Capacidad de producción
La empresa lleva 20 años profundamente implicada en la industria de la fundición. El centro de investigación y desarrollo es un centro tecnológico de dos pisos con un área de construcción de más de 1.200 metros cuadrados. Es un centro provincial de tecnología empresarial y diseño industrial. El centro tecnológico está equipado con un espectrómetro de lectura directa ARL2460 importado, un instrumento de medición del sistema de magnetización de saturación, una máquina de prueba de materiales universal WFW-600, una máquina de prueba de impacto JB30B, un probador de características de enfriamiento, un microscopio metalográfico óptico, un detector de arena y otros instrumentos y equipos de prueba avanzados en el hogar. y en el extranjero, con capacidades de diseño innovadoras. Línea de producción vertical, línea de producción de espuma perdida, fundición de carcasa con núcleo frío, línea de producción de impresión 3D. La investigación y desarrollo de productos abarca desde 0,5 kg hasta 8000 kg, correspondientes a la línea de moldeo para productos por lotes y a la línea manual para productos pesados de una sola pieza. Hay máquinas de grabado que pueden grabar moldes de madera y equipos de impresión 3D que pueden imprimir núcleos de arena para verter, reduciendo el tiempo de apertura del molde. La empresa ha pasado la certificación del sistema de calidad 1SO9001 y el proceso de producción está equipado con personal profesional de inspección, inspección final e inspección de envío. La tasa de cobertura de la inspección final del producto alcanza el 100%, lo que garantiza efectivamente la calidad y estabilidad de los productos de la empresa.
-
20
20 años de experiencia en la industria de la fundición.
-
1200METRO2
Superficie edificable de más de 1.200 metros cuadrados
-
100%
La tasa de cobertura de la inspección final del producto alcanza el 100%
-
Línea de moldeado vertical DISA
Capacidad de producción: normalmente en el rango de 100 a 150 piezas fundidas por hora, dependiendo del tamaño y la complejidad de la pieza fundida.
Tamaño del molde: Moldes adecuados para piezas de fundición pequeñas y medianas, con un tamaño máximo de molde de aproximadamente 335 x 335 mm.
Método de Moldeo: Moldeo vertical, utilizando la tecnología de moldeo por alta presión de DISA. -
Línea de moldeo de espuma perdida
Capacidad de producción: Generalmente en el rango de 50 a 100 piezas por hora, dependiendo del tamaño y complejidad de la pieza.
Tamaño del molde: Adecuado para espuma perdida más grande, generalmente el tamaño máximo del molde puede alcanzar 500 x 500 mm o más.
Método de fundición: Fundición de espuma perdida, que utiliza espuma perdida que se funde con gas a alta temperatura, capaz de producir formas complejas y piezas fundidas de alta precisión. -
Línea de producción del método V.
Capacidad de producción: el peso de las piezas fundidas producidas por hora es de aproximadamente 10 a 20 toneladas (dependiendo del tamaño de la pieza y los parámetros del proceso).
Tamaño de fundición: El tamaño máximo puede alcanzar 3000 mm x 2000 mm x 1500 mm (se puede personalizar según las necesidades)
Número de moldes: Diseño de múltiples moldes, se pueden configurar según las necesidades de producción. -
Línea de producción de granallado con cadena de acumulación
Capacidad de granallado: Cada máquina granalladora tiene una capacidad de granallado de 180-200 kg por minuto.
Potencia de la granalladora: cada granalladora tiene una potencia de 11 a 15 kW y la potencia total es de 88 a 120 kW.
Velocidad de granallado: 70-80 m/s. -
Línea de producción de moldeo de carcasa de núcleo frío
Capacidad de producción: La capacidad de producción es generalmente entre 30 y 60 piezas fundidas por hora, dependiendo del tamaño y complejidad de la pieza fundida.
Tamaño del molde: Adecuado para moldes medianos a grandes, generalmente el tamaño máximo del molde puede alcanzar 400 x 400 mm o más.
Método de fundición: Fundición de carcasa con núcleo frío, mediante proceso de carcasa con núcleo frío, capaz de producir piezas fundidas complejas y de alta precisión.
Nivel de automatización: Tiene un alto nivel de automatización, incluyendo funciones automáticas de carga, conformado, vertido, enfriamiento y desmoldeo de moldes. -
Línea de producción de tratamiento térmico con horno de túnel de gas
Estructura del horno: ladrillos refractarios de alta resistencia, la carcasa es de placa de acero de alta resistencia
Tamaño del horno: personalizado según las necesidades específicas, generalmente de 1,5 metros a 3 metros de alto, de 1 metro a 2,5 metros de ancho
Volumen del horno: unos 3 metros cúbicos. -
Sistema de almacenamiento estereoscópico de control inteligente de almacén no tripulado
WMS (Sistema de gestión de almacenes): proporciona funciones como gestión de inventario, procesamiento de pedidos, instrucciones de selección, almacenamiento y operaciones de salida.
WCS (Sistema de Control de Almacén): Monitoreo en tiempo real del estado operativo de los equipos automatizados y optimización de la programación de los equipos.
Interfaz de operación: pantalla táctil o interfaz de control por computadora, admite monitoreo y administración remotos. -
Línea de producción vertical.
Capacidad de producción: 90-120 juegos por hora (dependiendo de las condiciones de producción específicas)
Tamaño de la moldura: El tamaño estándar es 450 mm x 600 mm x 150-350 mm (ancho x largo x alto), se puede personalizar según las necesidades.
Velocidad de moldeo: 20-25 segundos/molde -
Horno de media frecuencia
Capacidad de fusión: Dependiendo del tamaño del horno, normalmente entre 5 y 15 toneladas.
Tiempo de fusión: aproximadamente 1-2 horas (dependiendo del material y la capacidad)
Temperatura máxima de fusión: 1600°C a 1800°C (dependiendo del material específico) -
Estación de trabajo de pulido con robot
Tipo de herramienta de rectificado: Amoladora eléctrica o neumática (opcional)
Velocidad de rectificado: ajustable, normalmente entre 1000 y 5000 RPM
Número de cabezales de rectificado: único o múltiple (según la configuración) -
equipo de impresión 3D
Tamaño de la máquina principal: 9000 × 1900 × 1950 mm (largo × ancho × alto). El tiempo de impresión de la caja completa es de unas 12 horas. La configuración estándar son dos cajas de arena en funcionamiento, que pueden lograr una impresión ininterrumpida las 24 horas.
El tamaño interior de la caja de arena de trabajo es 1800 × 1000 × 730 mm (largo × ancho × alto), lo que satisface las necesidades de impresión de la mayoría de los moldes de arena para fundición.
