Производственная мощность
Компания уже 20 лет активно работает в литейной отрасли. Научно-исследовательский центр представляет собой двухэтажный технологический центр площадью застройки более 1200 квадратных метров. Это провинциальный центр технологий и промышленного дизайна. Технологический центр оснащен импортным спектрометром прямого считывания ARL2460, прибором для измерения системы намагничивания насыщения, универсальной машиной для испытания материалов WFW-600, машиной для испытания на удар JB30B, тестером характеристик охлаждения, оптическим металлографическим микроскопом, детектором песка и другими современными испытательными приборами и оборудованием в домашних условиях. и за рубежом, с инновационными возможностями дизайна. Вертикальная производственная линия, линия по производству пенопласта, холодное литье оболочек, производственная линия для 3D-печати. Исследования и разработки продукции охватывают от 0,5 до 8000 кг, что соответствует линии формования серийных изделий и ручной линии для штучных тяжелых изделий. Существуют гравировальные станки, которые могут гравировать деревянные формы, и оборудование для 3D-печати, которое может печатать песчаные стержни для заливки, сокращая время открытия формы. Компания прошла сертификацию системы качества 1SO9001, а производственный процесс оснащен профессиональным персоналом по проверке, окончательной проверке и проверке отгрузки. Степень охвата окончательной проверкой продукции достигает 100%, что эффективно гарантирует качество и стабильность продукции компании.
-
20
20 лет опыта работы в литейном производстве
-
1200М2
Площадь здания более 1200 квадратных метров.
-
100%
Степень охвата окончательной проверкой продукции достигает 100 %.
-
Вертикальная формовочная линия DISA
Производственная мощность: Обычно 100-150 отливок в час, в зависимости от размера и сложности отливки.
Размер формы: формы подходят для отливок малого и среднего размера, максимальный размер формы составляет примерно 335 x 335 мм.
Метод формования: Вертикальное формование с использованием технологии формования под высоким давлением DISA. -
Линия формования пенопласта по выплавляемым моделям
Производственная мощность: Обычно в пределах 50-100 отливок в час, в зависимости от размера и сложности отливки.
Размер формы: подходит для больших объемов пенопласта, обычно максимальный размер формы может достигать 500 x 500 мм или больше.
Метод литья: литье по выплавляемым моделям с использованием высокотемпературного газового плавления пенопласта, способное производить сложные формы и высокоточные отливки. -
Производственная линия V-метода
Производственная мощность: Вес отливок, выпускаемых в час, составляет около 10-20 тонн (в зависимости от размера отливки и технологических параметров).
Размер отливки: максимальный размер может достигать 3000 x 2000 x 1500 мм (может быть настроен в соответствии с потребностями).
Количество пресс-форм: конструкция с несколькими пресс-формами может быть настроена в соответствии с производственными потребностями. -
Накопительная цепная дробеструйная линия
Производительность дробеструйной обработки: каждая дробеструйная машина имеет производительность дробеструйной обработки 180-200 кг в минуту.
Мощность дробеструйной машины: Каждая дробеструйная машина имеет мощность 11-15 кВт, общая мощность 88-120 кВт.
Скорость дробеструйной обработки: 70-80 м/с. -
Линия по производству холодного формования корпусов
Производственная мощность: Производственная мощность обычно составляет 30-60 отливок в час, в зависимости от размера и сложности отливки.
Размер формы: подходит для средних и больших форм, обычно максимальный размер формы может достигать 400 x 400 мм или больше.
Метод литья: Холодное литье в стержневую оболочку с использованием процесса холодной стержневой оболочки, позволяющее производить высокоточные и сложные отливки.
Уровень автоматизации: Он имеет высокий уровень автоматизации, включая автоматическую загрузку пресс-форм, функции формования, заливки, охлаждения и извлечения из формы. -
Линия термической обработки газовой туннельной печи
Конструкция печи: Высокопрочный огнеупорный кирпич, оболочка — высокопрочная стальная пластина.
Размер печи: Настраивается в соответствии с конкретными потребностями, обычно от 1,5 до 3 метров в высоту, от 1 до 2,5 метров в ширину.
Объем печи: около 3 куб.м. -
Беспилотный склад с интеллектуальным управлением, стереоскопическая система хранения
WMS (система управления складом): обеспечивает такие функции, как управление запасами, обработка заказов, инструкции по комплектованию, складирование и исходящие операции.
WCS (система управления складом): мониторинг рабочего состояния автоматизированного оборудования в режиме реального времени и оптимизация планирования работы оборудования.
Рабочий интерфейс: сенсорный экран или интерфейс управления компьютером, поддерживает удаленный мониторинг и управление. -
Будет вертикальная производственная линия
Производительность: 90-120 комплектов в час (в зависимости от конкретных условий производства)
Размер формовки: стандартный размер 450 x 600 x 150-350 мм (ширина x длина x высота), может быть настроен в соответствии с потребностями.
Скорость формования: 20-25 секунд/форма -
Среднечастотная печь
Плавильная мощность: В зависимости от размера печи, обычно от 5 до 15 тонн.
Время плавления: около 1-2 часов (в зависимости от материала и мощности)
Максимальная температура плавления: от 1600°C до 1800°C (в зависимости от конкретного материала). -
Роботизированная полировальная станция
Тип шлифовального инструмента: электрическая или пневматическая шлифовальная машина (опция).
Скорость шлифования: регулируемая, обычно от 1000 до 5000 об/мин.
Количество шлифовальных головок: одна или несколько (в зависимости от конфигурации) -
оборудование для 3D-печати
Размер основной машины: 9000 × 1900 × 1950 мм (длина × ширина × высота). Полное время печати коробки составляет около 12 часов. Стандартная конфигурация — две рабочие песочницы, обеспечивающие бесперебойную печать в течение 24 часов.
Внутренний размер рабочей песочницы составляет 1800 × 1000 × 730 мм (длина × ширина × высота), что соответствует потребностям печати большинства форм для литья песка.
