Produktionskapazität
Das Unternehmen ist seit 20 Jahren intensiv in der Gussindustrie tätig. Das Forschungs- und Entwicklungszentrum ist ein zweistöckiges Technologiezentrum mit einer Baufläche von mehr als 1.200 Quadratmetern. Es ist ein provinzielles Zentrum für Unternehmenstechnologie und Industriedesign. Das Technologiezentrum ist mit einem importierten direkt ablesbaren Spektrometer ARL2460, einem Sättigungsmagnetisierungssystem-Messgerät, einer universellen Materialprüfmaschine WFW-600, einer JB30B-Schlagprüfmaschine, einem Kühlcharakteristik-Tester, einem optischen metallografischen Mikroskop, einem Sanddetektor und anderen fortschrittlichen Prüfinstrumenten und -geräten zu Hause ausgestattet und im Ausland, mit innovativen Designfähigkeiten. Vertikale Produktionslinie, Produktionslinie für verlorenen Schaum, Kaltkern-Schalenguss, 3D-Druck-Produktionslinie. Die Produktforschung und -entwicklung erstreckt sich von 0,5 kg bis 8000 kg, entsprechend der Formlinie für Chargenprodukte und der manuellen Linie für einteilige schwere Produkte. Es gibt Graviermaschinen, die Holzformen gravieren können, und 3D-Druckgeräte, die Sandkerne zum Gießen drucken können, wodurch die Öffnungszeit der Formen verkürzt wird. Das Unternehmen hat die Zertifizierung des Qualitätssystems 1SO9001 bestanden und der Produktionsprozess ist mit professionellem Personal für Inspektion, Endkontrolle und Versandkontrolle ausgestattet. Die Abdeckungsrate der Produktendkontrolle erreicht 100 %, was die Qualität und Stabilität der Produkte des Unternehmens effektiv garantiert.
-
20
20 Jahre Erfahrung in der Gießereibranche
-
1200M2
Gebäudefläche von mehr als 1.200 Quadratmetern
-
100%
Abdeckungsrate der Produktendkontrolle erreicht 100 %
-
Vertikale Formanlage DISA
Produktionskapazität: Typischerweise im Bereich von 100–150 Gussstücken pro Stunde, je nach Gussstückgröße und -komplexität.
Formgröße: Formen, die für kleine bis mittlere Gussteile geeignet sind, mit einer maximalen Formgröße von ca. 335 x 335 mm.
Formverfahren: Vertikales Formen unter Verwendung der Hochdruck-Formtechnologie von DISA. -
Formanlage für verlorenen Schaum
Produktionskapazität: Normalerweise im Bereich von 50–100 Gussstücken pro Stunde, abhängig von der Größe und Komplexität des Gussstücks.
Formgröße: Geeignet für größeren verlorenen Schaum, normalerweise kann die maximale Formgröße 500 x 500 mm oder mehr erreichen.
Gießmethode: Schaumausschmelzguss unter Verwendung von Hochtemperaturgas zum Schmelzen von Schaum, mit dem komplexe Formen und hochpräzise Gussteile hergestellt werden können. -
Produktionslinie nach V-Methode
Produktionskapazität: Das Gewicht der produzierten Gussteile pro Stunde beträgt etwa 10-20 Tonnen (abhängig von der Gussstückgröße und den Prozessparametern).
Gussgröße: Die maximale Größe kann 3000 mm x 2000 mm x 1500 mm erreichen (kann je nach Bedarf angepasst werden)
Anzahl der Formen: Design mehrerer Formen, kann entsprechend den Produktionsanforderungen konfiguriert werden. -
Produktionslinie für das Kugelstrahlen mit Akkumulationskette
Strahlleistung: Jede Strahlanlage verfügt über eine Strahlleistung von 180–200 kg pro Minute
Leistung der Strahlanlage: Jede Strahlanlage hat eine Leistung von 11–15 kW und die Gesamtleistung beträgt 88–120 kW
Strahlgeschwindigkeit: 70-80 m/s. -
Produktionslinie für Kaltkern-Schalenformung
Produktionskapazität: Die Produktionskapazität liegt im Allgemeinen zwischen 30 und 60 Gussteilen pro Stunde, abhängig von der Größe und Komplexität des Gussstücks.
Formgröße: Geeignet für mittlere bis große Formen, normalerweise kann die maximale Formgröße 400 x 400 mm oder mehr erreichen.