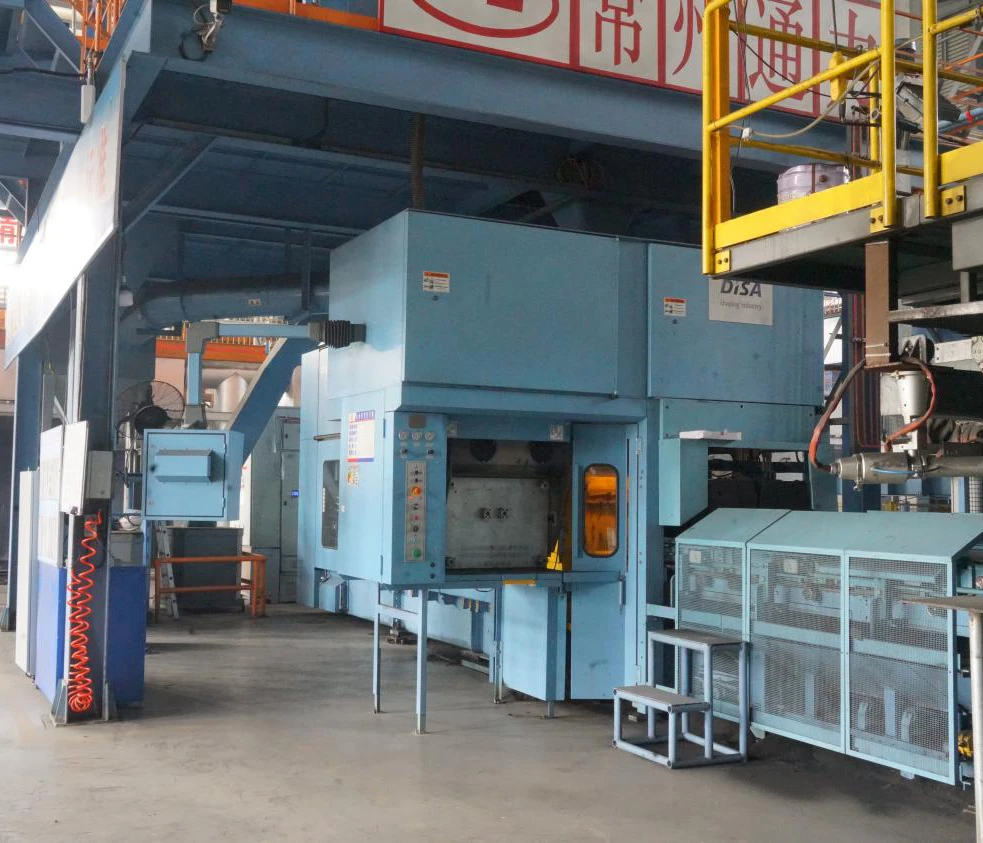
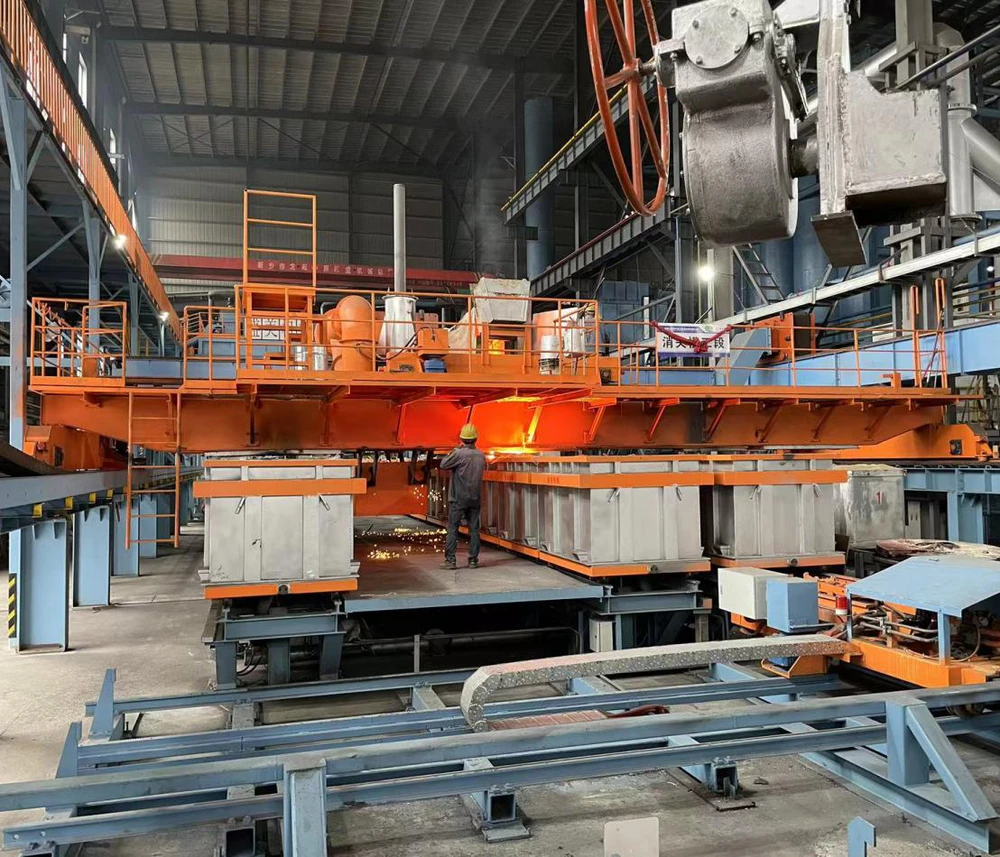
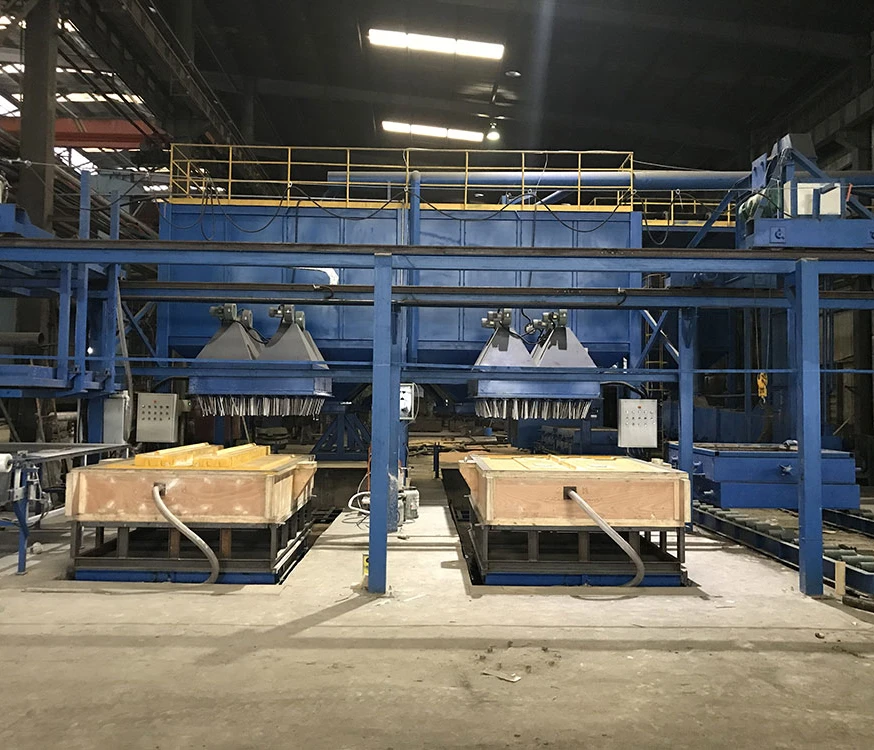
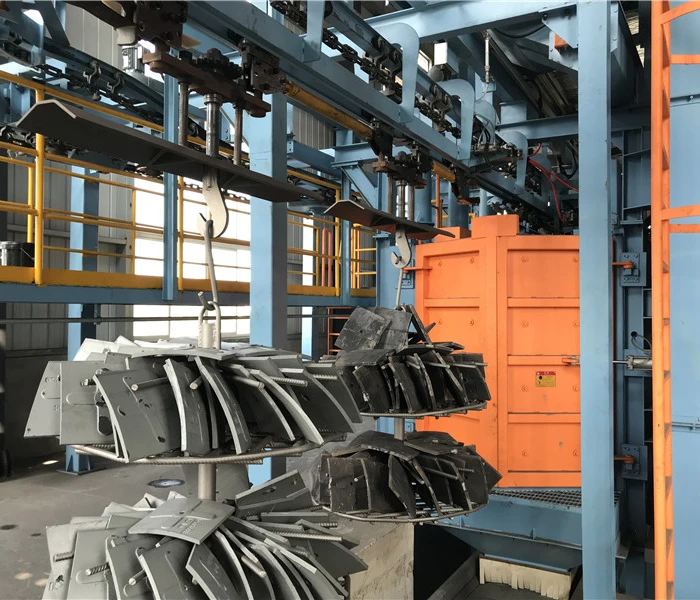
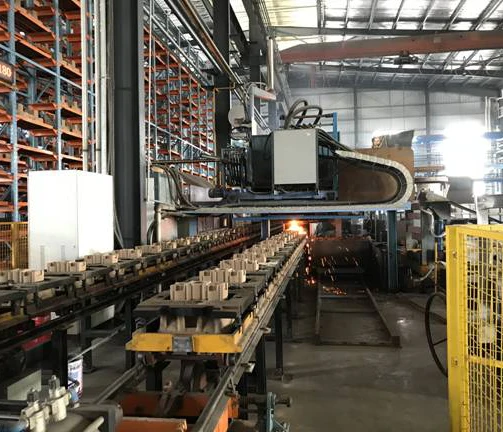
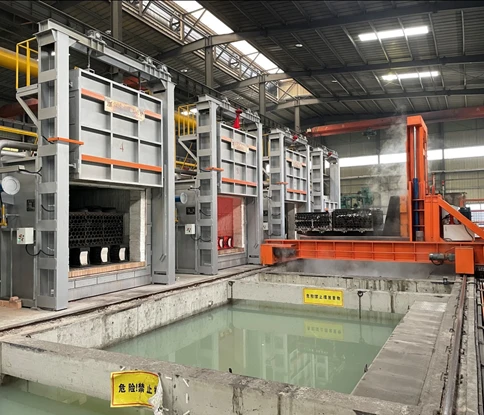
