Production Capacity
The company has been deeply involved in the casting industry for 20 years. The research and development center is a two-story technology center with a construction area of more than 1,200 square meters. It is a provincial enterprise technology and industrial design center. The technology center is equipped with imported ARL2460 direct reading spectrometer, saturation magnetization system measuring instrument, WFW-600 universal material testing machine, JB30B impact testing machine, cooling characteristics tester, optical metallographic microscope, sand detector and other advanced testing instruments and equipment at home and abroad, with innovative design capabilities. Vertical production line, lost foam production line, cold core shell casting, 3D printing production line. Product research and development covers from 0.5kg to 8000kg, corresponding to the molding line for batch products, and the manual line for single-piece heavy products. There are engraving machines that can engrave wooden molds, and 3D printing equipment that can print sand cores for pouring, reducing mold opening time. The company has passed the 1SO9001 quality system certification, and the production process is equipped with professional inspection, final inspection and shipment inspection personnel. The product final inspection coverage rate reaches 100%, which effectively guarantees the quality and stability of the company's products.
-
20
20 years of experience in the foundry industry
-
1200M2
Building area of more than 1,200 square meters
-
100%
Product final inspection coveragerate reaches 100%
-
DISA vertical molding line
Production Capacity: Typically in the range of 100-150 castings per hour, depending on casting size and complexity.
Mould Size: Moulds suitable for small to medium castings, with a maximum mould size of approximately 335 x 335 mm.
Moulding Method: Vertical moulding, using DISA's high pressure moulding technology. -
Lost Foam Molding Line
Production capacity: Usually in the range of 50-100 castings per hour, depending on the size and complexity of the casting.
Mould size: Suitable for larger lost foam, usually the maximum mould size can reach 500 x 500 mm or larger.
Casting method: Lost foam casting, using high temperature gas melting lost foam, capable of producing complex shapes and high precision castings. -
V method production line
Production capacity: The weight of castings produced per hour is about 10-20 tons (depending on the casting size and process parameters)
Casting size: The maximum size can reach 3000 mm x 2000 mm x 1500 mm (can be customized according to needs)
Number of molds: Multiple molds design, can be configured according to production needs. -
Accumulation chain shot blasting production line
Shot blasting capacity: Each shot blasting machine has a shot blasting capacity of 180-200 kg per minute
Shot blasting machine power: Each shot blasting machine has a power of 11-15 kW, and the total power is 88-120 kW
Shot blasting speed: 70-80 m/s. -
Cold core shell molding production line
Production capacity: The production capacity is generally between 30-60 castings per hour, depending on the size and complexity of the casting.
Mould size: Suitable for medium to large moulds, usually the maximum mould size can reach 400 x 400 mm or larger.