Gießmethode: Kaltkern-Schalenguss mit Kaltkern-Schalenverfahren, mit dem hochpräzise und komplexe Gussteile hergestellt werden können.
Automatisierungsgrad: Es verfügt über einen hohen Automatisierungsgrad, einschließlich automatischer Formlade-, Form-, Gieß-, Kühl- und Entformungsfunktionen. -
Produktionslinie für die Wärmebehandlung von Gastunnelöfen
Ofenstruktur: Hochfeste feuerfeste Steine, Mantel aus hochfester Stahlplatte
Ofengröße: Je nach Bedarf individuell angepasst, im Allgemeinen 1,5 bis 3 Meter hoch, 1 bis 2,5 Meter breit
Ofenvolumen: ca. 3 Kubikmeter. -
Unbemanntes stereoskopisches Lagersystem mit intelligenter Steuerung
WMS (Warehouse Management System): Bietet Funktionen wie Bestandsverwaltung, Auftragsabwicklung, Kommissionierungsanweisungen, Lagerhaltung und Ausgangsvorgänge
WCS (Warehouse Control System): Echtzeitüberwachung des Betriebsstatus automatisierter Geräte und Optimierung der Geräteplanung
Bedienoberfläche: Touchscreen oder Computersteuerungsschnittstelle, unterstützt Fernüberwachung und -verwaltung. -
Wird vertikale Produktionslinie
Produktionskapazität: 90–120 Sätze pro Stunde (abhängig von den spezifischen Produktionsbedingungen)
Formgröße: Die Standardgröße beträgt 450 mm x 600 mm x 150–350 mm (Breite x Länge x Höhe), kann je nach Bedarf angepasst werden
Formgeschwindigkeit: 20–25 Sekunden/Form -
Mittelfrequenzofen
Schmelzkapazität: Abhängig von der Größe des Ofens, normalerweise zwischen 5 Tonnen und 15 Tonnen
Schmelzzeit: ca. 1-2 Stunden (je nach Material und Kapazität)
Maximale Schmelztemperatur: 1600 °C bis 1800 °C (abhängig vom spezifischen Material) -
Roboter-Polierarbeitsplatz
Schleifwerkzeugtyp: Elektrischer oder pneumatischer Schleifer (optional)
Schleifgeschwindigkeit: Einstellbar, typischerweise im Bereich von 1000 bis 5000 U/min
Anzahl der Schleifköpfe: Einfach oder mehrfach (je nach Konfiguration) -
3D-Druckausrüstung
Hauptmaschinengröße: 9000 × 1900 × 1950 mm (Länge × Breite × Höhe). Die Druckzeit für die gesamte Schachtel beträgt etwa 12 Stunden. Die Standardkonfiguration besteht aus zwei funktionierenden Sandkästen, die einen unterbrechungsfreien 24-Stunden-Druck ermöglichen.
Die Innengröße des Arbeitssandkastens beträgt 1800 × 1000 × 730 mm (Länge × Breite × Höhe), was den Druckanforderungen der meisten Gusssandformen entspricht.