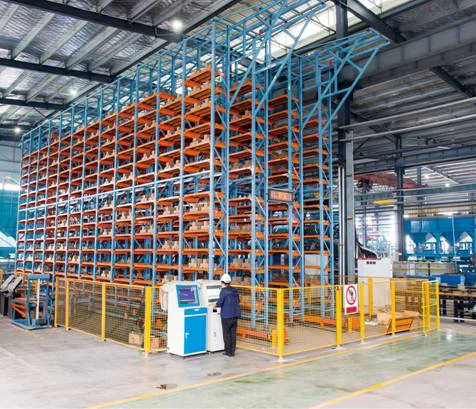
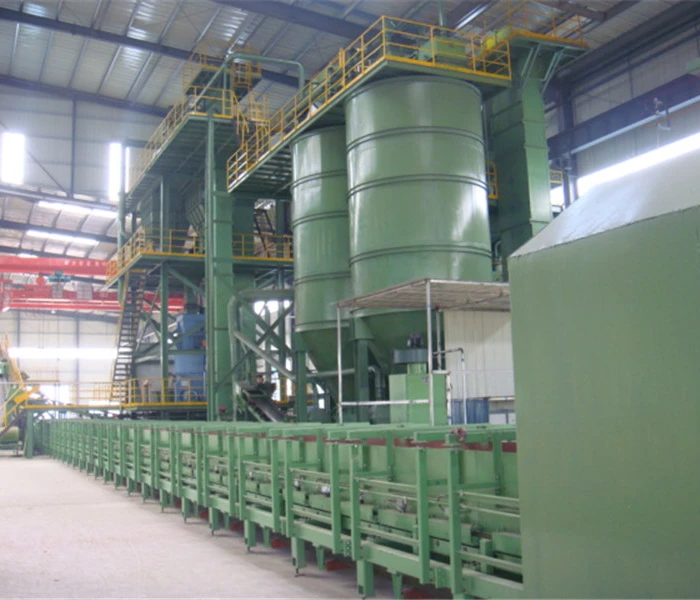
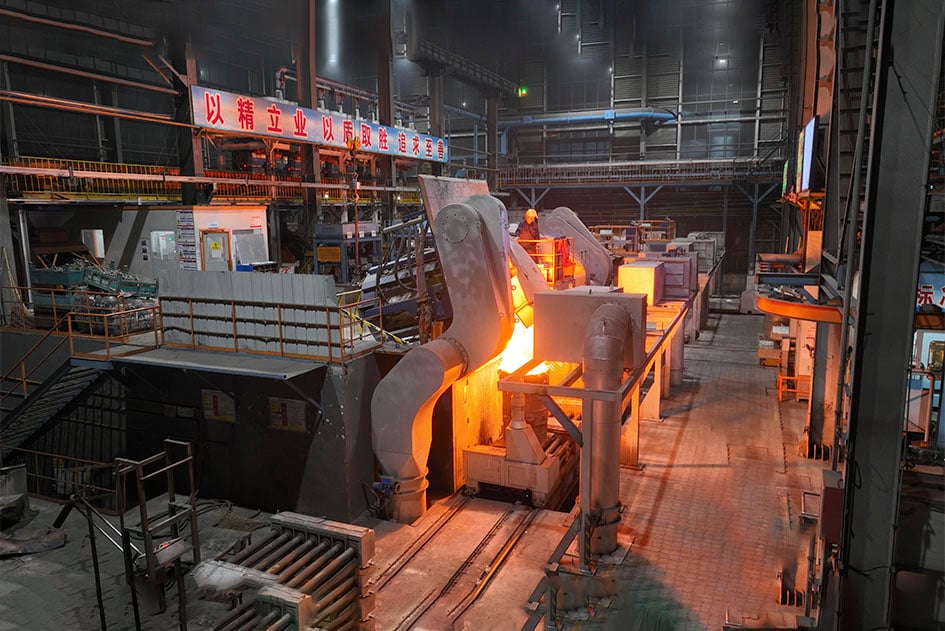
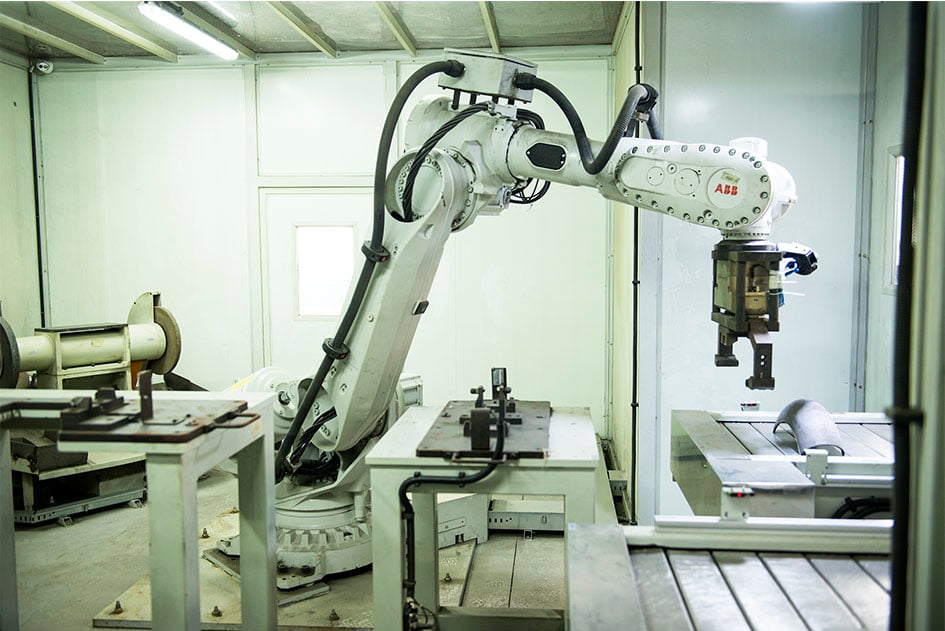
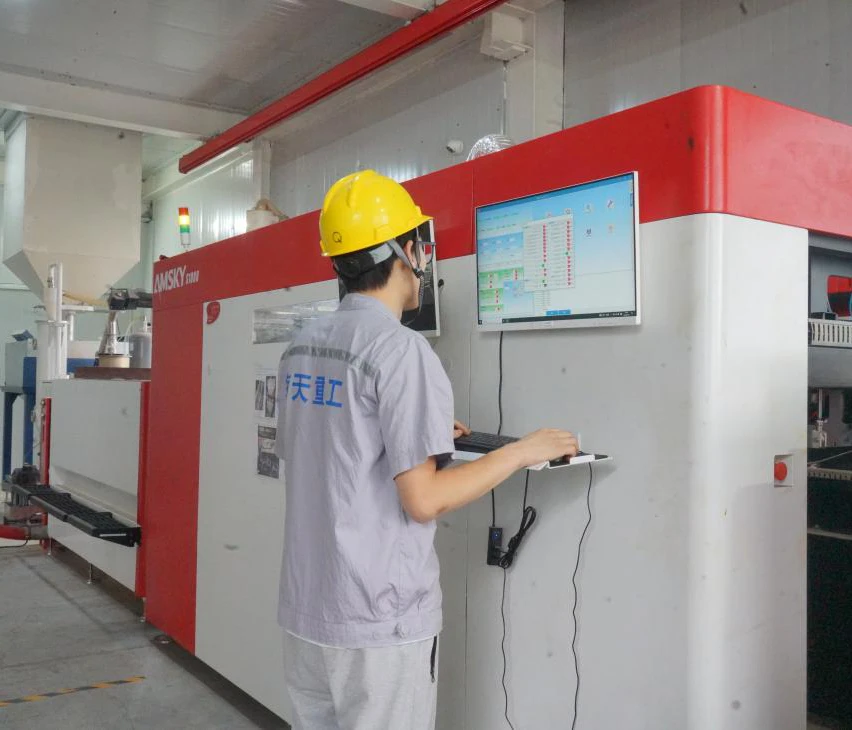
EQUIPO DE PRUEBA
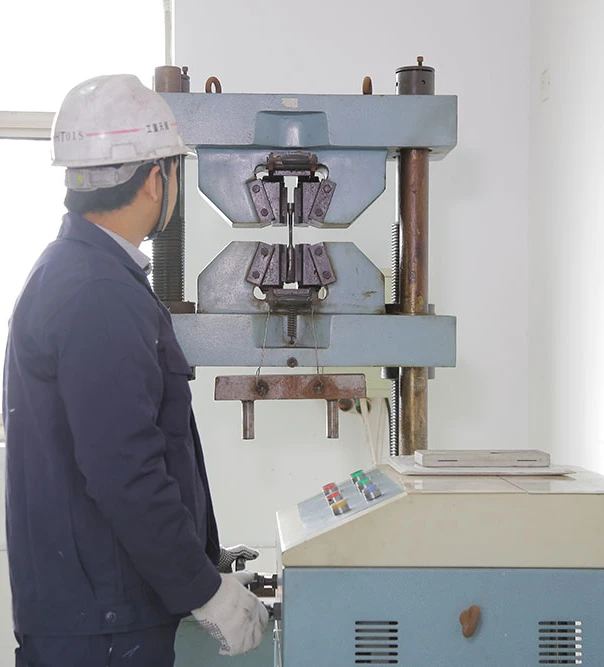