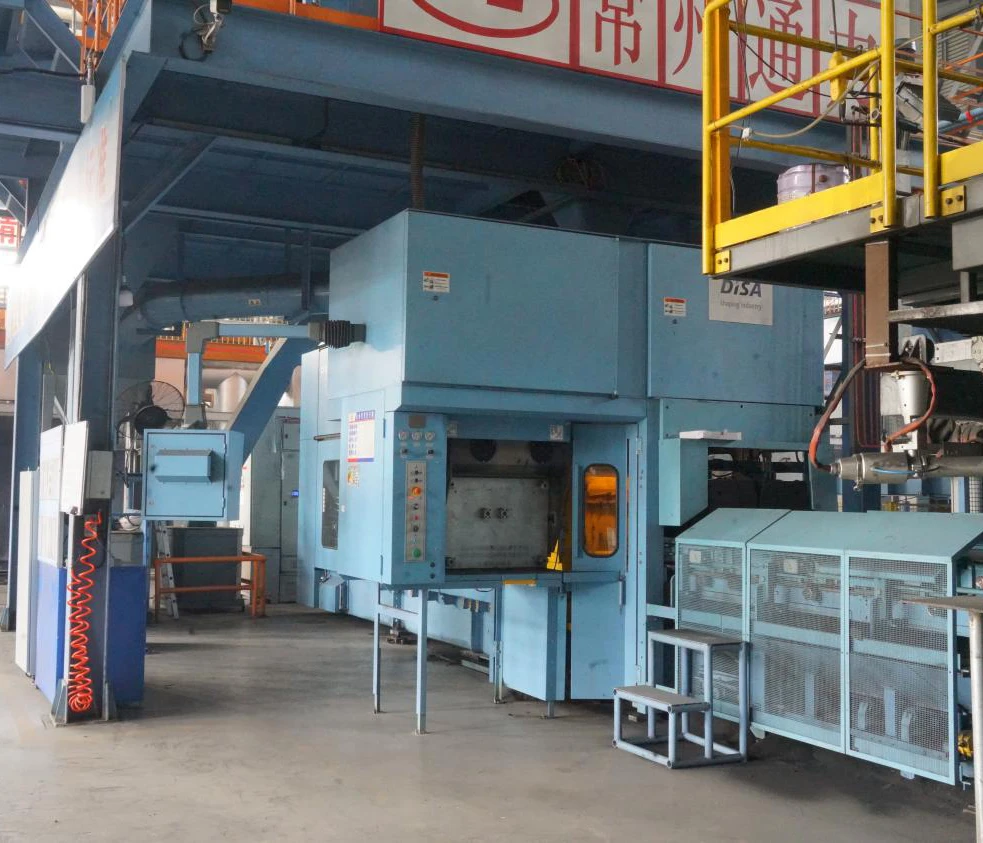
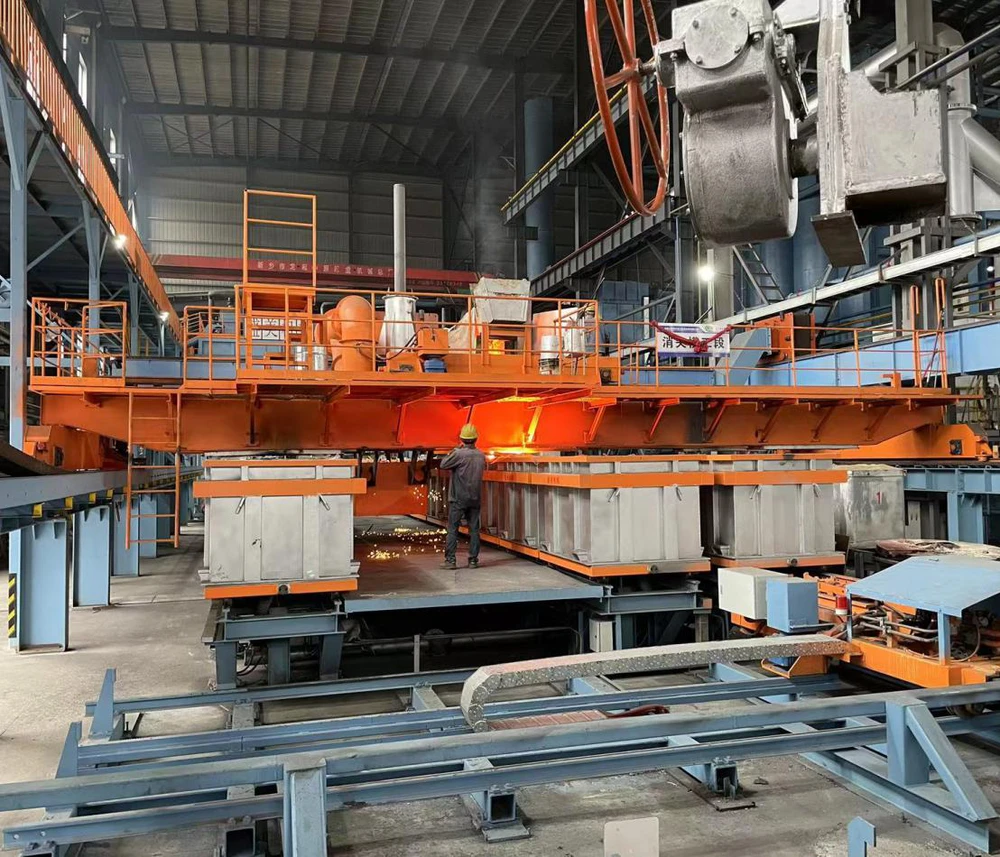
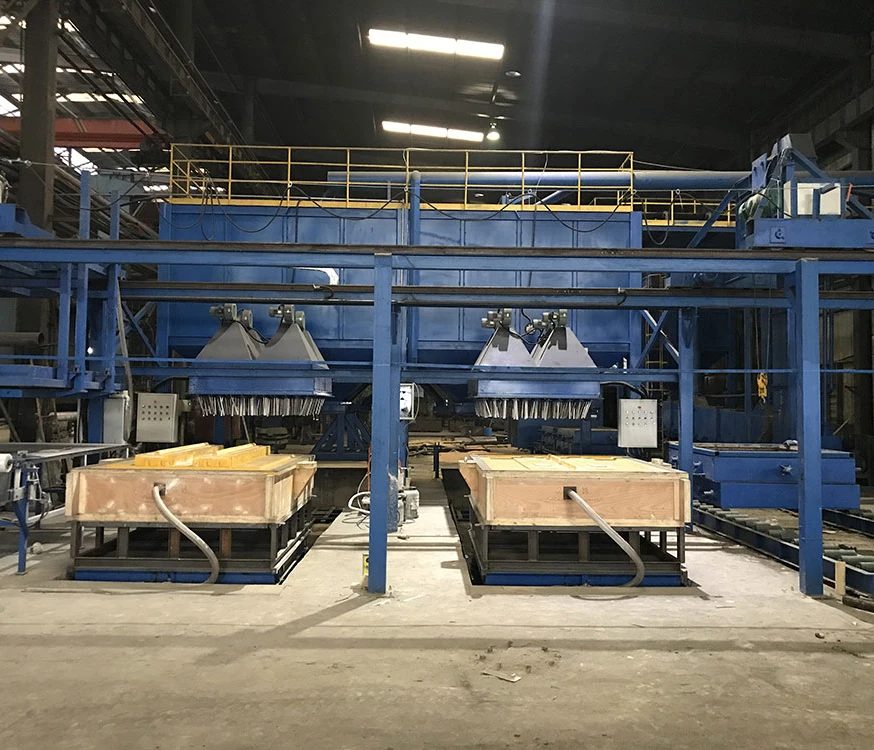
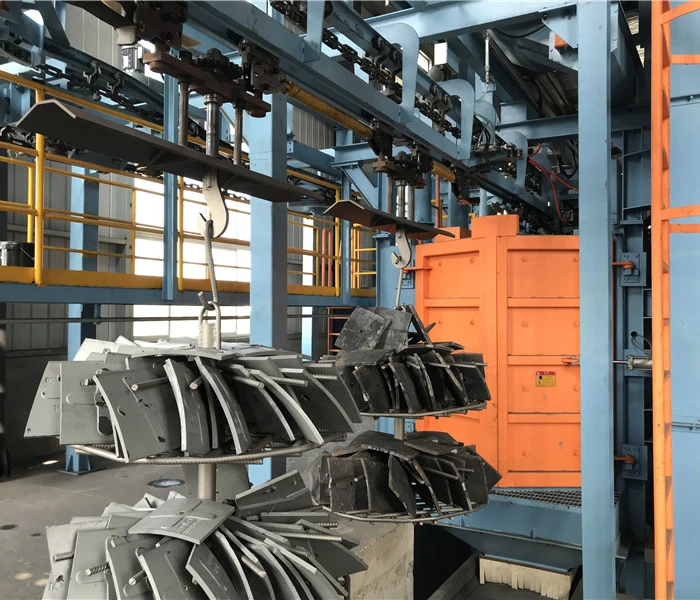
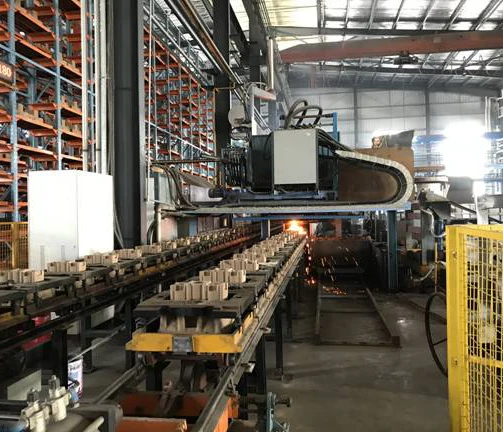
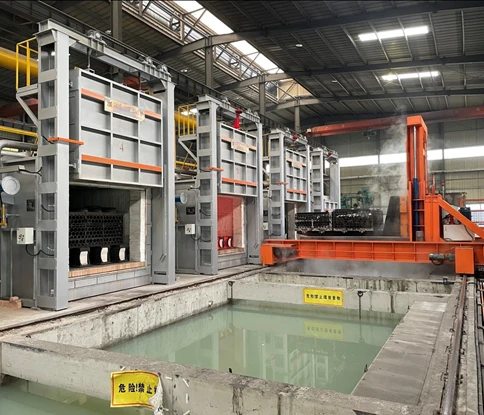
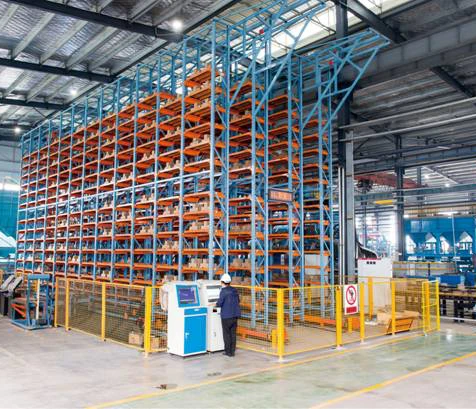
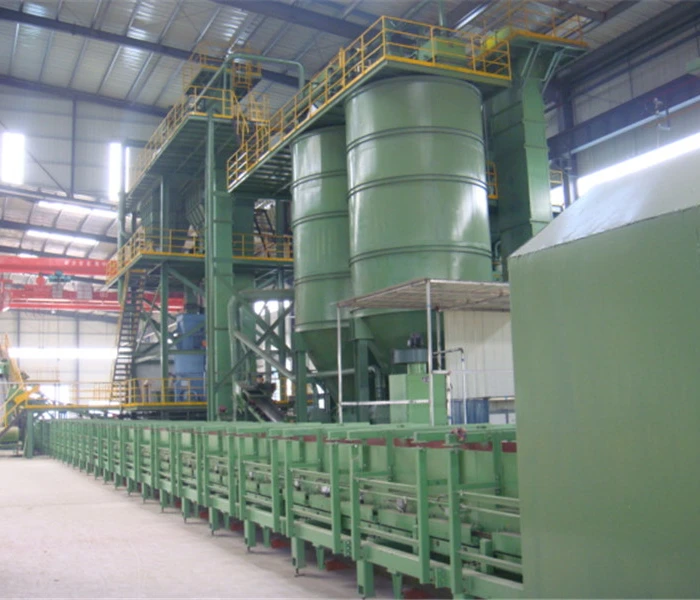
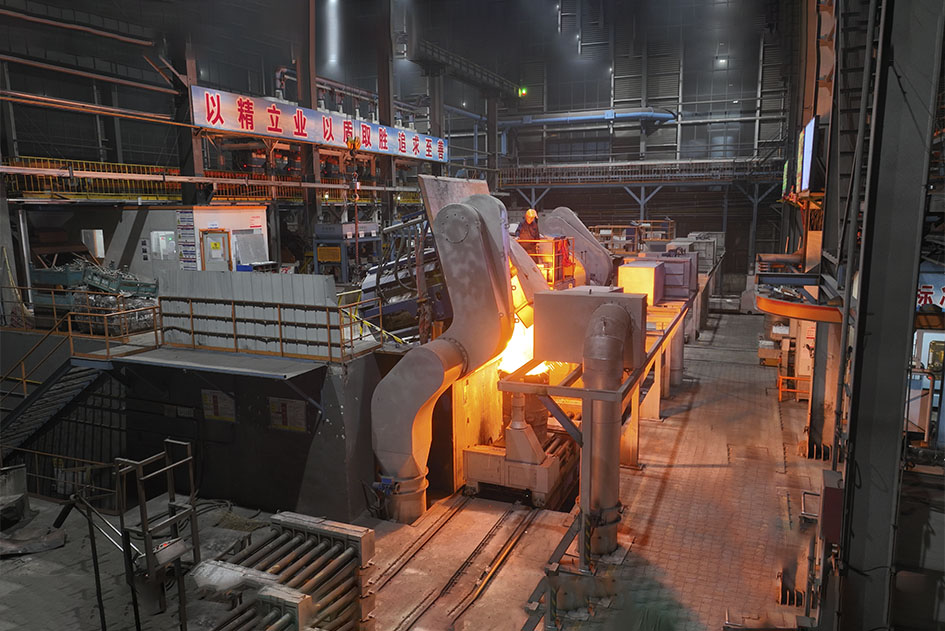
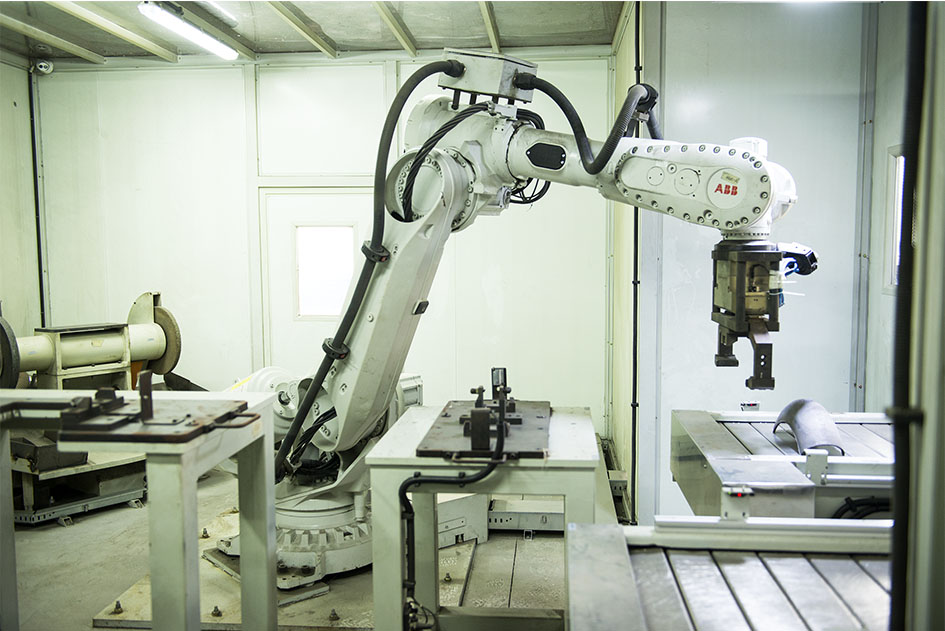
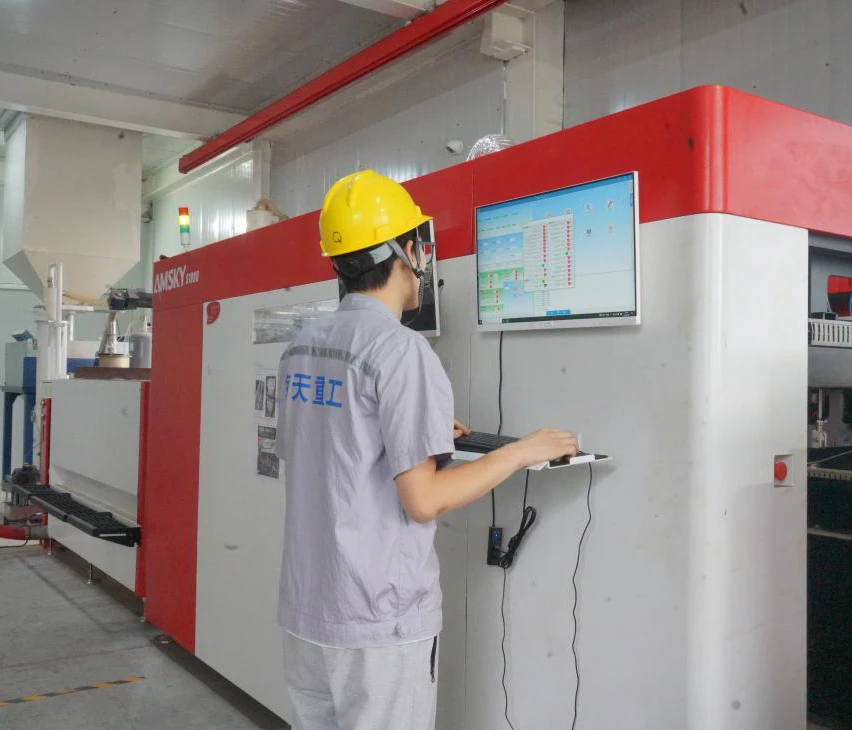
ИСПЫТАТЕЛЬНОЕ ОБОРУДОВАНИЕ
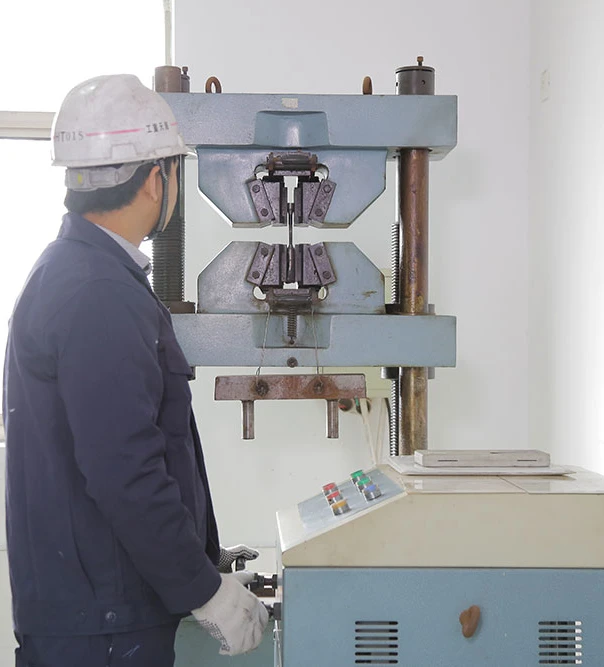
Оборудование для испытаний на растяжение