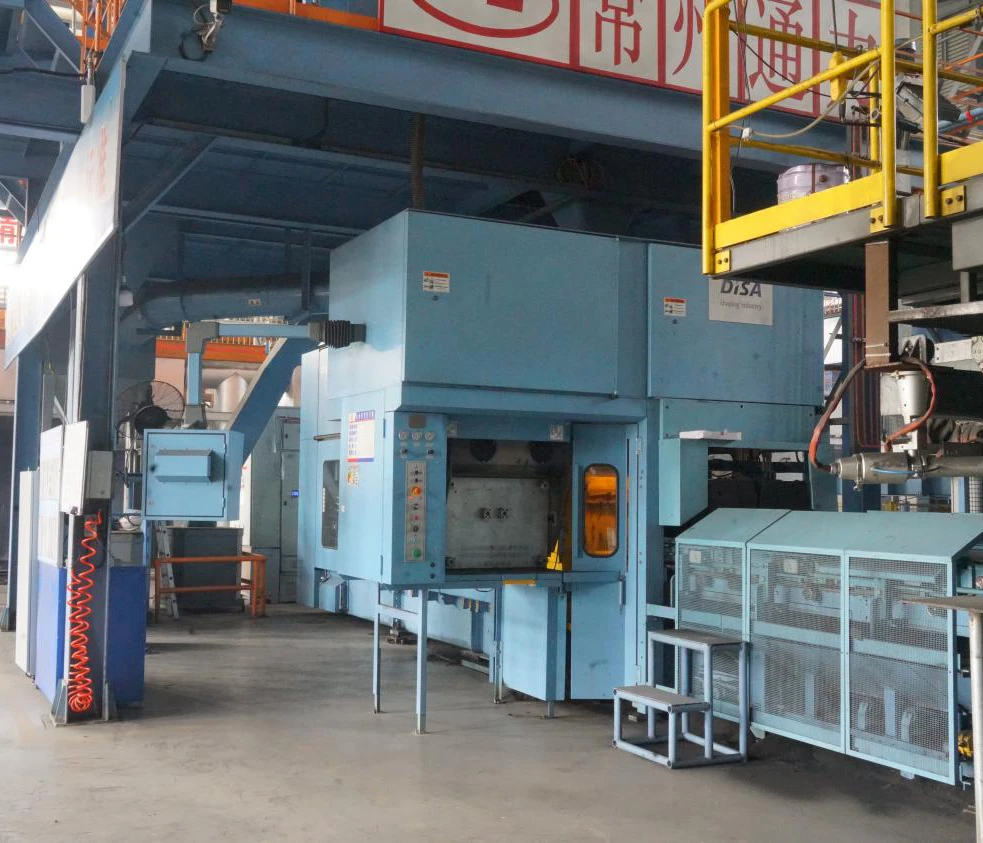
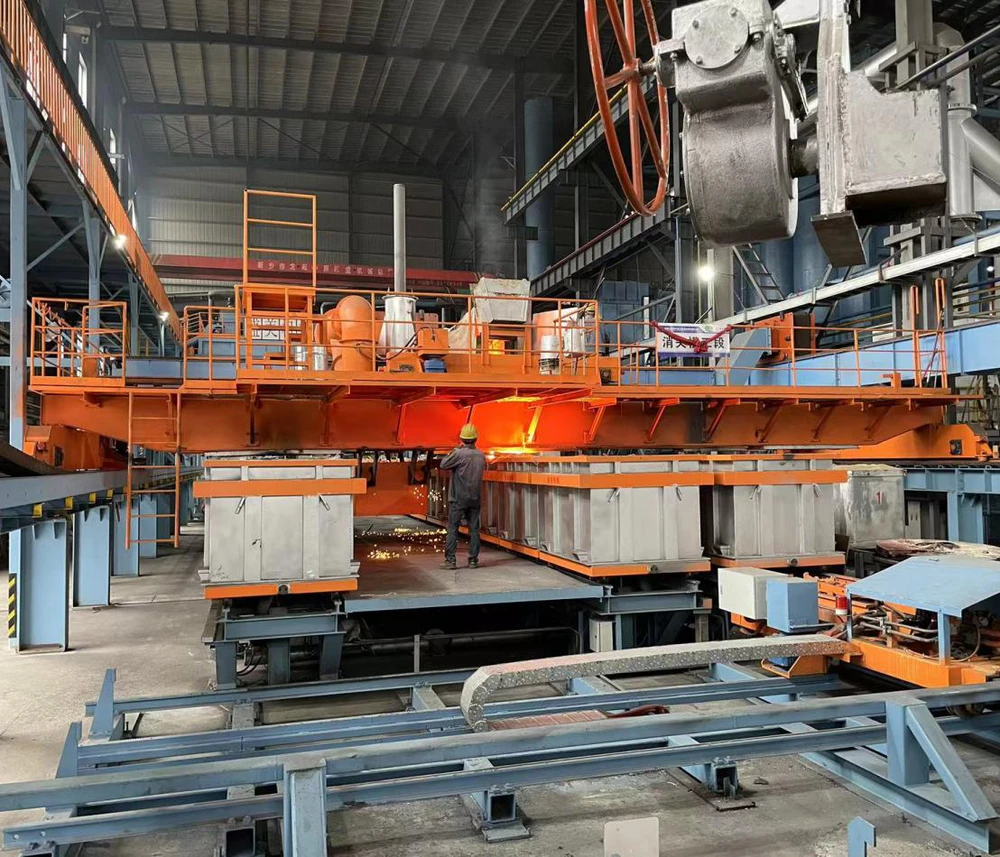
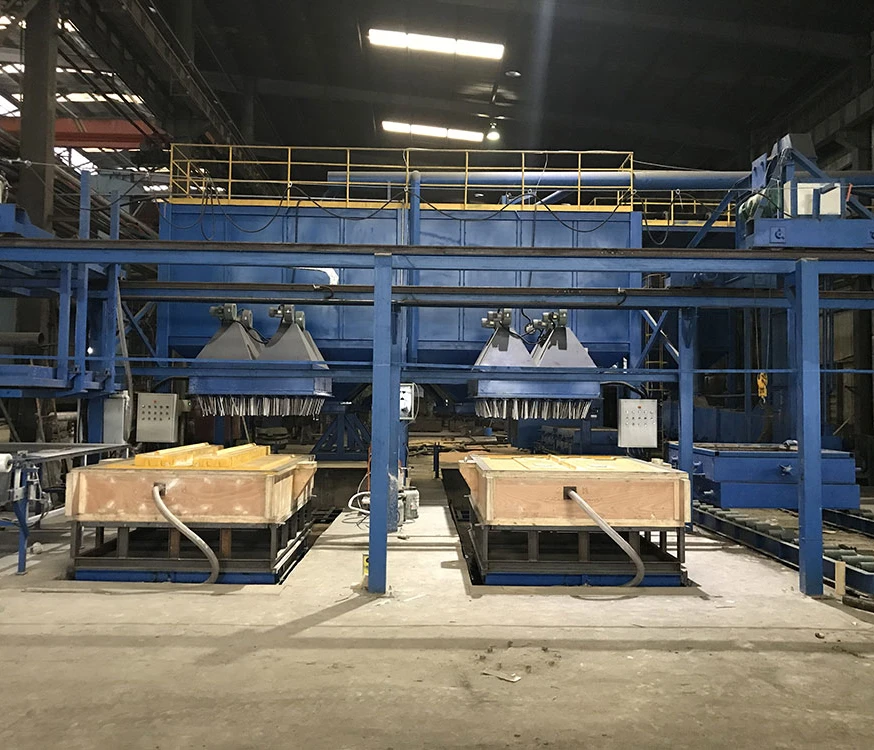
