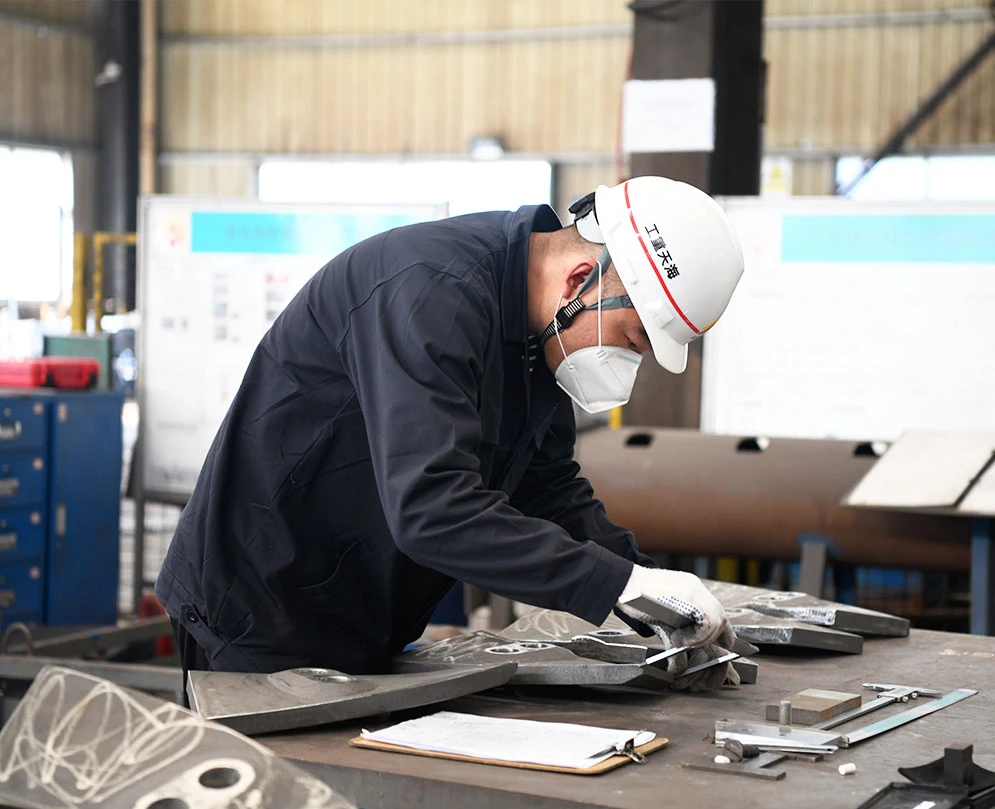
-
Controle de parâmetros de processo
Controle de temperatura: Monitore a temperatura durante a fundição, vazamento e tratamento térmico para garantir que o metal seja tratado dentro da faixa de temperatura apropriada para garantir a qualidade do produto.
Controle de tempo: Controle o tempo de cada processo para garantir que cada processo seja totalmente executado sem excessos para evitar defeitos.
Controle de pressão: Durante o processo de vazamento e moldagem, o tamanho e a distribuição da pressão são controlados por aspiração através de uma membrana transparente para garantir a uniformidade e estabilidade do líquido metálico que preenche o molde.
-
Aplicação de equipamentos de teste
Detecção por microscópio metalúrgico: Observe e analise a estrutura metálica para detectar se há defeitos como poros e inclusões dentro do metal.
Detecção ultrassônica: Utilize tecnologia ultrassônica para detectar defeitos no interior do produto, como rachaduras, inclusões, etc., para garantir a qualidade e confiabilidade do produto.
Teste de dureza: Teste a dureza do produto para avaliar se sua resistência ao desgaste e propriedades mecânicas atendem aos requisitos.
-
Equipamento de produção automatizado
Sistema de controle automatizado: Use sistemas avançados de controle automatizado para monitorar o processo de produção, obter controle e ajuste precisos dos parâmetros de produção e melhorar a consistência e estabilidade do produto.
-
Controle de qualidade manual
Inspeção técnica de processo: Os técnicos de processo inspecionam regularmente a linha de produção para garantir que o equipamento esteja operando normalmente e que os parâmetros de produção atendam aos requisitos.
Supervisão da operação do operador de processo: Supervisionar a operação do operador de processo para garantir que a operação seja padronizada e precisa e reduzir o impacto de erros operacionais na qualidade do produto.
-
Análise e melhoria de dados
Coleta e análise de dados de qualidade: Colete vários dados de qualidade no processo de produção, conduza análises estatísticas, encontre problemas a tempo e tome medidas de melhoria.