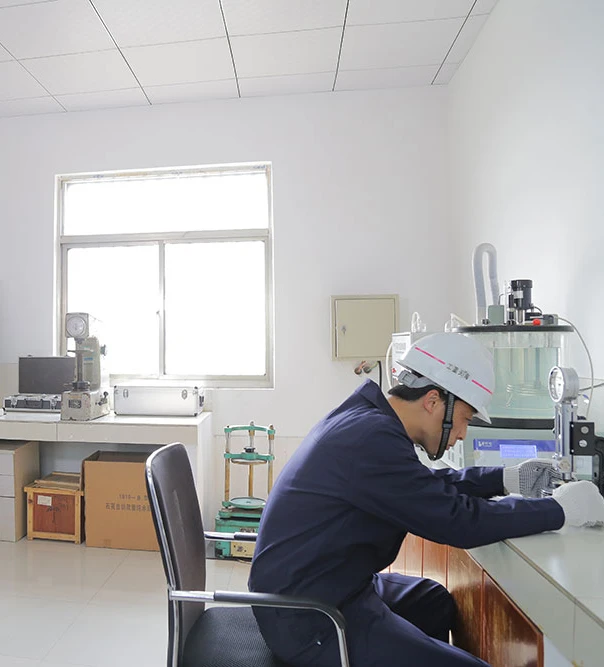
Оборудование для испытаний на энергию удара
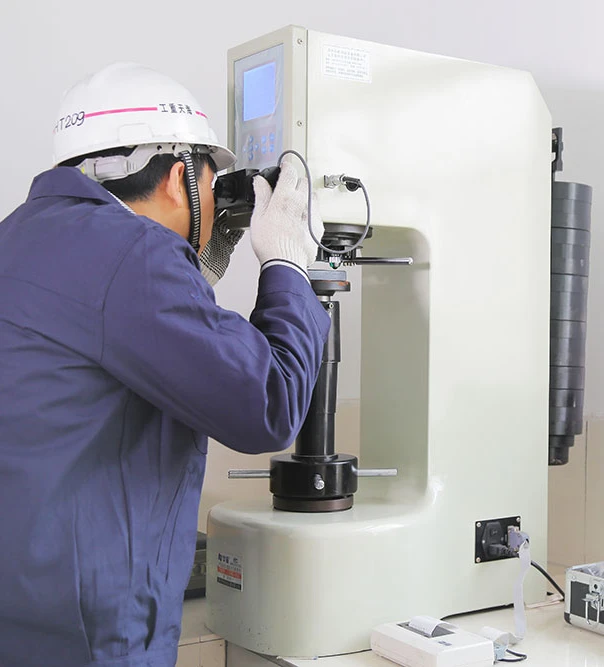
Оборудование для измерения твердости по Бринеллю
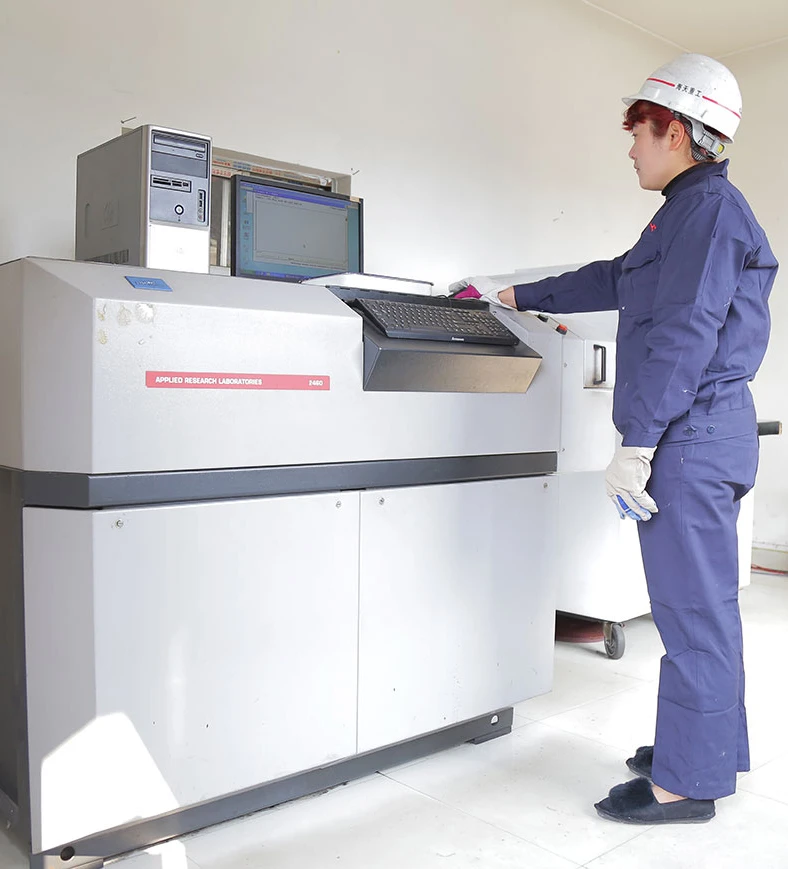
Оборудование для обнаружения компонентов спектрометра
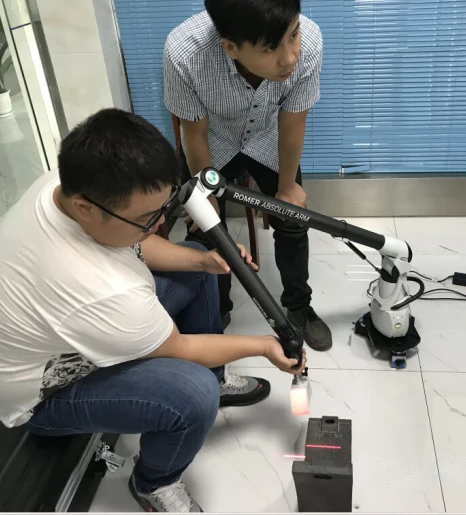
Триангуляционная координатно-измерительная машина
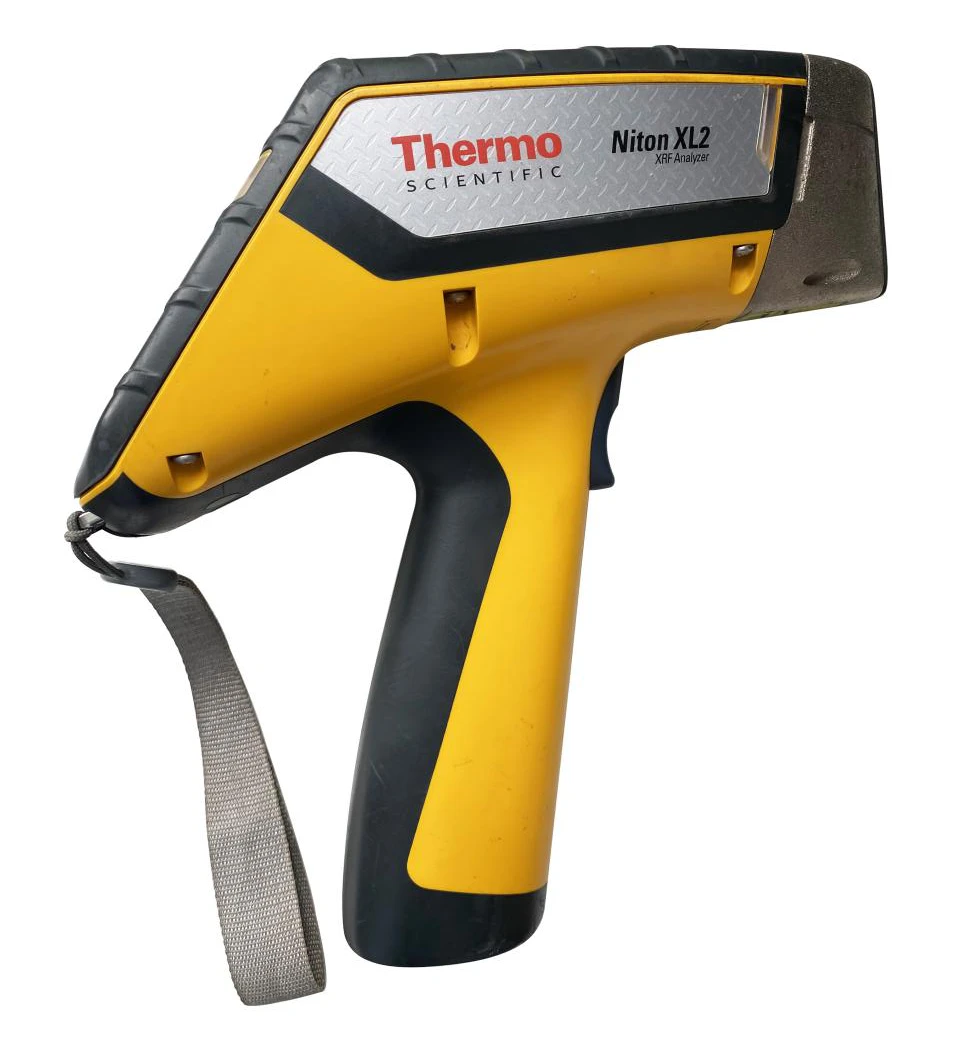
Ручной спектрометр
ПРОЦЕССНЫЙ ПОТОК
-
01
Выбор сырья
В процессе изготовления износостойких деталей решающее значение имеет выбор сырья. Мы тщательно отбираем высококачественные сплавы, чтобы обеспечить им превосходную износостойкость и прочность, закладывая прочную основу качества продукции.
-
02
Процесс плавления
После того как в печь поступает строго пропорциональное сырье, мы используем передовую технологию плавки, чтобы состав и температура расплавленного металла достигли оптимального состояния, обеспечивая равномерную и стабильную подачу металла для формования изделия.
-
03
Литье и формовка
В ходе изысканного процесса литья расплавленный металл впрыскивается в форму, где он затвердевает и приобретает определенную форму и размер. Наши мастера прошли профессиональное обучение и владеют различными сложными процессами формования, что позволяет гарантировать точность формы и размера изделий, а качество стабильное.
-
04
Дробеструйная очистка и шлифовка
После распалубки изделие подвергается тонкому шлифованию для удаления поверхностных дефектов и заусенцев, что делает его поверхность гладкой и ровной. Наши мастера используют деликатные методы и превосходные навыки для ухода за каждым изделием и придания ему идеального внешнего вида и текстуры.