Casting method: Cold core shell casting, using cold core shell process, capable of producing high-precision and complex castings.
Automation level: It has a high level of automation, including automatic mould loading, forming, pouring, cooling and demoulding functions. -
Gas tunnel furnace heat treatment production line
Furnace structure: High-strength refractory bricks, shell is high-strength steel plate
Furnace size: Customized according to specific needs, generally 1.5 meters to 3 meters high, 1 meter to 2.5 meters wide
Furnace volume: about 3 cubic meters. -
Unmanned warehouse intelligent control stereoscopic storage system
WMS (Warehouse Management System): Provides functions such as inventory management, order processing, picking instructions, warehousing and outbound operations
WCS (Warehouse Control System): Real-time monitoring of the operating status of automated equipment and optimization of equipment scheduling
Operation interface: Touch screen or computer control interface, supports remote monitoring and management. -
Will vertical production line
Production capacity: 90-120 sets per hour (depending on specific production conditions)
Molding size: Standard size is 450mm x 600mm x 150-350mm (width x length x height), can be customized according to needs
Molding speed: 20-25 seconds/mold -
Medium frequency furnace
Melting capacity: Depending on the size of the furnace, usually between 5 tons and 15 tons
Melting time: About 1-2 hours (depending on the material and capacity)
Maximum melting temperature: 1600°C to 1800°C (depending on the specific material) -
Robot polishing workstation
Grinding tool type: Electric or pneumatic grinder (optional)