Equipos de prueba de tracción.

Equipos de prueba de energía de impacto.
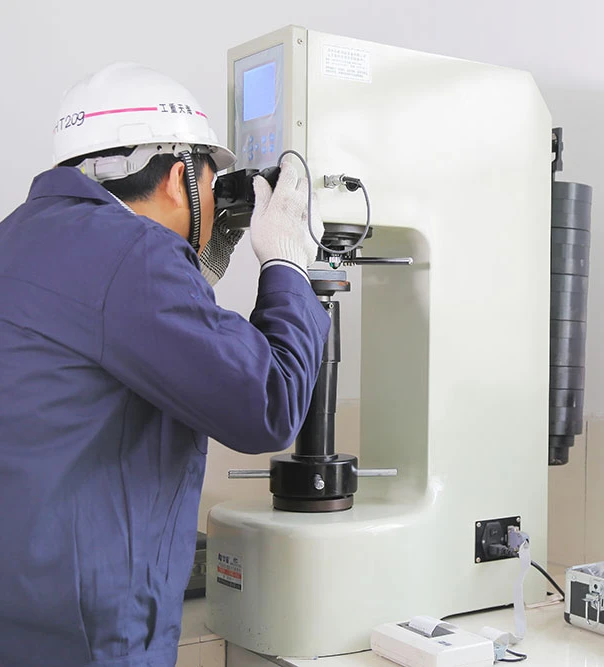
Equipo de prueba de dureza Brinell
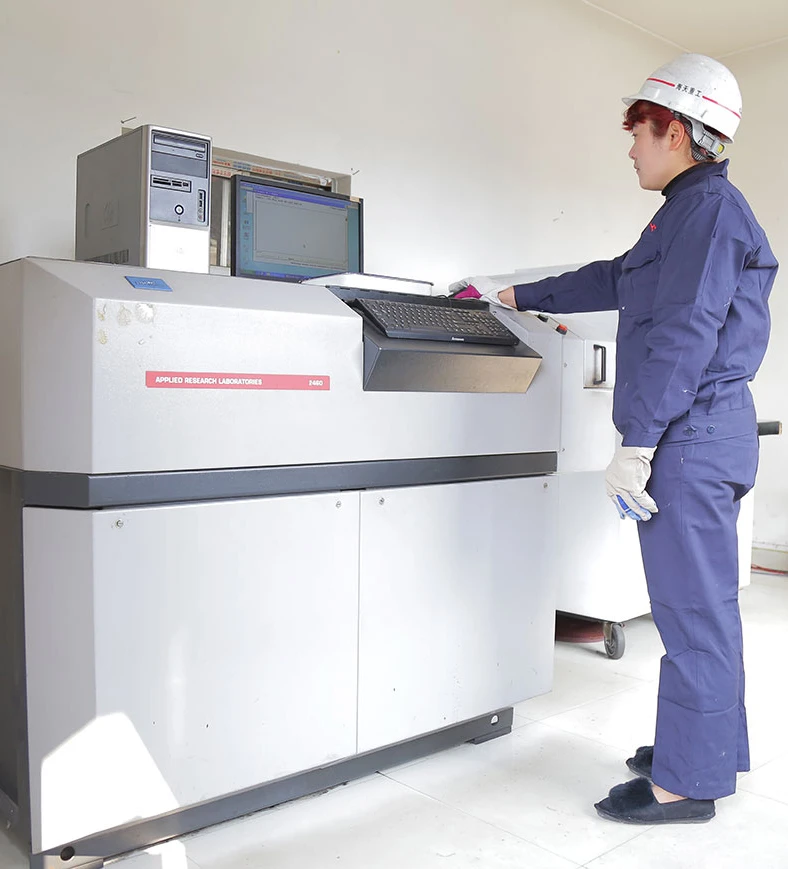
Equipo de detección de componentes de espectrómetro.