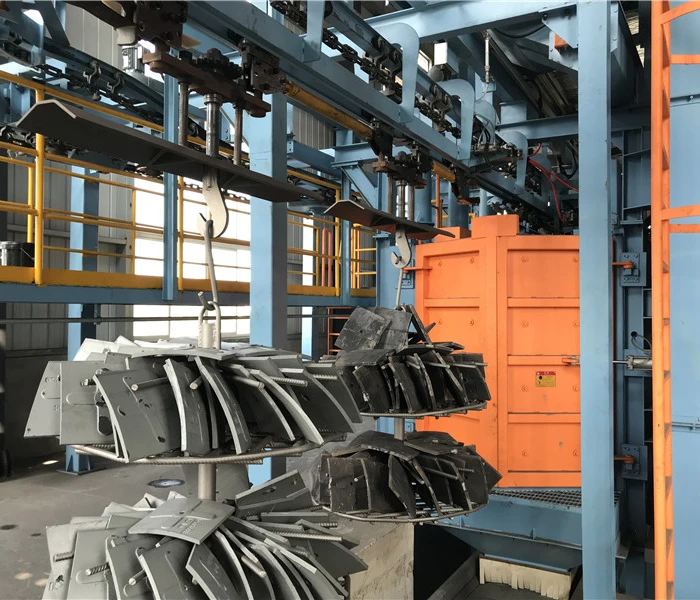
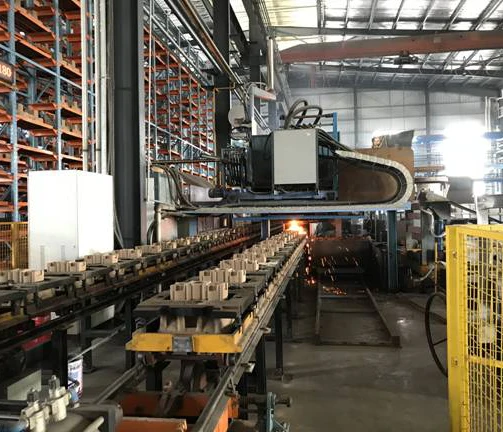
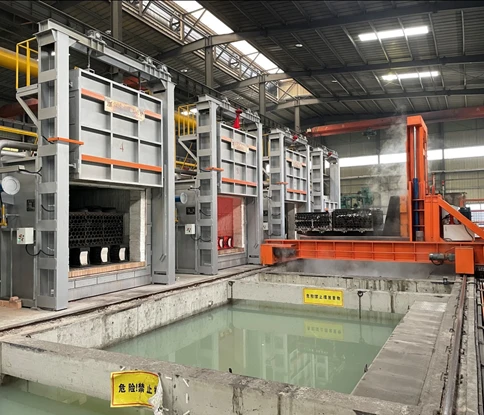