Grinding speed: Adjustable, typically ranging from 1000 to 5000 RPM
Number of grinding heads: Single or multiple (depending on configuration) -
3D printing equipment
Main machine size: 9000 × 1900 × 1950mm (length × width × height). The full box printing time is about 12 hours. The standard configuration is two working sand boxes, which can achieve 24-hour uninterrupted printing.
The inner size of the working sand box is 1800 × 1000 × 730mm (length × width × height), which meets the printing needs of most casting sand molds.
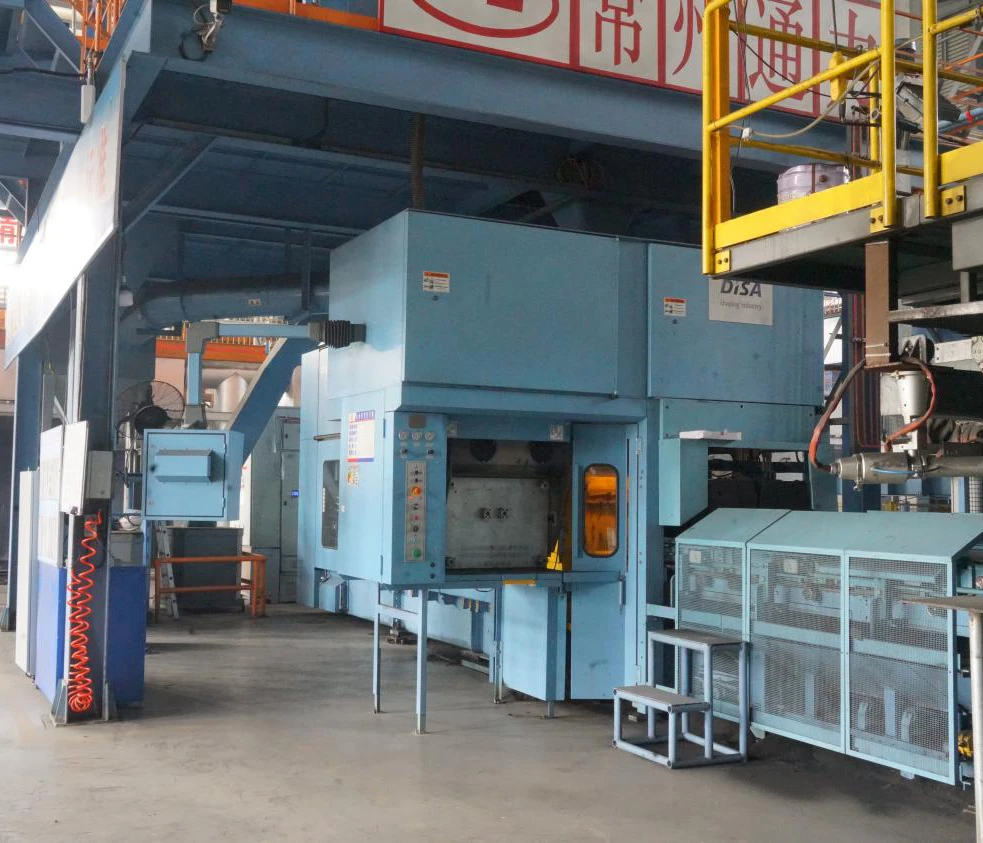
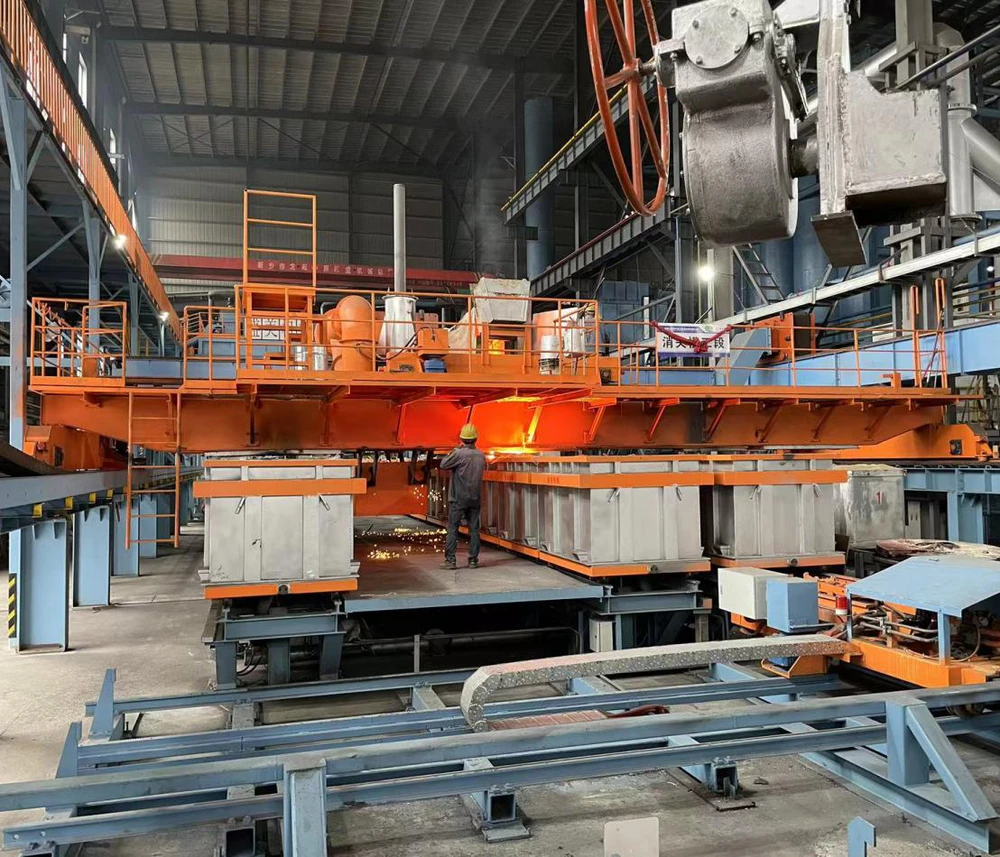
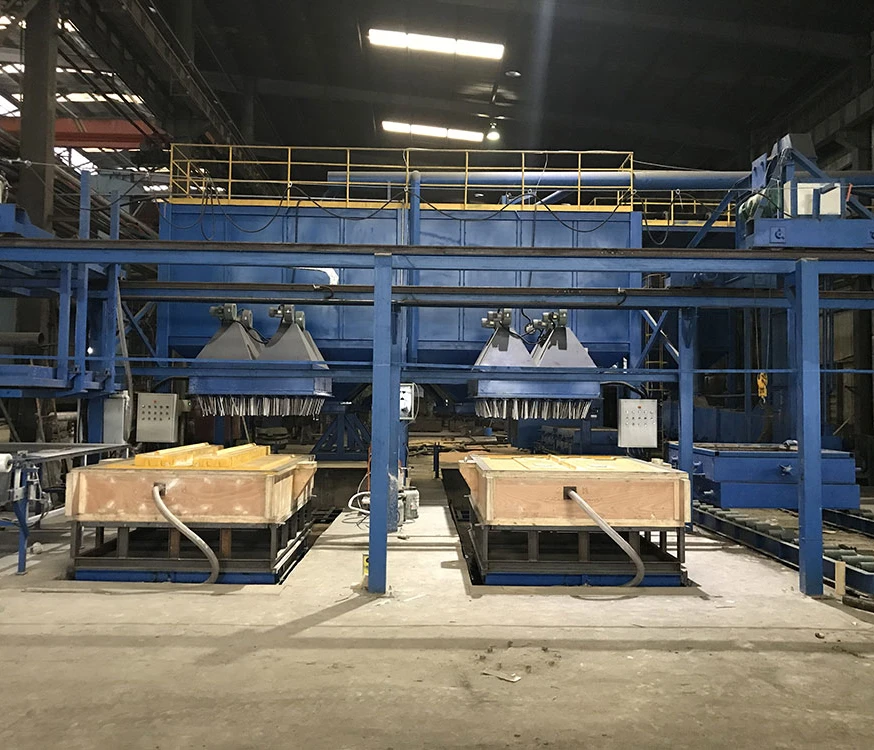
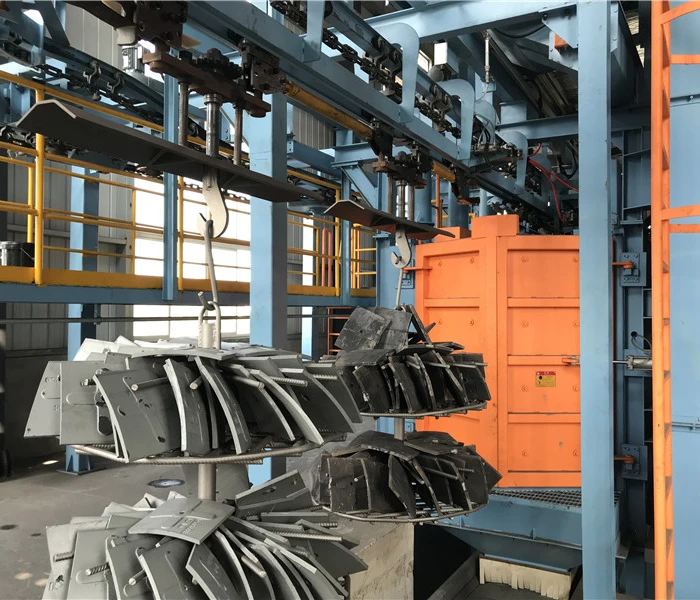
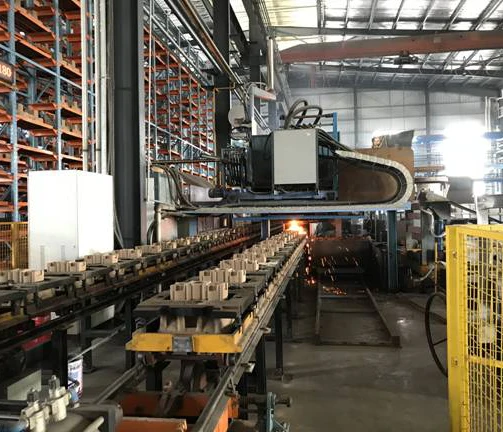
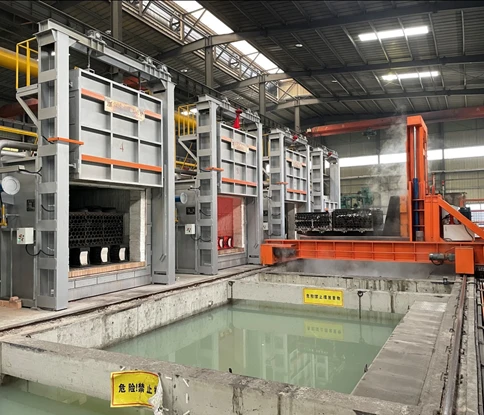
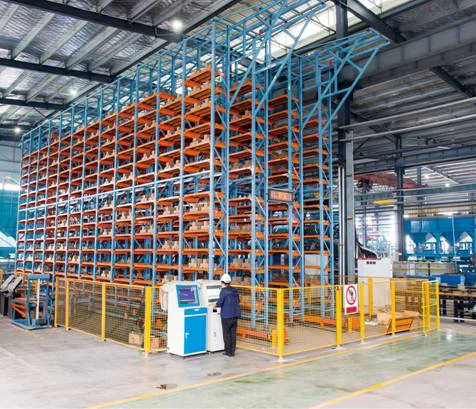
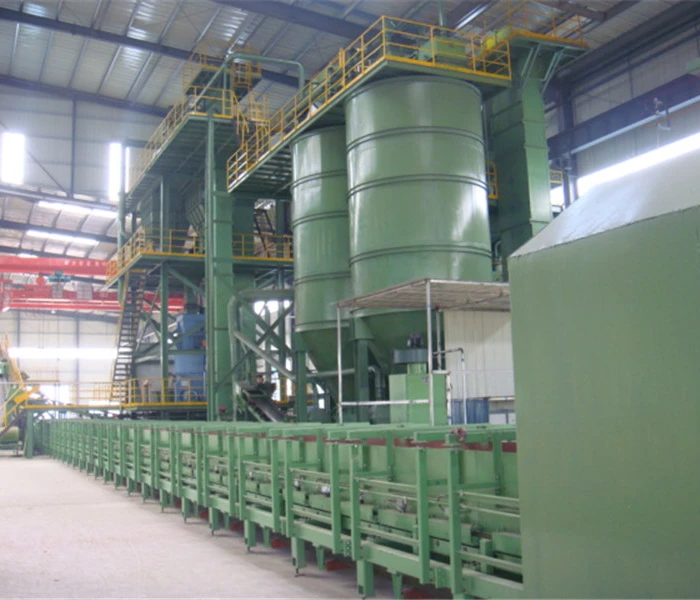
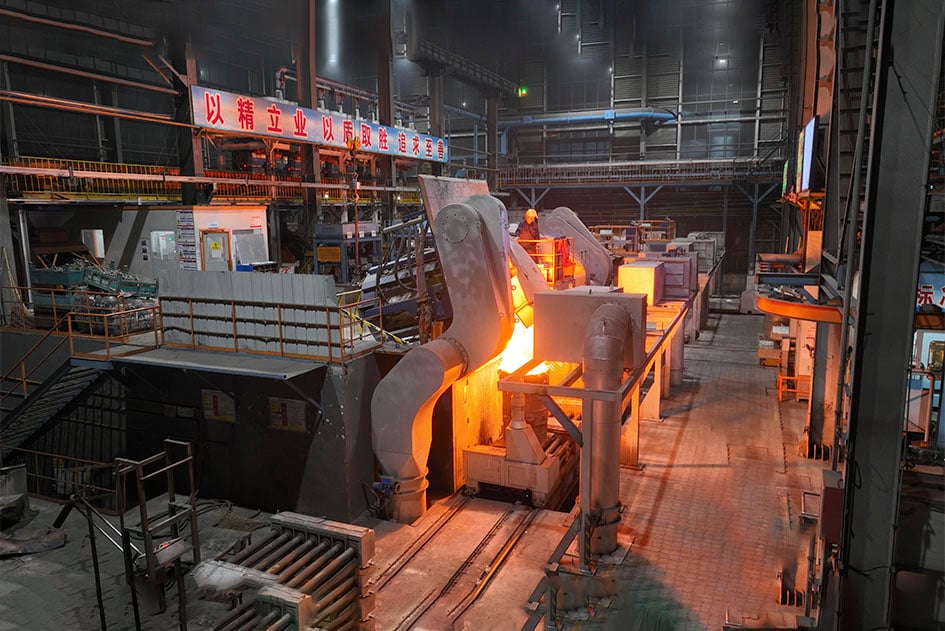
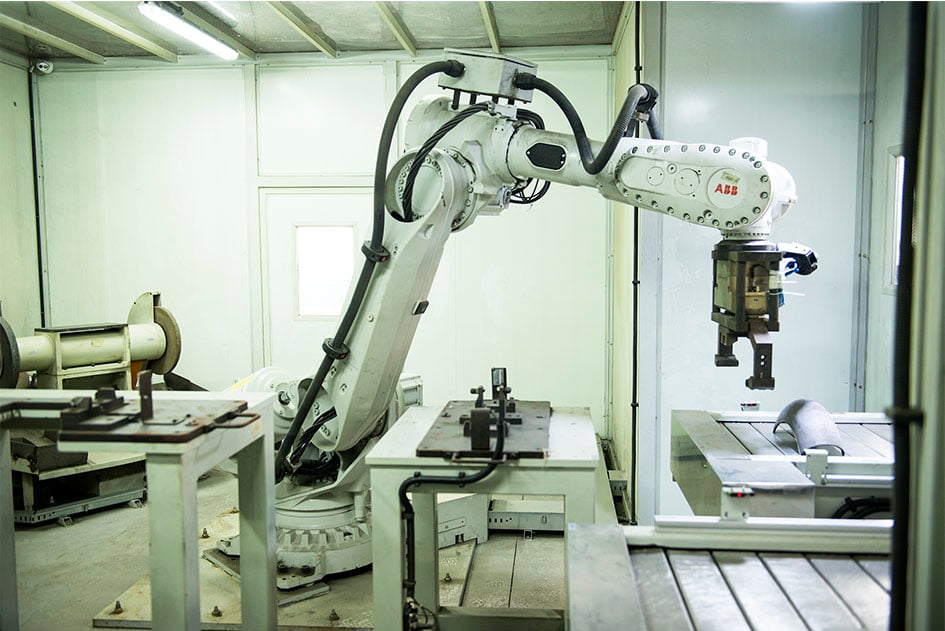
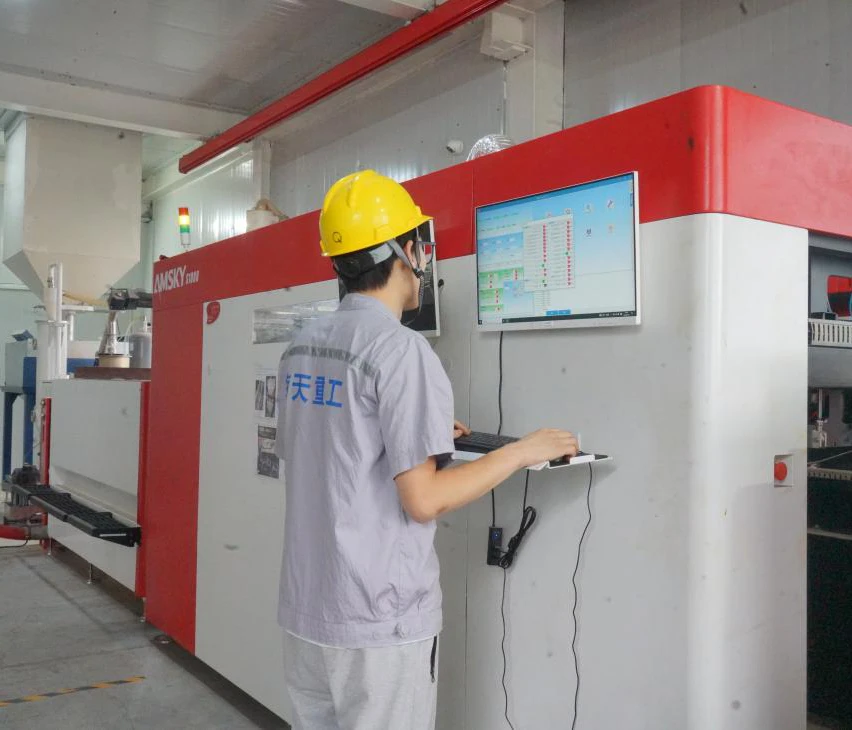
TEST EQUIPMENT
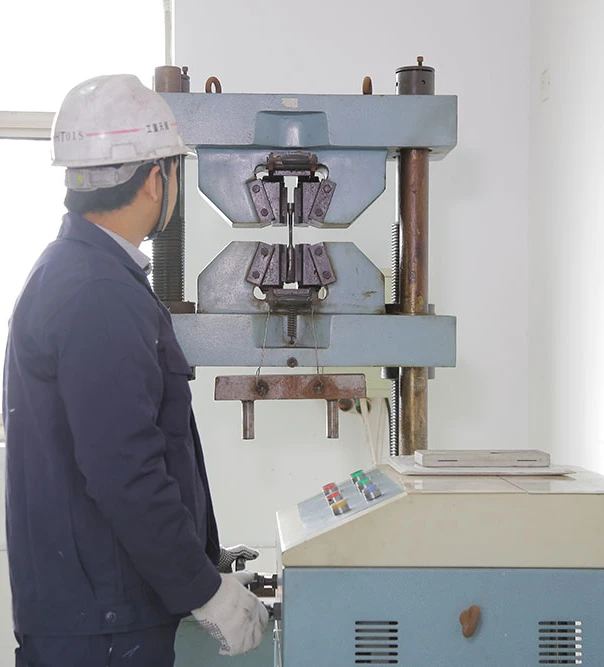
Tensile testing equipment

Impact energy testing equipment
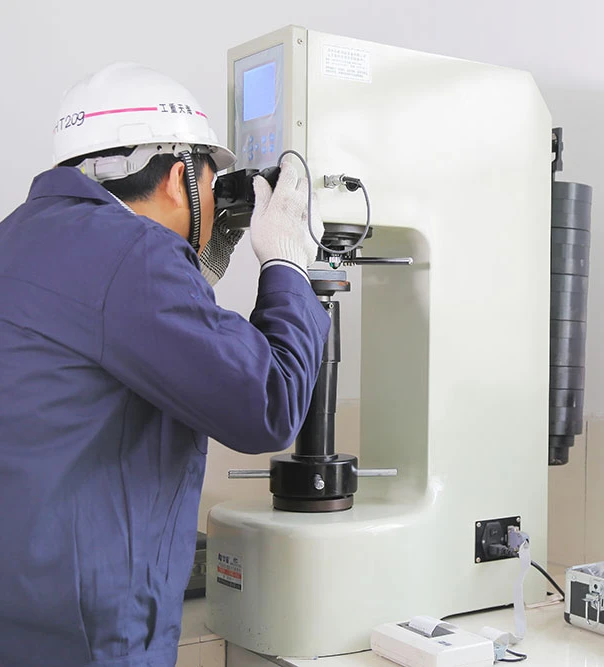
Brinell hardness testing equipment
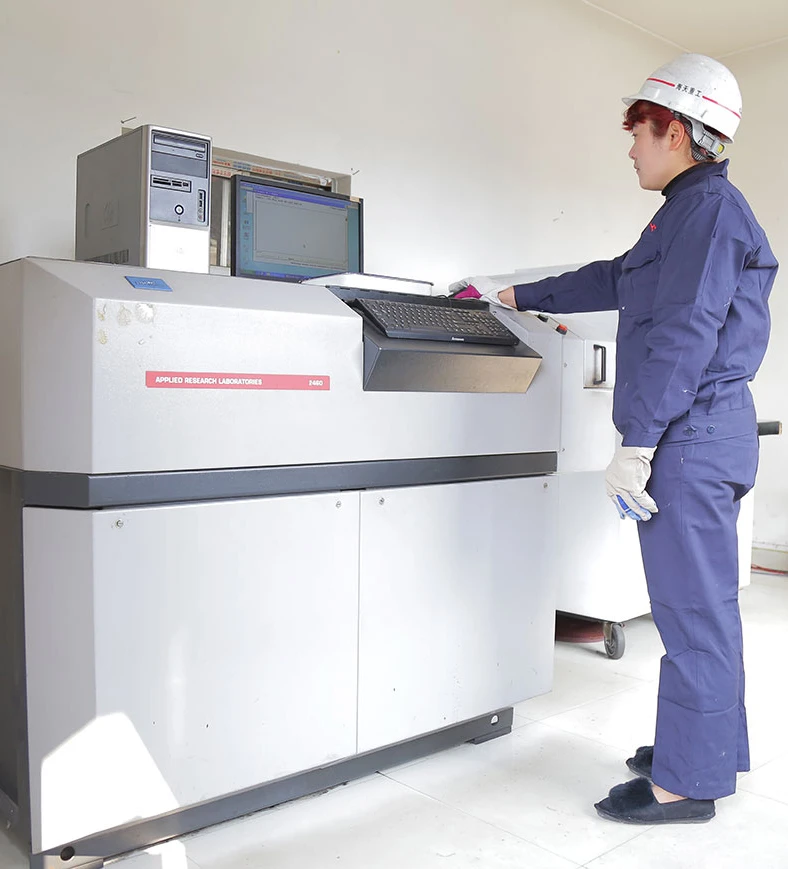
Spectrometer component detection equipment
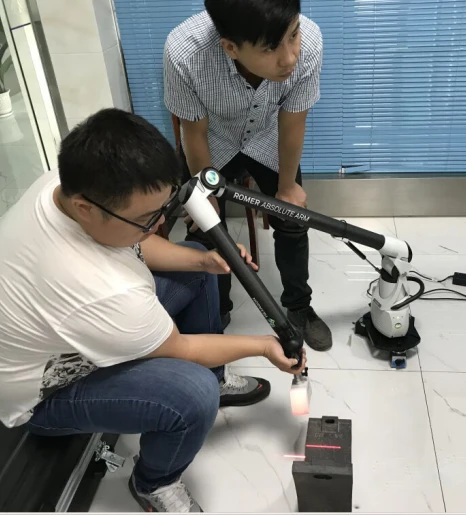
Triangulation Coordinate Measuring Machine
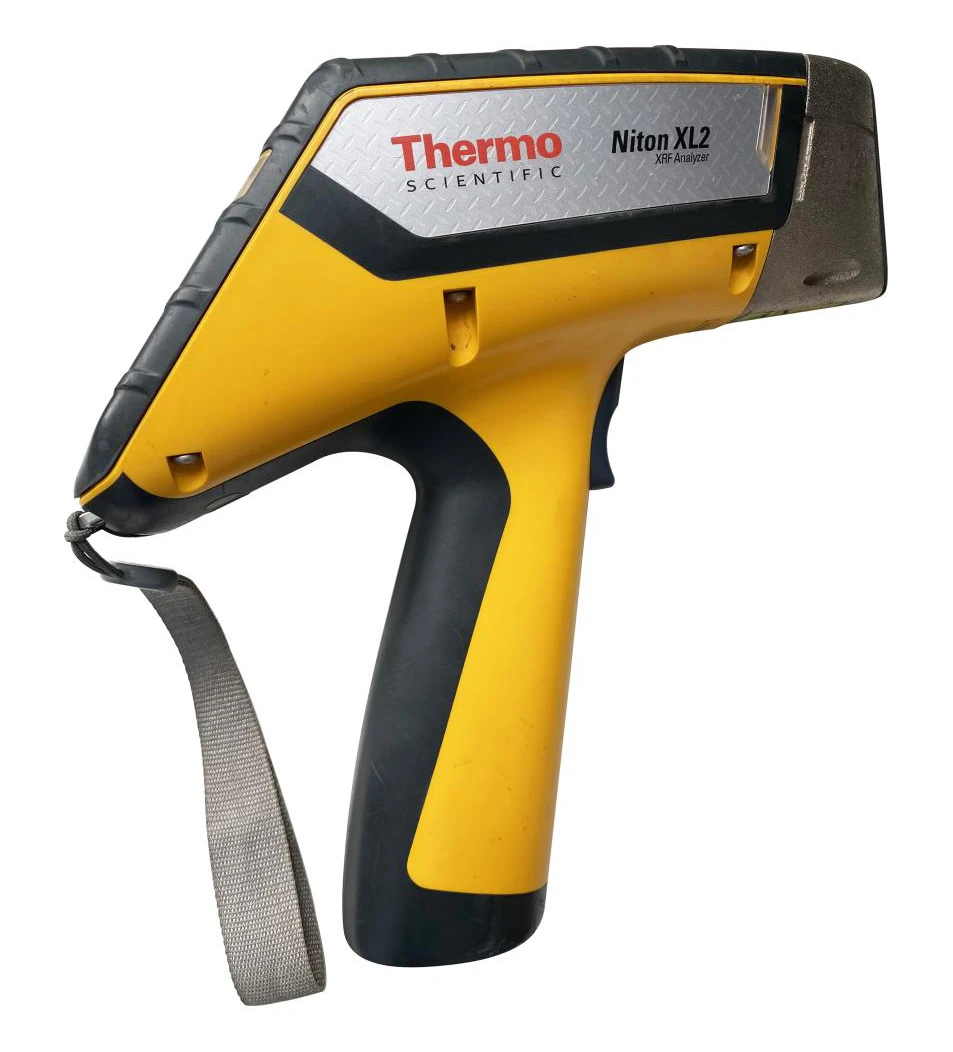
Handheld Spectrometer
PROCESS FIOW
-
01
Raw material selection
In the manufacturing process of wear-resistant parts, the selection of raw materials is crucial. We carefully select high-quality alloy materials to ensure that they have excellent wear resistance and strength, laying a solid foundation for the quality of the products.
-
02
Melting process
After the strictly proportioned raw materials enter the furnace, we use advanced smelting technology to ensure that the composition and temperature of the molten metal reach the optimal state, providing uniform and stable metal flow for the molding of the product.
-
03
Casting and molding
Through the exquisite casting process, the molten metal is injected into the mold to solidify and mold in a specific shape and size. Our craftsmen have been professionally trained and are proficient in various complex molding processes to ensure that the shape and size of the products are accurate and the quality is stable.
-
04
Shot blasting and grinding
After demolding, the product undergoes a fine grinding process to remove surface defects and burrs, making its surface smooth and flat. Our craftsmen use delicate techniques and superb skills to care for each product and give it a perfect appearance and texture.
-
05
Heat treatment process
After the heat treatment process, the structure and performance of the product are further stabilized and improved. According to the specific requirements of the product, we use different heat treatment processes to make it have excellent wear resistance, strength and corrosion resistance, and adapt to the needs of various harsh working environments.
-
06
Painting and inspection
The product is painted, which not only beautifies the appearance, but also improves the corrosion resistance and wear resistance of its surface. After that, it goes through a strict inspection process to ensure that all indicators of the product meet the standard requirements and provide customers with reliable product guarantees.