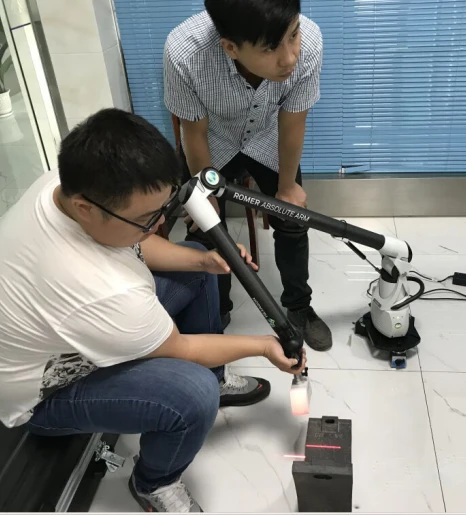
Máquina de medición de coordenadas por triangulación
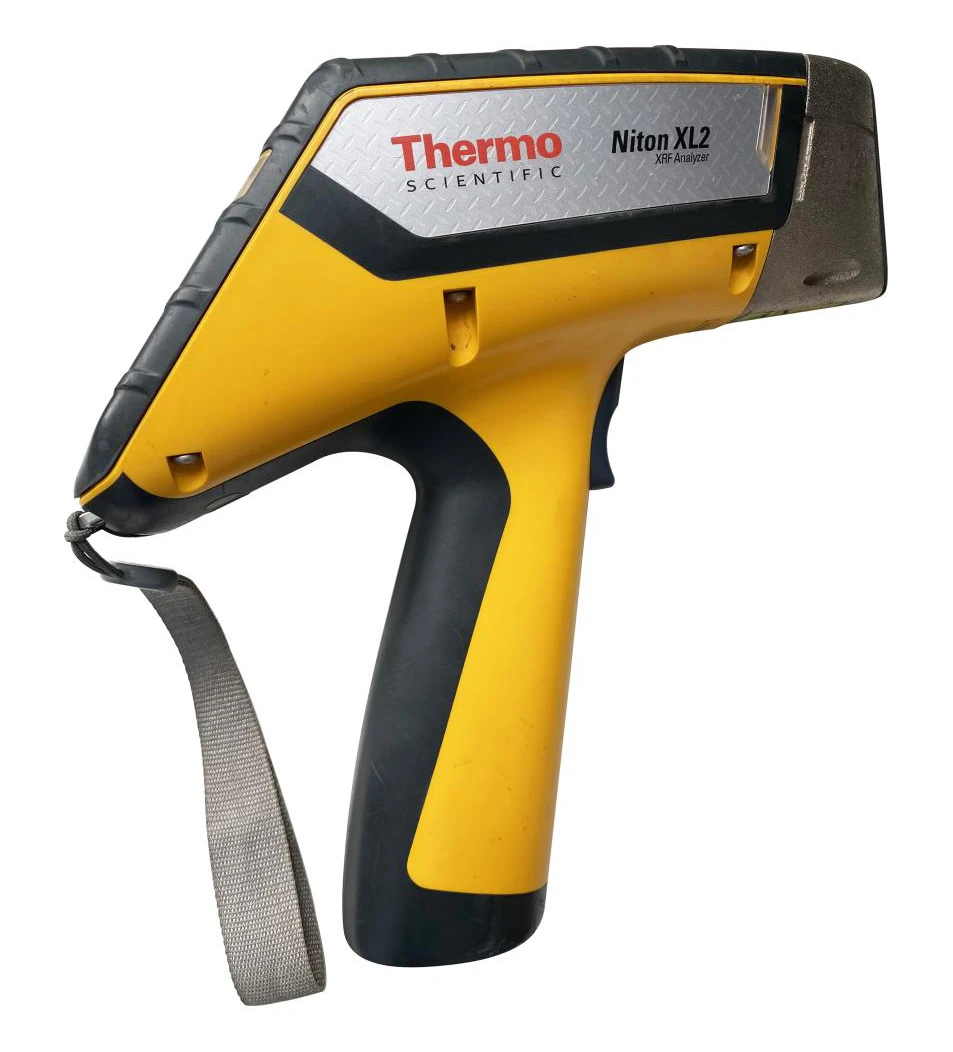
Espectrómetro de mano
FLUJO DEL PROCESO
-
01
Selección de materia prima
En el proceso de fabricación de piezas resistentes al desgaste, la selección de las materias primas es crucial. Seleccionamos cuidadosamente materiales de aleación de alta calidad para garantizar que tengan una excelente resistencia al desgaste y resistencia, sentando una base sólida para la calidad de los productos.
-
02
proceso de fusión
Después de que las materias primas estrictamente proporcionadas ingresan al horno, utilizamos tecnología de fundición avanzada para garantizar que la composición y la temperatura del metal fundido alcancen el estado óptimo, proporcionando un flujo de metal uniforme y estable para el moldeado del producto.
-
03
Fundición y moldeado
A través del exquisito proceso de fundición, el metal fundido se inyecta en el molde para solidificarse y moldearse en una forma y tamaño específicos. Nuestros artesanos han recibido capacitación profesional y dominan varios procesos de moldeo complejos para garantizar que la forma y el tamaño de los productos sean precisos y la calidad estable.
-
04
Granallado y rectificado
Después del desmolde, el producto se somete a un proceso de pulido fino para eliminar defectos y rebabas de la superficie, dejando su superficie lisa y plana. Nuestros artesanos utilizan técnicas delicadas y magníficas habilidades para cuidar cada producto y darle una apariencia y textura perfecta.
-
05
Proceso de tratamiento térmico
Después del proceso de tratamiento térmico, la estructura y el rendimiento del producto se estabilizan y mejoran aún más. De acuerdo con los requisitos específicos del producto, utilizamos diferentes procesos de tratamiento térmico para que tenga una excelente resistencia al desgaste, solidez y resistencia a la corrosión, y se adapte a las necesidades de diversos entornos de trabajo hostiles.