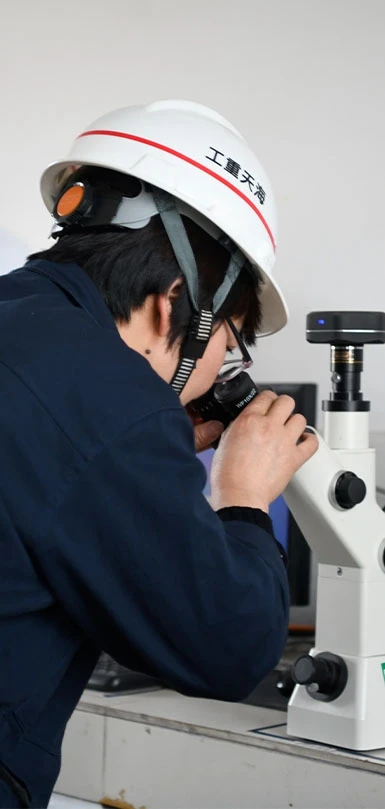
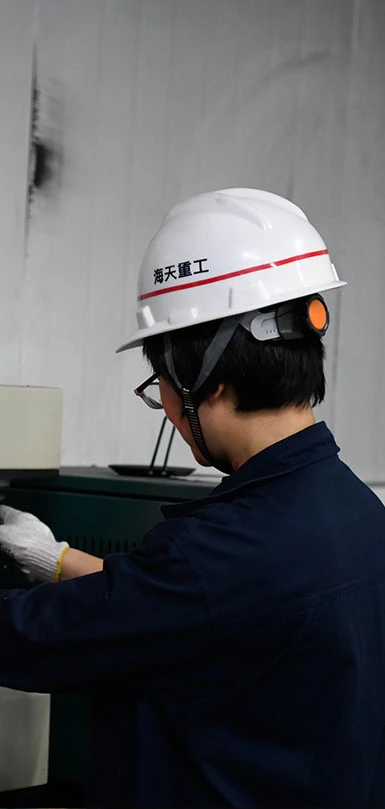
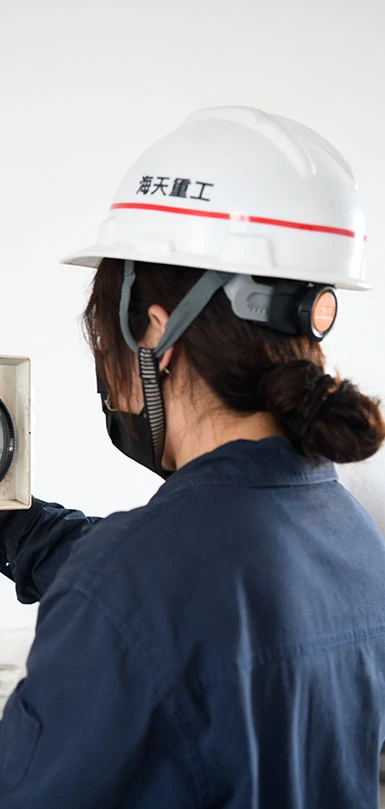
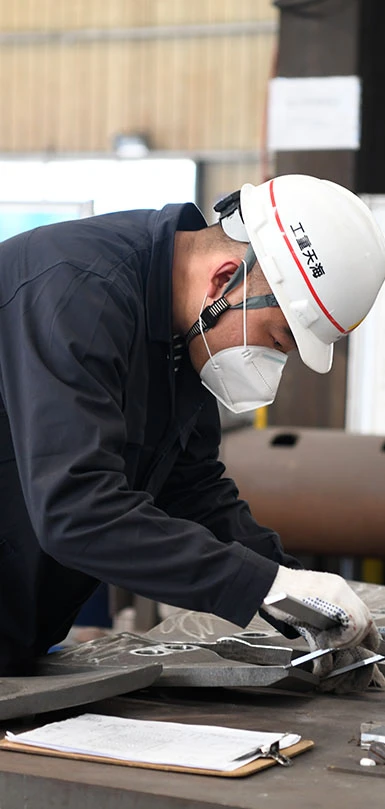
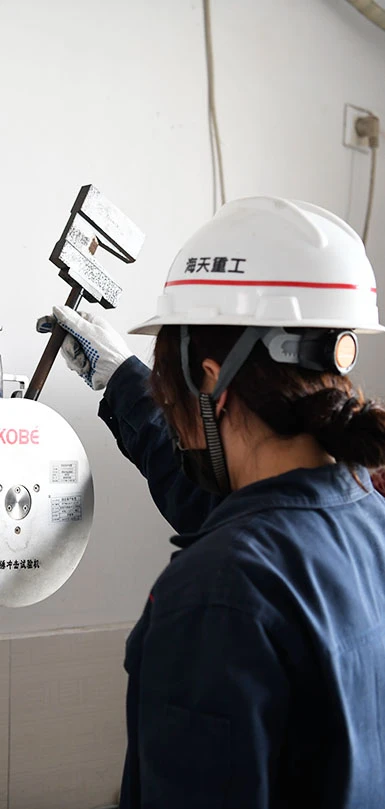
Se você estiver interessado em nossos produtos ou tiver alguma dúvida, não hesite em nos contatar.
Forneceremos serviços de consultoria profissional e soluções customizadas de acordo com suas necessidades.
ENVIAR INQUÉRITO AGORAInformações de contato
Telefone: 0555-71661667166199
Fax: 0555-6971198
Site: https://www.htwearparts.com
E-mail: info@mashthi.com
Código postal: 243141
Endereço: Parque Industrial Xinshi, distrito de Bowang, cidade de Ma'anshan, província de Anhui, China