-
05
Процесс термообработки
После процесса термообработки структура и характеристики продукта дополнительно стабилизируются и улучшаются. В соответствии с конкретными требованиями к продукту мы используем различные процессы термообработки, чтобы обеспечить превосходную износостойкость, прочность и коррозионную стойкость, а также адаптировать его к потребностям различных суровых рабочих условий.
-
06
Покраска и осмотр
Изделие окрашивается, что не только украшает внешний вид, но и повышает коррозионную стойкость и износостойкость его поверхности. После этого он проходит строгий процесс проверки, чтобы убедиться, что все показатели продукта соответствуют стандартным требованиям, и предоставить клиентам надежные гарантии на продукцию.
-
07
Заезд на склад и доставка
Наконец, продукт проходит строгий контроль качества и надежно хранится на складе, готовый к доставке в любое время. Как только мы получим заказ клиента, мы выполним доставку вовремя, с соблюдением количества и качества, чтобы обеспечить безопасную и своевременную доставку продукта клиенту.
КОНТРОЛЬ КАЧЕСТВА ВО ВРЕМЯ ПРОИЗВОДСТВА
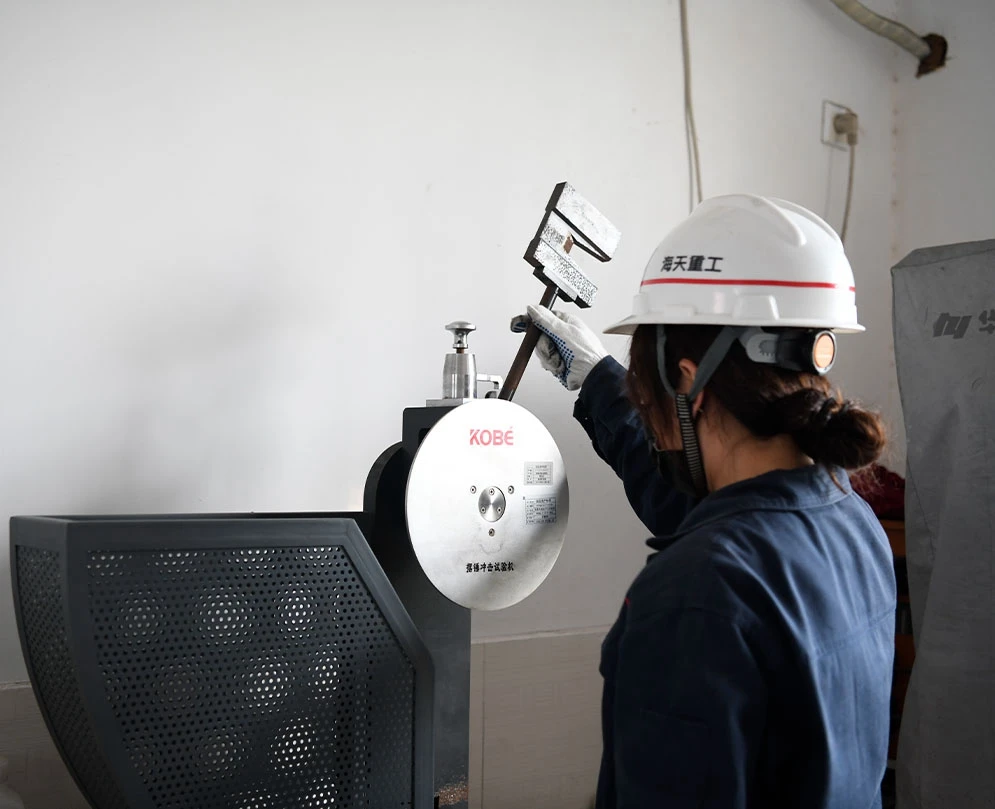
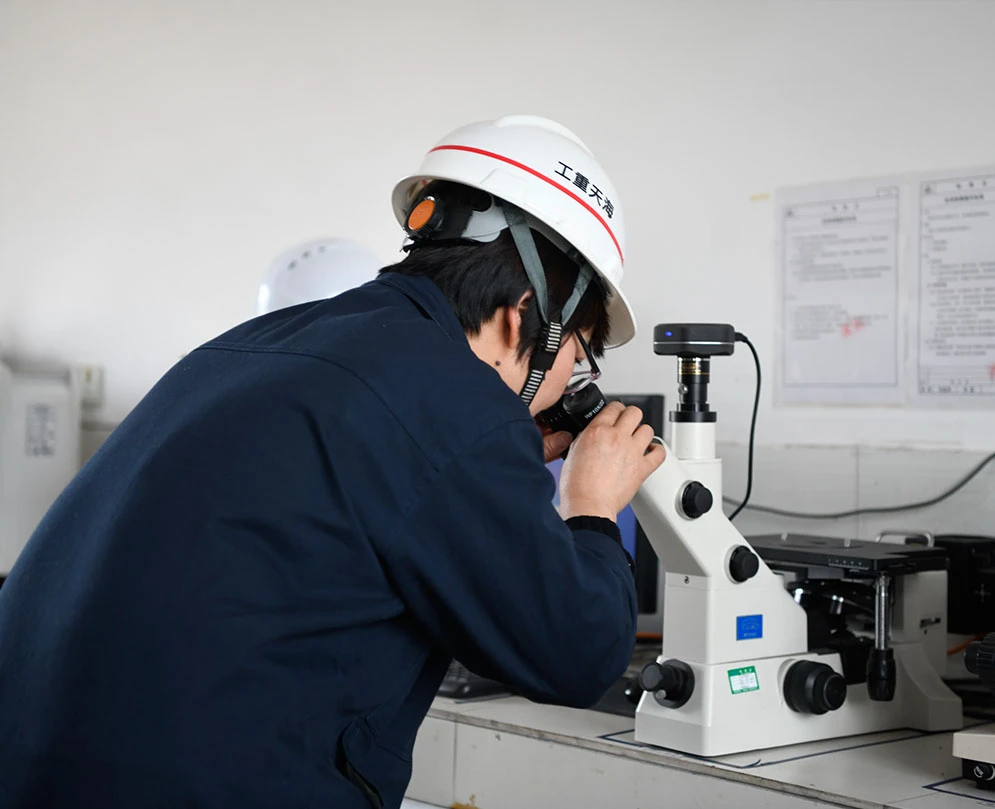
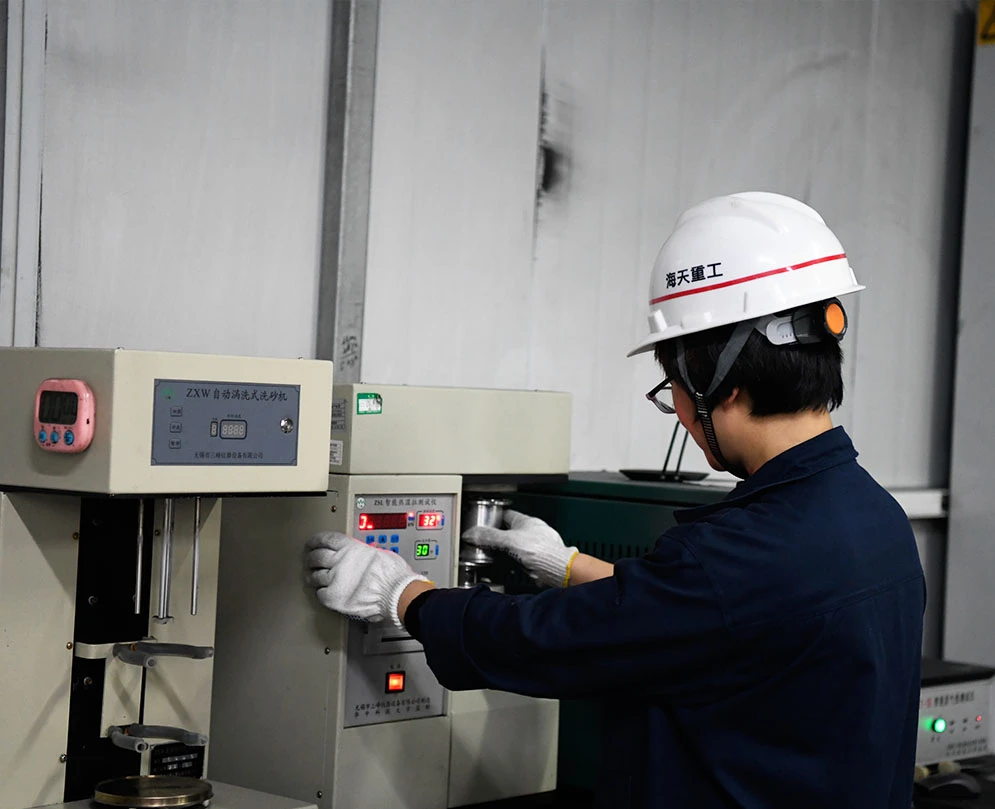
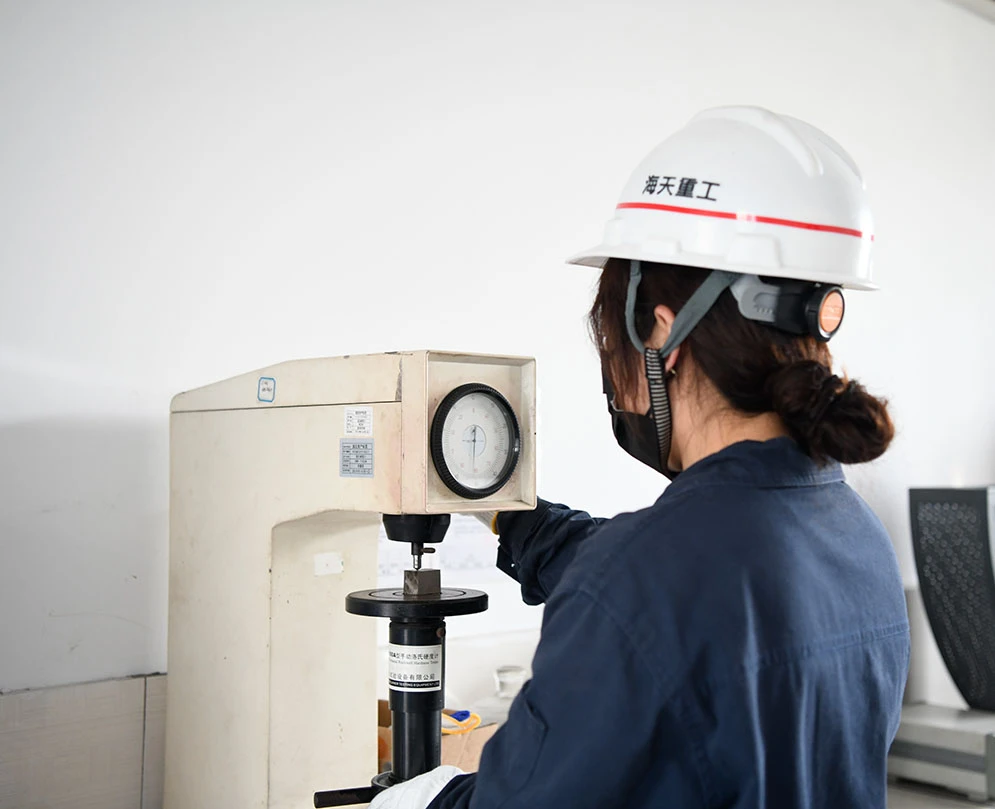
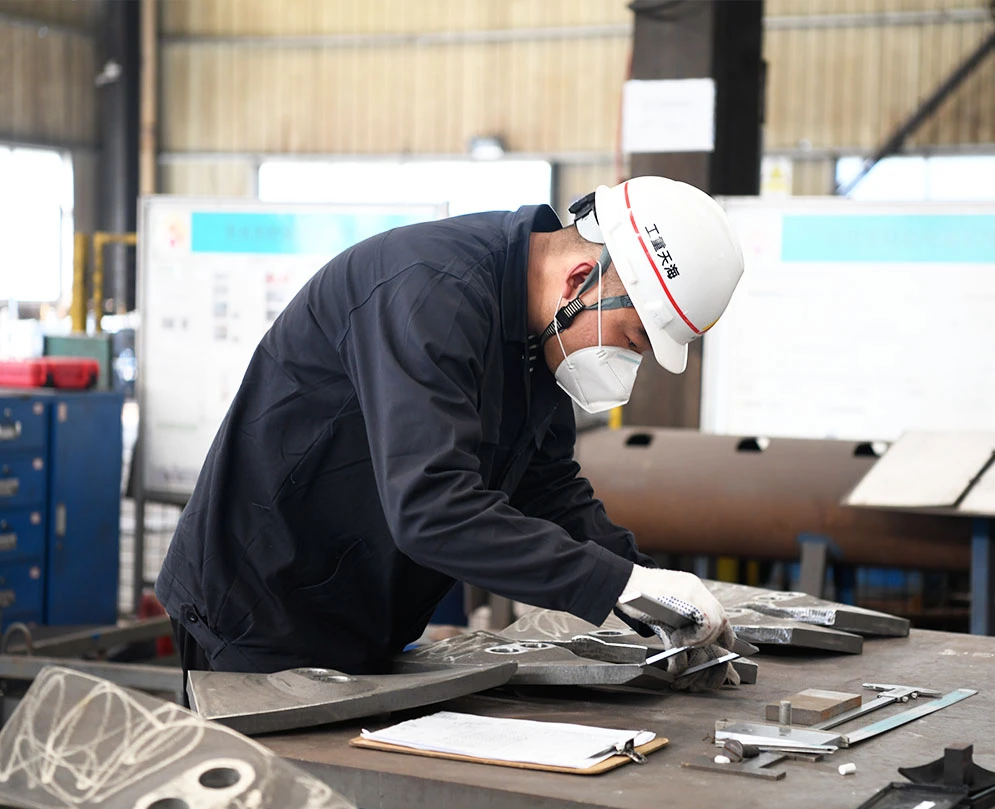
-
Управление параметрами процесса
Контроль температуры: следите за температурой во время плавки, разливки и термообработки, чтобы обеспечить обработку металла в соответствующем температурном диапазоне и обеспечить качество продукции.
Контроль времени: Контролируйте время каждого процесса, чтобы гарантировать, что каждый процесс выполняется полностью и без чрезмерных усилий, чтобы избежать дефектов.