-
07
Warehouse entry and delivery
Finally, the product undergoes strict quality inspection and is safely stored in the warehouse, ready to be delivered at any time. Once we receive the customer's order, we will complete the delivery on time, quantity and quality to ensure that the product is delivered to the customer safely and on time.
QUALITY CONTROL DURING PRODUCTION
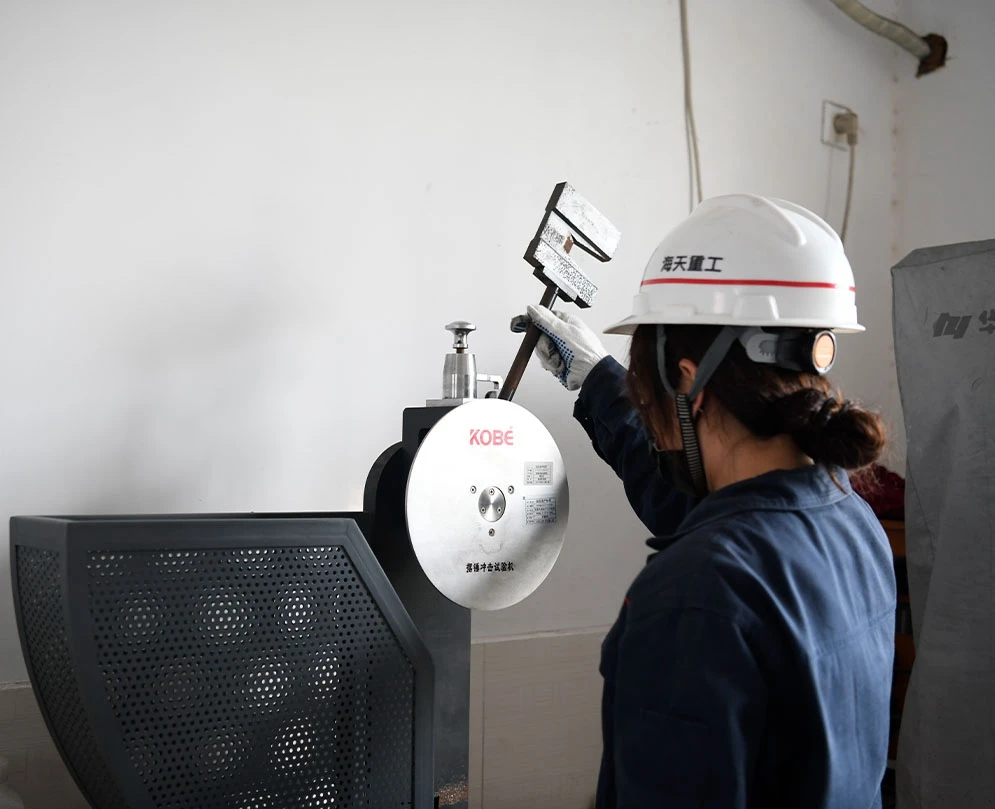