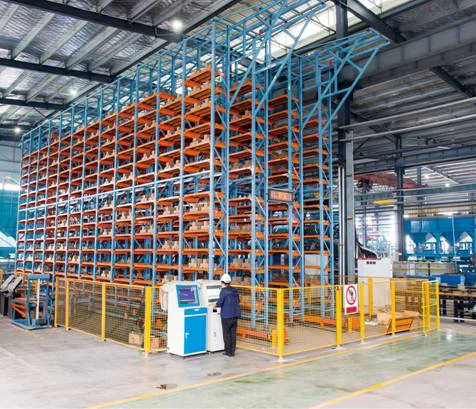
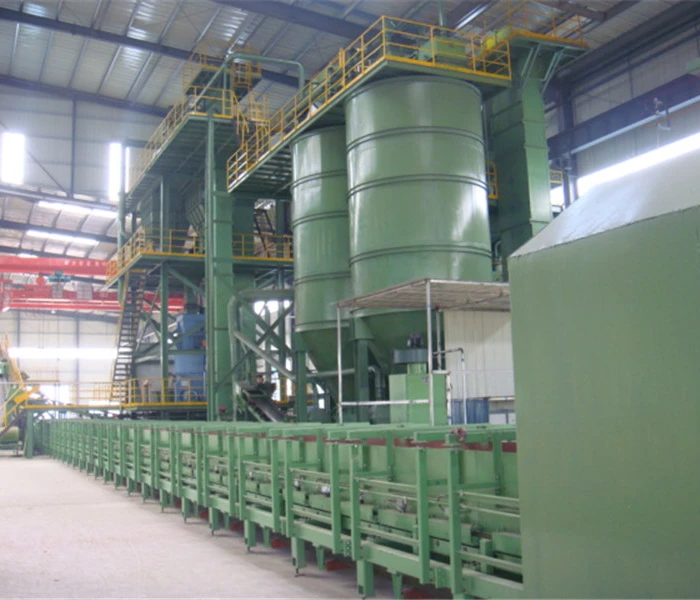