Контроль давления: во время процесса заливки и формования размер и распределение давления контролируются путем вакуумирования через прозрачную мембрану, чтобы обеспечить однородность и стабильность металлической жидкости, заполняющей форму.
-
Применение испытательного оборудования
Обнаружение металлургического микроскопа: наблюдайте и анализируйте структуру металла, чтобы обнаружить наличие внутри металла дефектов, таких как поры и включения.
Ультразвуковое обнаружение: используйте ультразвуковую технологию для обнаружения дефектов внутри продукта, таких как трещины, включения и т. д., чтобы обеспечить качество и надежность продукта.
Испытание на твердость: проверьте твердость изделия, чтобы оценить, соответствуют ли его износостойкость и механические свойства требованиям.
-
Автоматизированное производственное оборудование
Автоматизированная система управления: используйте передовые автоматизированные системы управления для мониторинга производственного процесса, достижения точного контроля и регулировки производственных параметров, а также улучшения консистенции и стабильности продукции.
-
Ручной контроль качества
Проверка технического специалиста: Технические специалисты-технологи регулярно проверяют производственную линию, чтобы убедиться, что оборудование работает нормально и производственные параметры соответствуют требованиям.
Надзор за работой оператора процесса: Контролируйте работу оператора процесса, чтобы гарантировать, что операция стандартизирована и точна, а также уменьшить влияние операционных ошибок на качество продукции.
-
Анализ и улучшение данных
Сбор и анализ данных о качестве: собирайте различные данные о качестве в производственном процессе, проводите статистический анализ, вовремя находите проблемы и принимайте меры по улучшению.
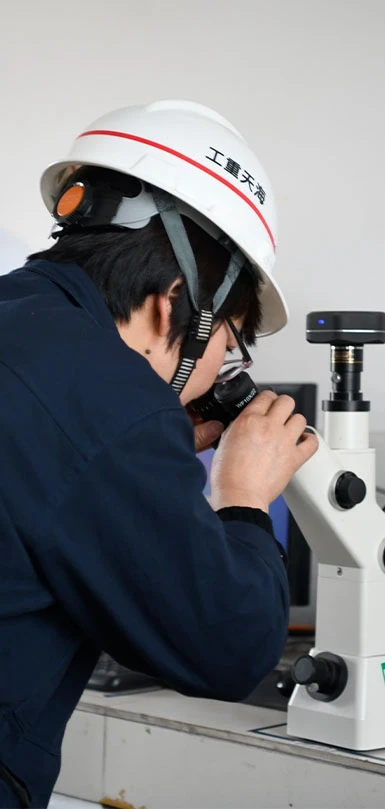
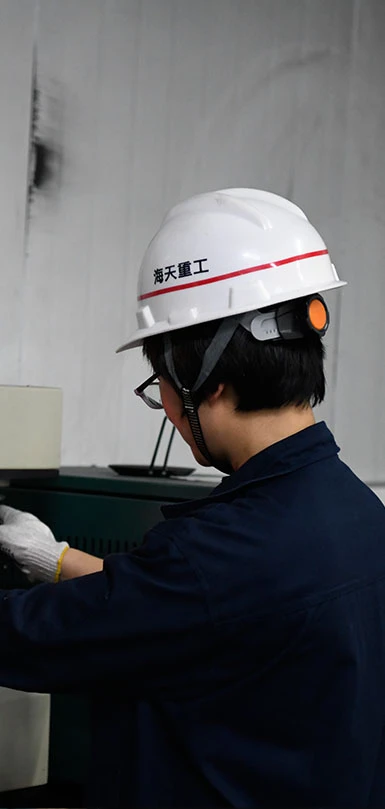
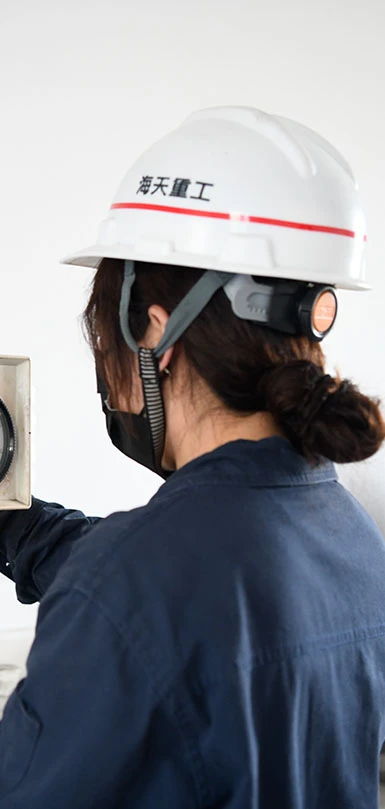
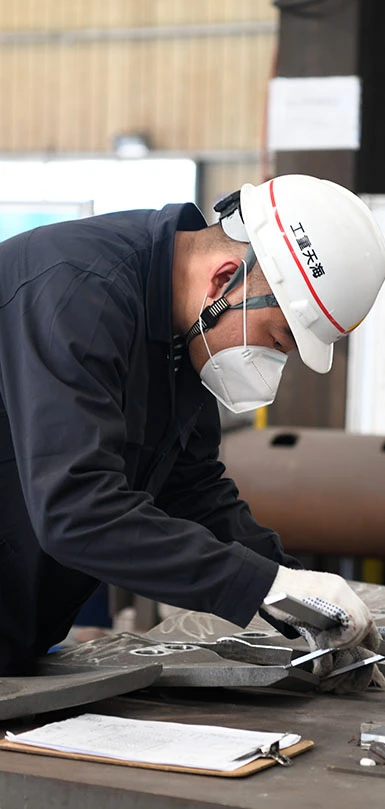
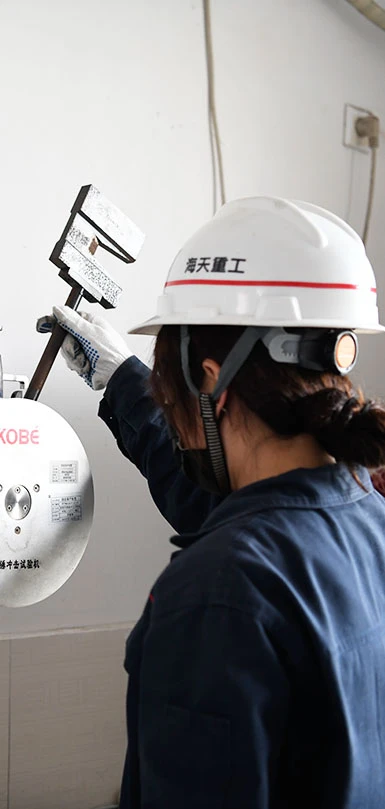
Если вы заинтересованы в нашей продукции или у вас есть какие-либо вопросы, пожалуйста, свяжитесь с нами.
Мы предоставим профессиональные консультационные услуги и индивидуальные решения в соответствии с вашими потребностями.
ОТПРАВИТЬ ЗАПРОС СЕЙЧАСКонтактная информация
Тел: 0555-71661667166199
Факс: 0555-6971198
Веб-сайт: https://www.htwearparts.com
Электронная почта: info@mashthi.com
Почтовый индекс: 243141.
Адрес: Промышленный парк Синьши, район Бованг, город Мааньшань, провинция Аньхой, Китай.