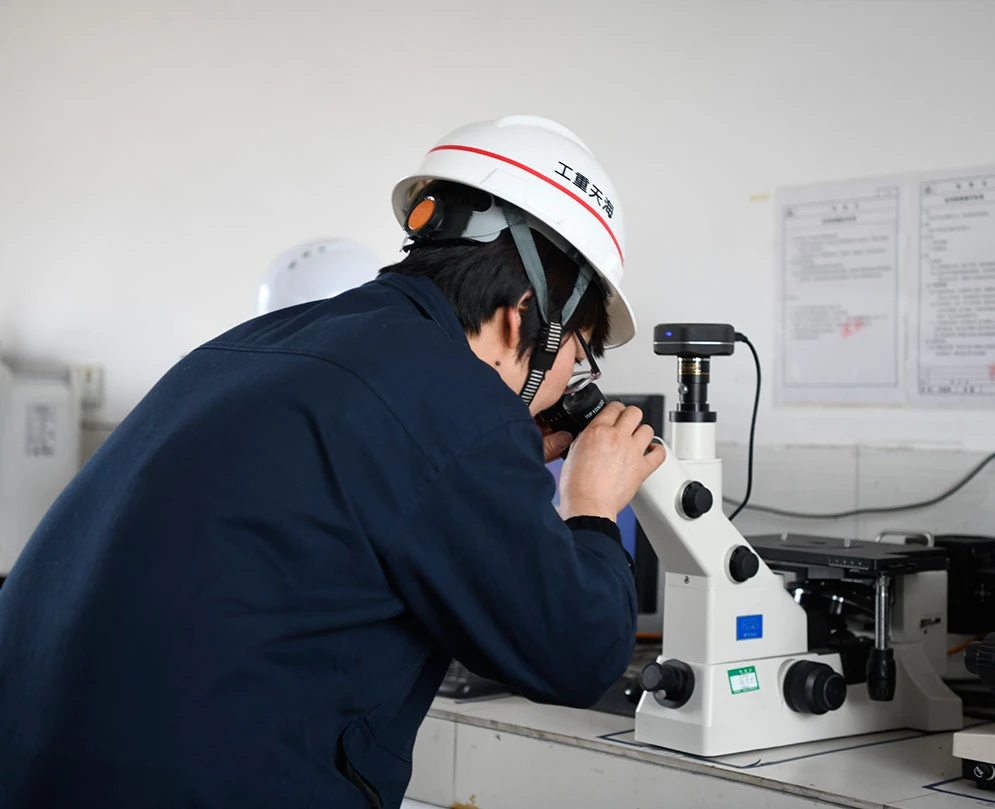
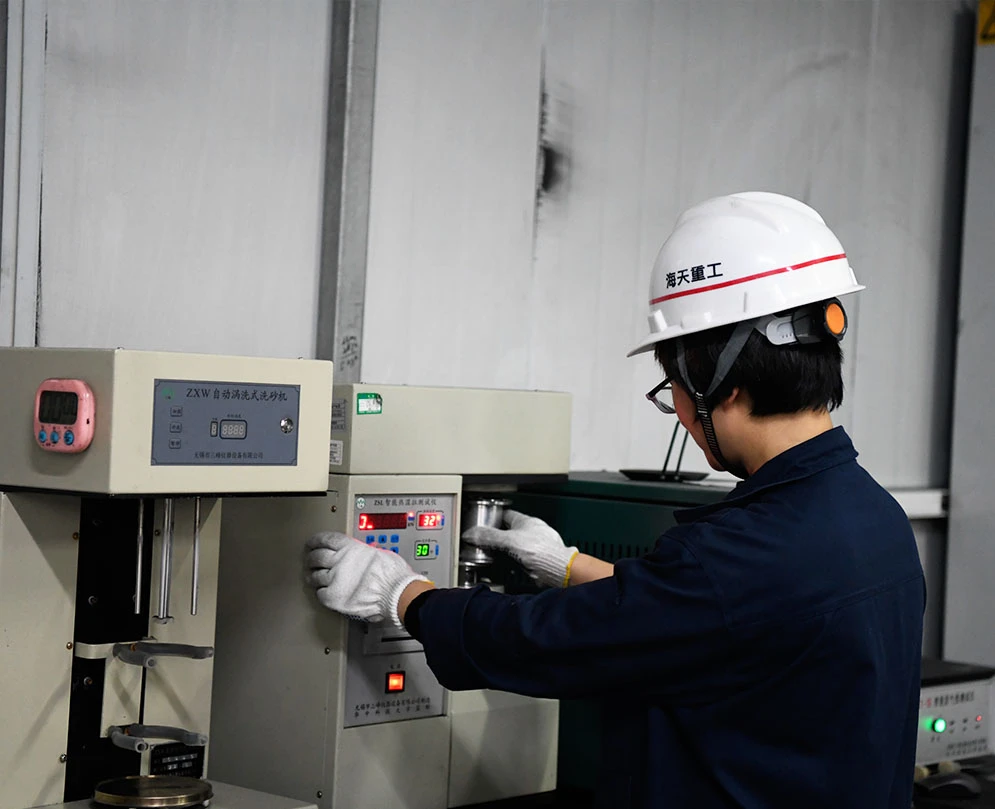
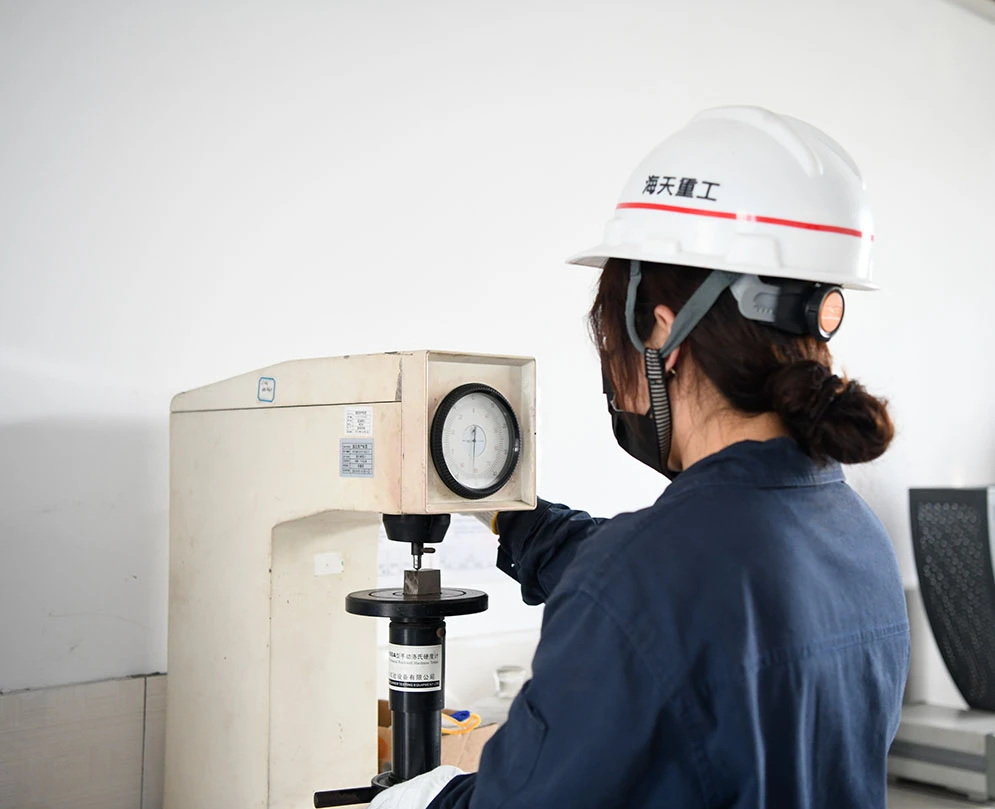
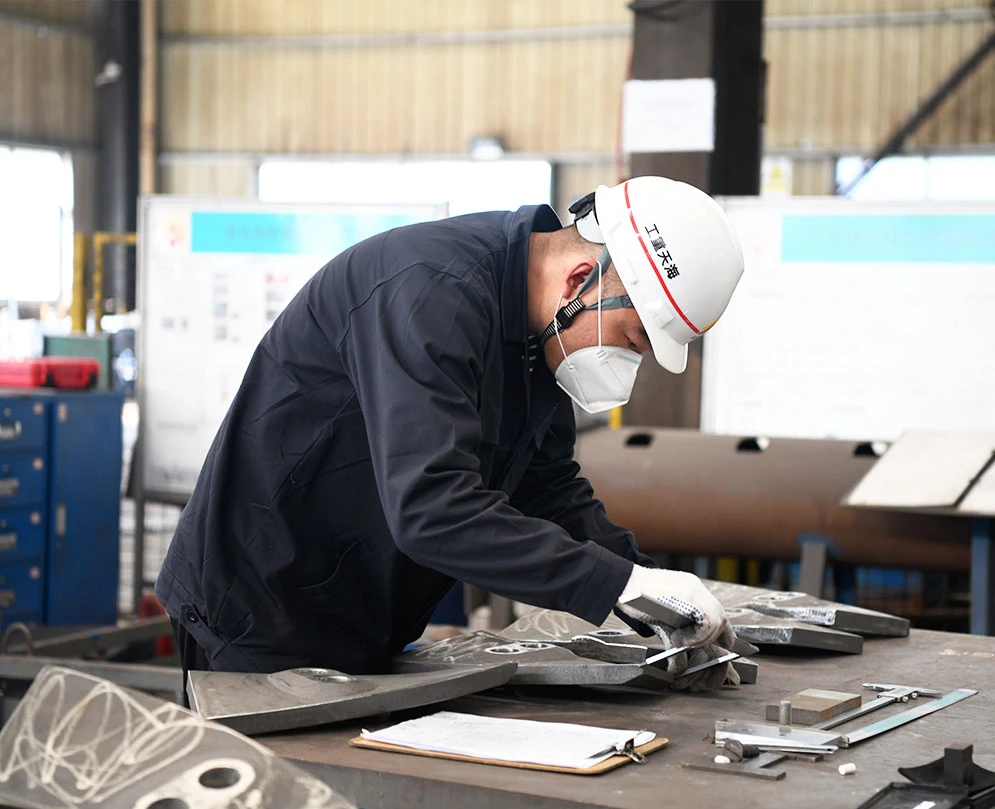
-
Process parameter control
Temperature control: Monitor the temperature during smelting, pouring and heat treatment to ensure that the metal is treated within the appropriate temperature range to ensure product quality.