-
06
Pintura e inspección
El producto está pintado, lo que no sólo embellece la apariencia, sino que también mejora la resistencia a la corrosión y al desgaste de su superficie. Después de eso, pasa por un estricto proceso de inspección para garantizar que todos los indicadores del producto cumplan con los requisitos estándar y brinden a los clientes garantías confiables del producto.
-
07
Entrada y entrega del almacén.
Finalmente, el producto pasa por una estricta inspección de calidad y se almacena de forma segura en el almacén, listo para ser entregado en cualquier momento. Una vez que recibamos el pedido del cliente, completaremos la entrega a tiempo, cantidad y calidad para garantizar que el producto se entregue al cliente de forma segura y puntual.
CONTROL DE CALIDAD DURANTE LA PRODUCCIÓN
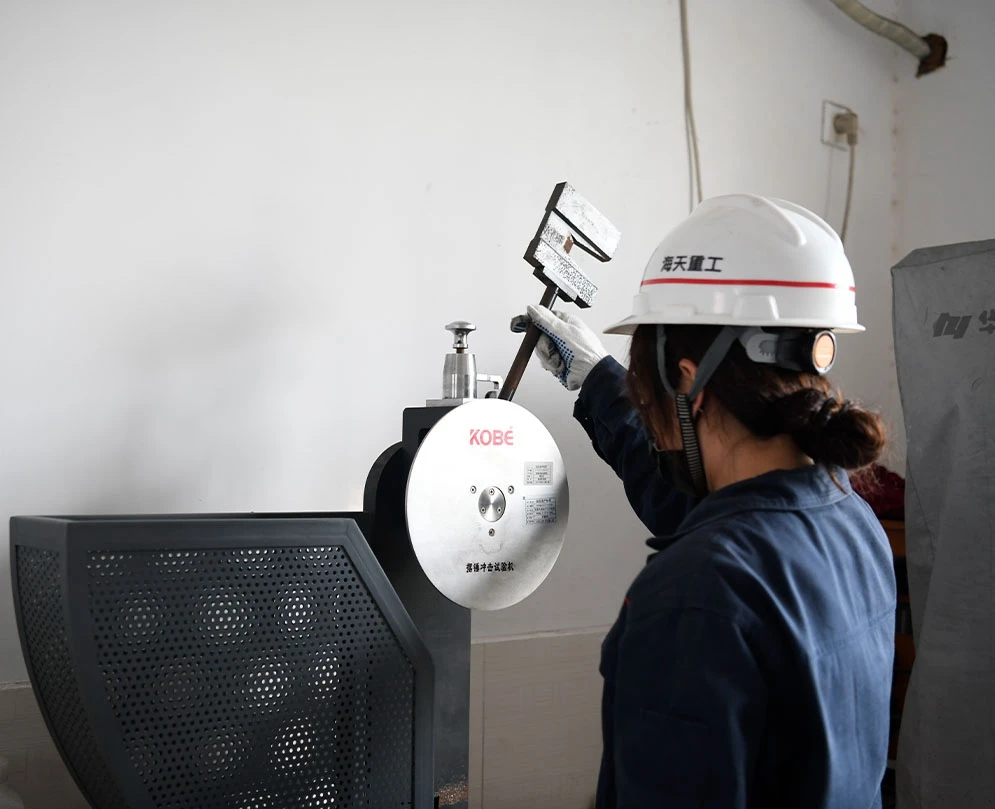
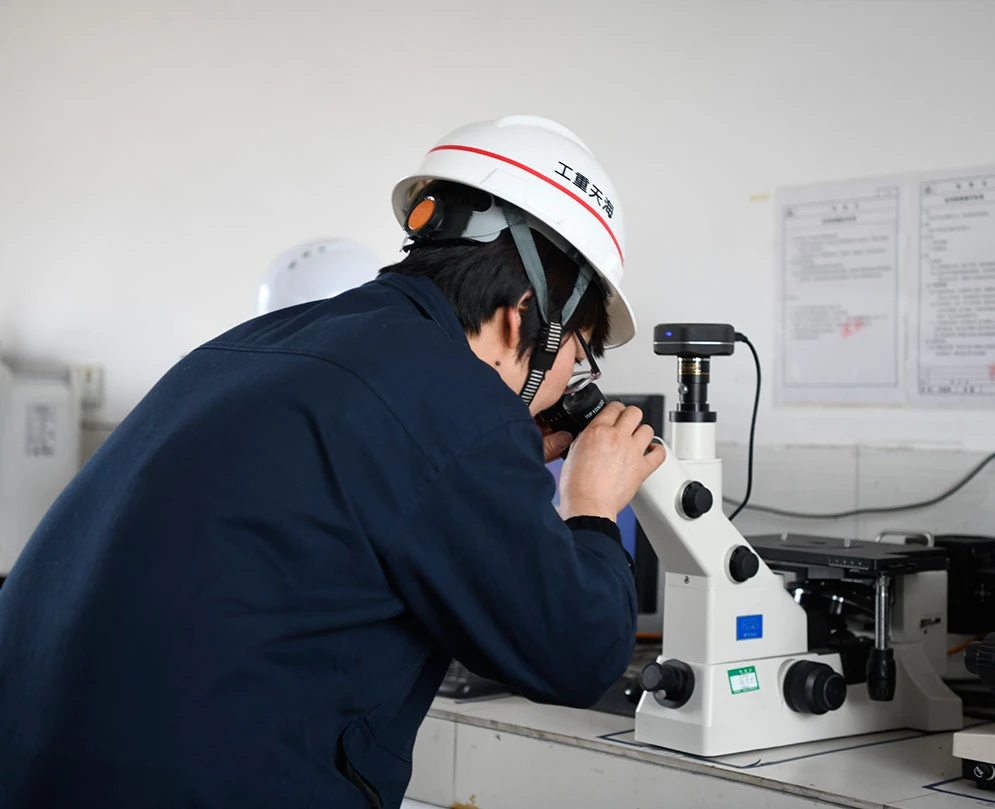
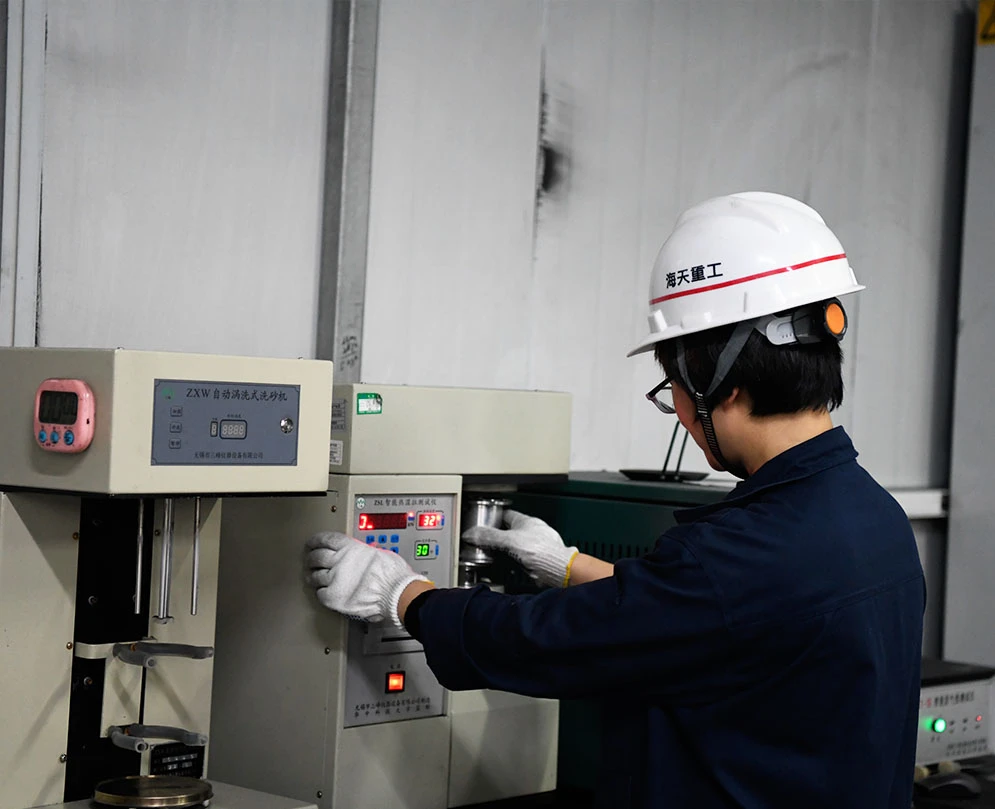
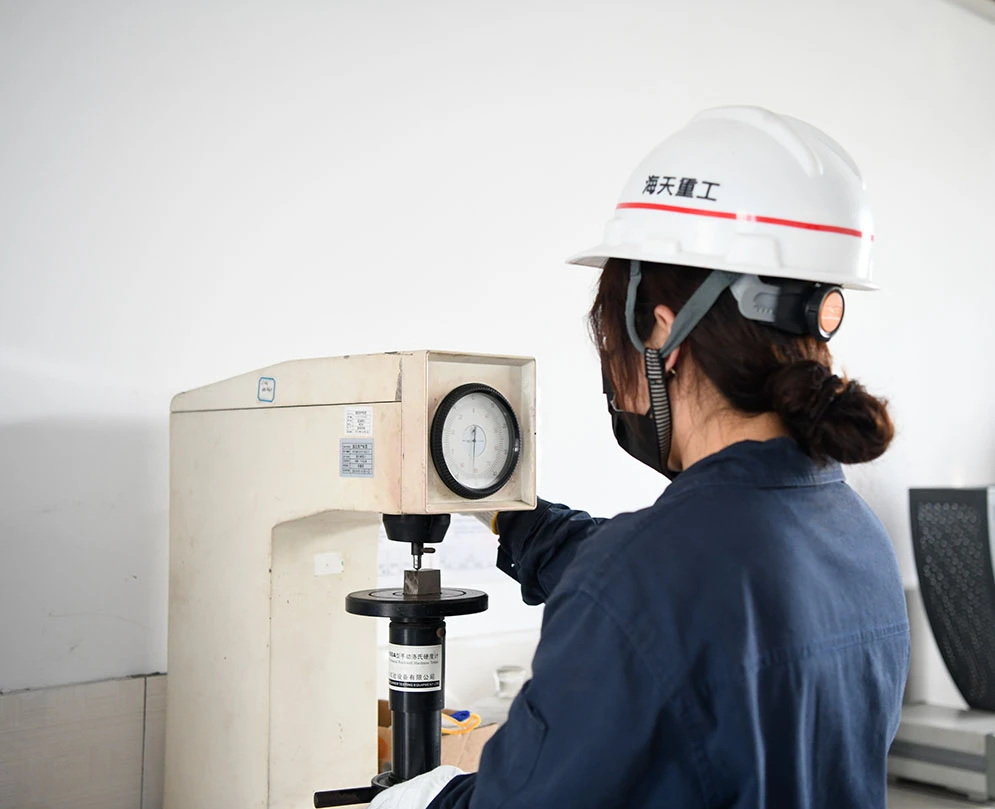
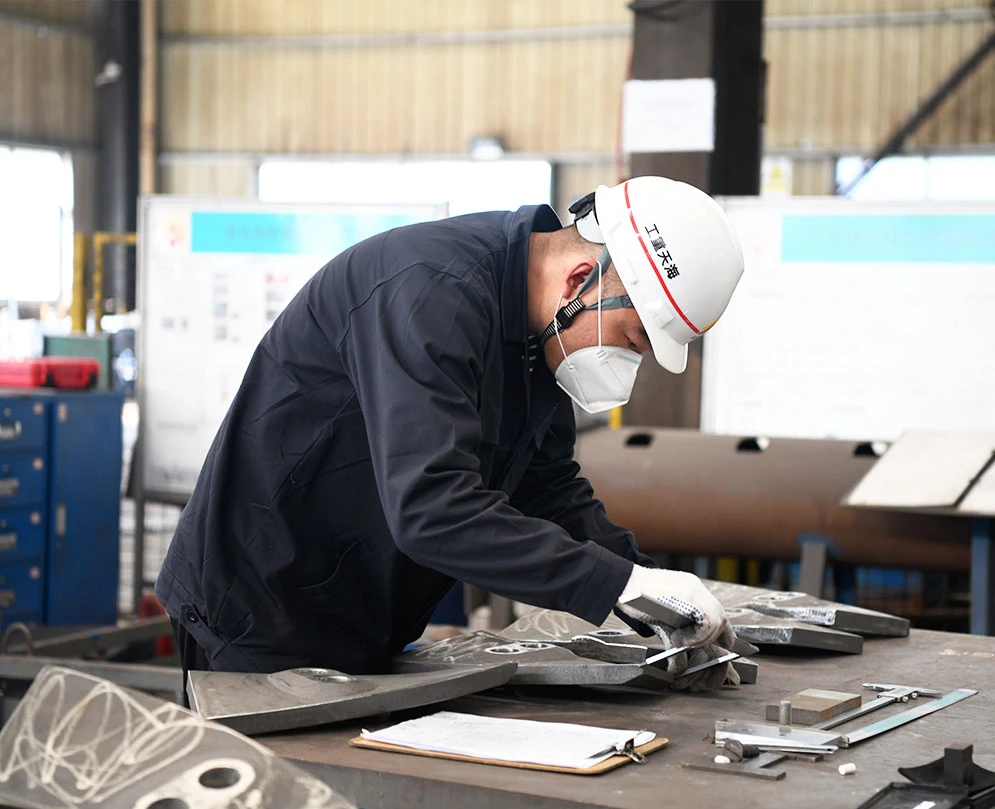
-
Control de parámetros de proceso
Control de temperatura: controle la temperatura durante la fundición, el vertido y el tratamiento térmico para garantizar que el metal se trate dentro del rango de temperatura adecuado para garantizar la calidad del producto.
Control de tiempos: Controlar el tiempo de cada proceso para asegurar que cada proceso se realice en su totalidad y sin excesos para evitar defectos.