Time control: Control the time of each process to ensure that each process is fully carried out without excessive to avoid defects.
Pressure control: During the pouring and molding process, the size and distribution of pressure are controlled by vacuuming through a transparent membrane to ensure the uniformity and stability of the metal liquid filling the mold.
-
Application of testing equipment
Metallurgical microscope detection: Observe and analyze the metal structure to detect whether there are defects such as pores and inclusions inside the metal.
Ultrasonic detection: Use ultrasonic technology to detect defects inside the product, such as cracks, inclusions, etc., to ensure the quality and reliability of the product.
Hardness test: Test the hardness of the product to evaluate whether its wear resistance and mechanical properties meet the requirements.
-
Automated production equipment
Automated control system: Use advanced automated control systems to monitor the production process, achieve precise control and adjustment of production parameters, and improve product consistency and stability.
-
Manual quality control
Process technician inspection: Process technicians regularly inspect the production line to ensure that the equipment is operating normally and the production parameters meet the requirements.
Process operator operation supervision: Supervise the operation of the process operator to ensure that the operation is standardized and accurate, and reduce the impact of operational errors on product quality.
-
Data analysis and improvement
Quality data collection and analysis: Collect various quality data in the production process, conduct statistical analysis, find problems in time and take improvement measures.
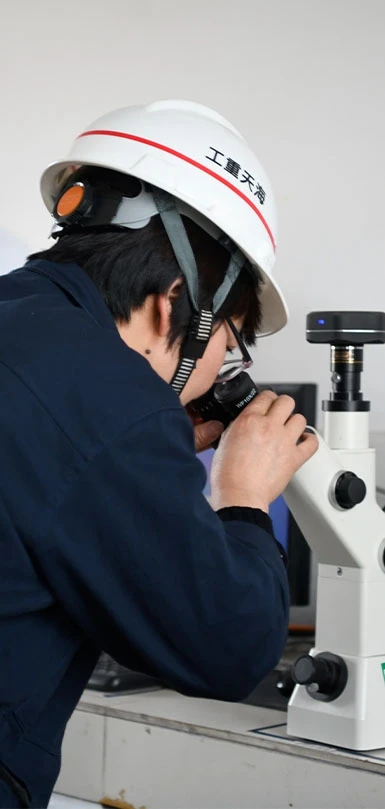
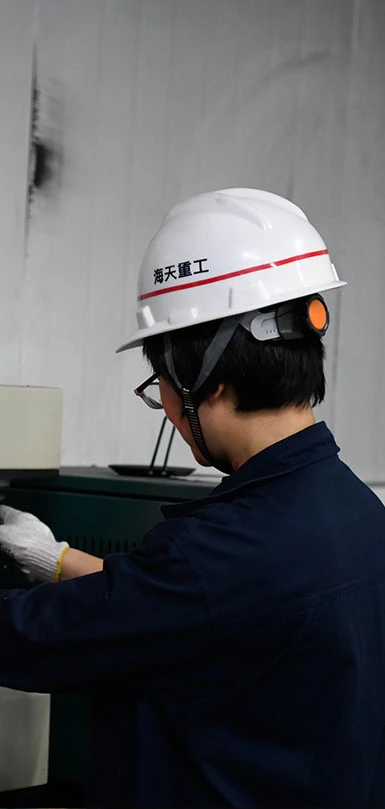
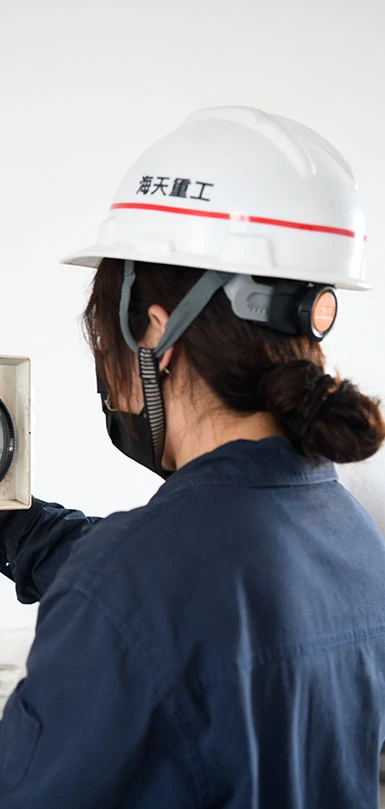
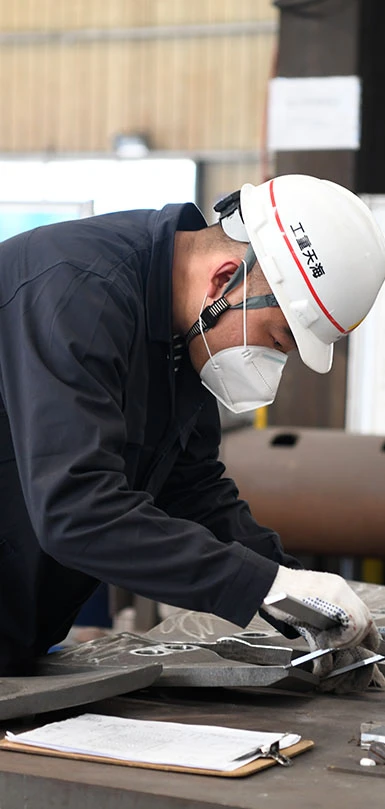
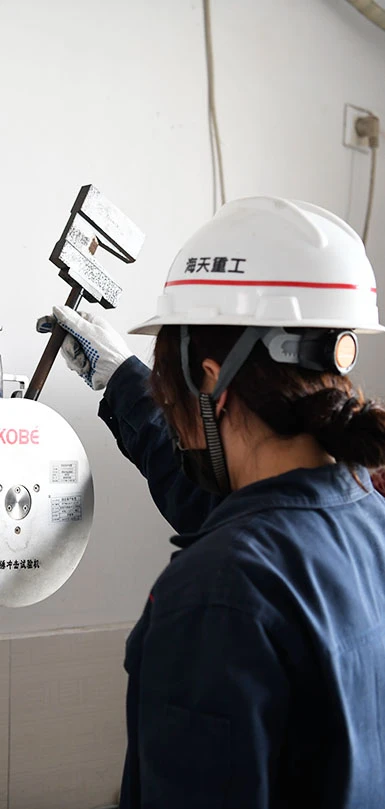
If you are interested in our products or have any questions, please feel free to contact us.
We will provide professional consulting services and customized solutions according to your needs.
SEND INQUIRY NOWContact information
Tel: 0555-71661667166199
Fax: 0555-6971198
Website: https://www.htwearparts.com
Email: info@mashthi.com
Postal code: 243141
Address: Xinshi Industrial Park, Bowang District, Ma’anshan City, Anhui Province, China