Control de presión: Durante el proceso de vertido y moldeado, el tamaño y la distribución de la presión se controlan mediante el vacío a través de una membrana transparente para garantizar la uniformidad y estabilidad del líquido metálico que llena el molde.
-
Aplicación de equipos de prueba.
Detección por microscopio metalúrgico: observe y analice la estructura metálica para detectar si existen defectos como poros e inclusiones en el interior del metal.
Detección ultrasónica: utilice tecnología ultrasónica para detectar defectos dentro del producto, como grietas, inclusiones, etc., para garantizar la calidad y confiabilidad del producto.
Prueba de dureza: Pruebe la dureza del producto para evaluar si su resistencia al desgaste y sus propiedades mecánicas cumplen con los requisitos.
-
Equipos de producción automatizados.
Sistema de control automatizado: utilice sistemas de control automatizados avanzados para monitorear el proceso de producción, lograr un control y ajuste precisos de los parámetros de producción y mejorar la consistencia y estabilidad del producto.
-
control de calidad manual
Inspección del técnico de procesos: los técnicos de procesos inspeccionan periódicamente la línea de producción para garantizar que el equipo esté funcionando normalmente y que los parámetros de producción cumplan con los requisitos.
Supervisión de la operación del operador del proceso: Supervise la operación del operador del proceso para garantizar que la operación sea estandarizada y precisa, y reducir el impacto de los errores operativos en la calidad del producto.
-
Análisis y mejora de datos.
Recopilación y análisis de datos de calidad: recopile diversos datos de calidad en el proceso de producción, realice análisis estadísticos, encuentre problemas a tiempo y tome medidas de mejora.
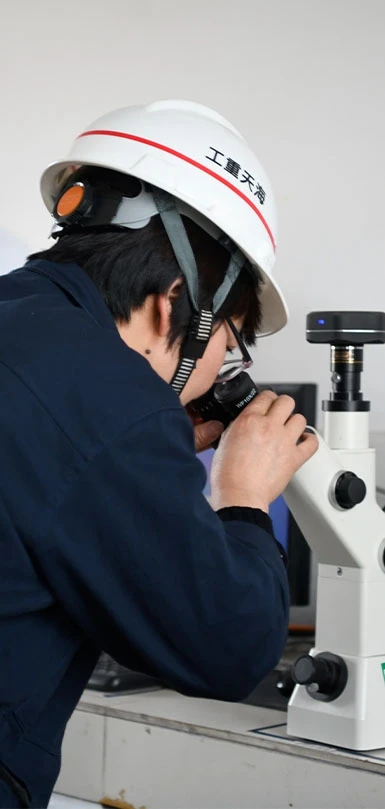
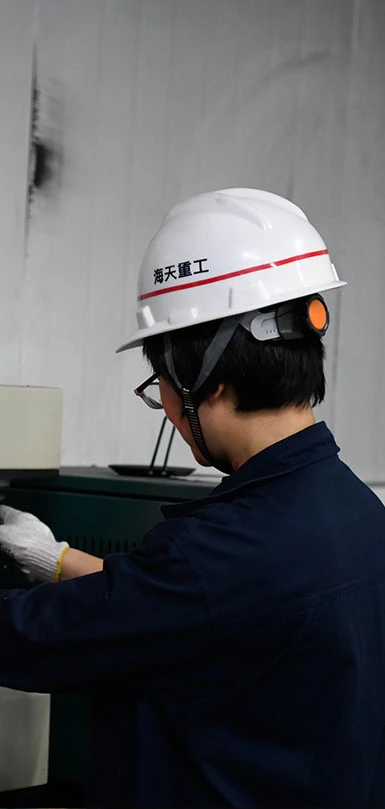
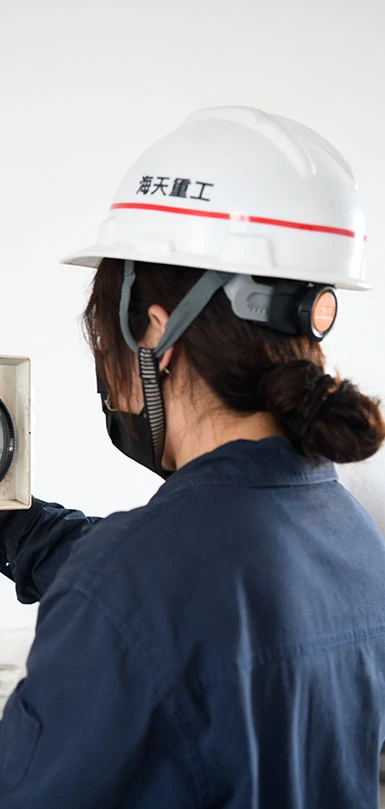
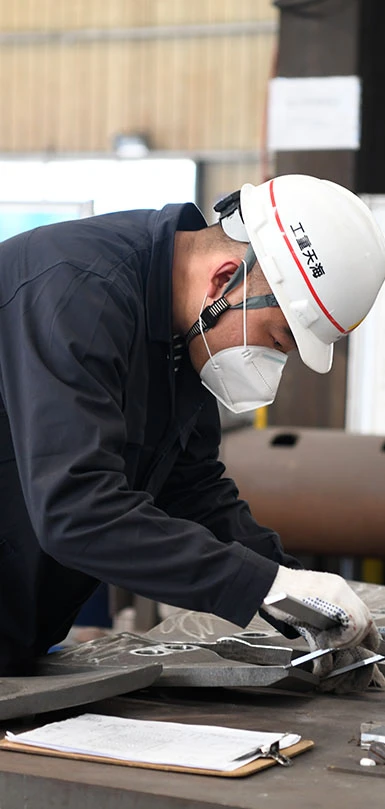
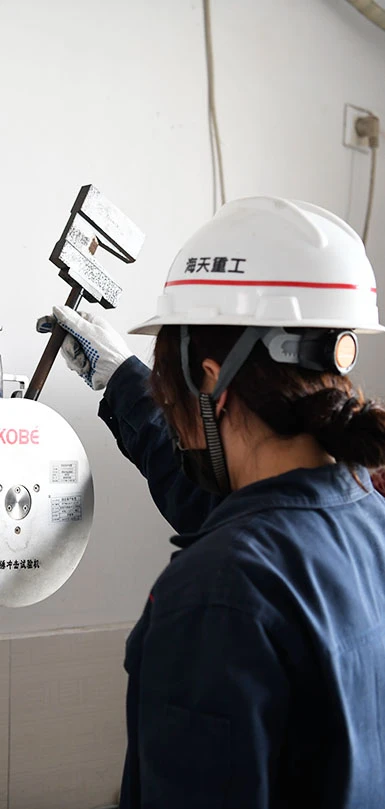
Si está interesado en nuestros productos o tiene alguna pregunta, no dude en contactarnos.
Brindaremos servicios de consultoría profesional y soluciones personalizadas de acuerdo a sus necesidades.
ENVIAR CONSULTA AHORAInformación del contacto
Teléfono: 0555-71661667166199
Fax: 0555-6971198
Sitio web: https://www.htwearparts.com
Correo electrónico: info@mashthi.com
Código postal: 243141
Dirección: Parque industrial Xinshi, distrito de Bowang, ciudad de Ma'anshan, provincia de Anhui, China