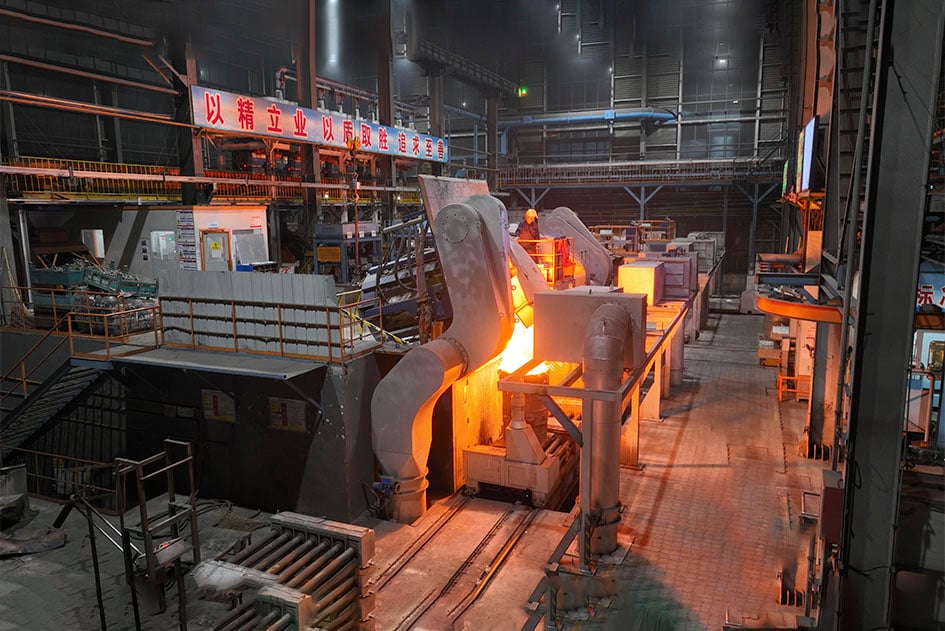
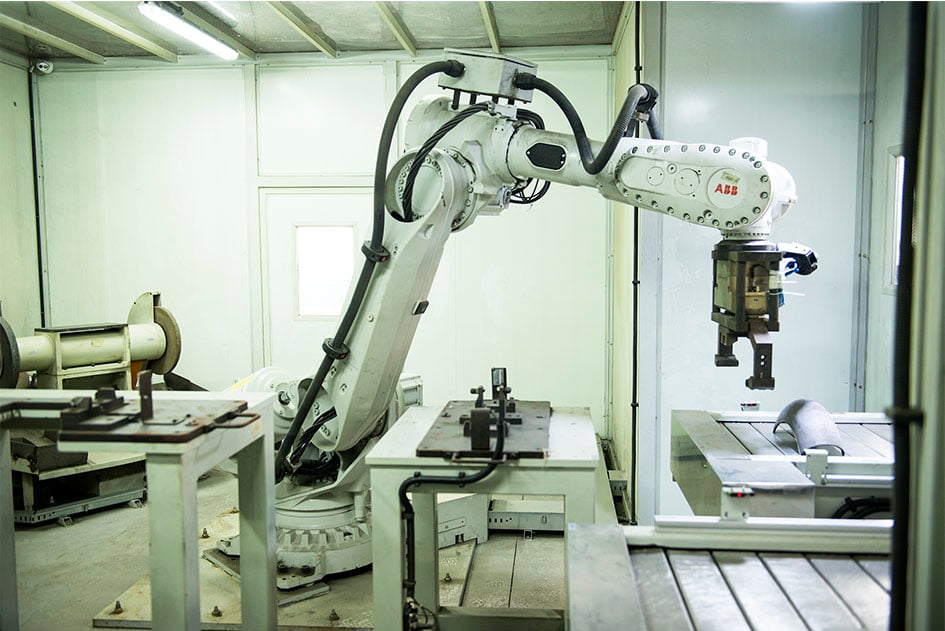
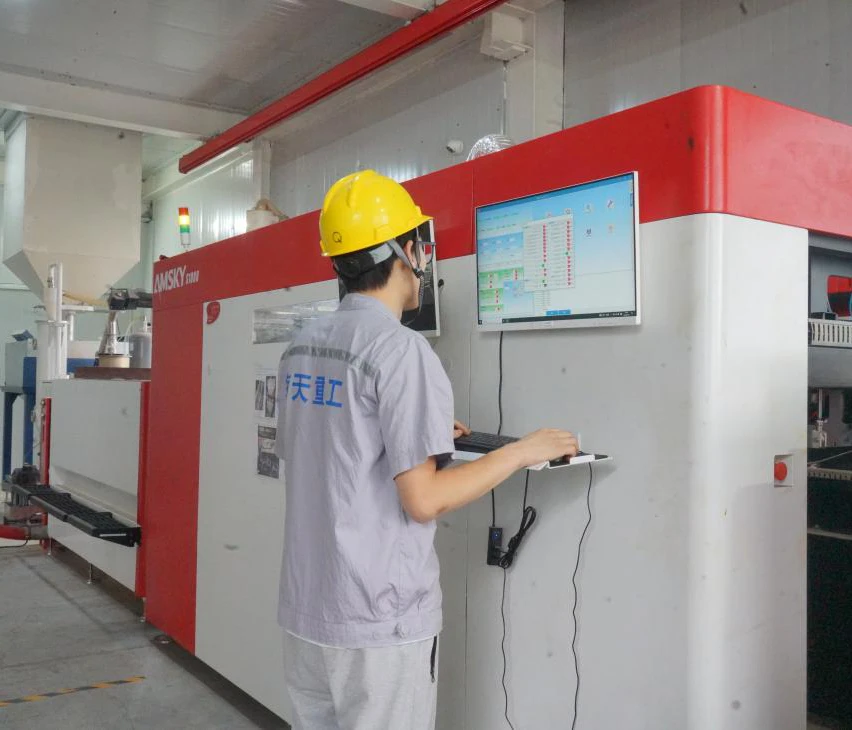
PRÜFGERÄTE
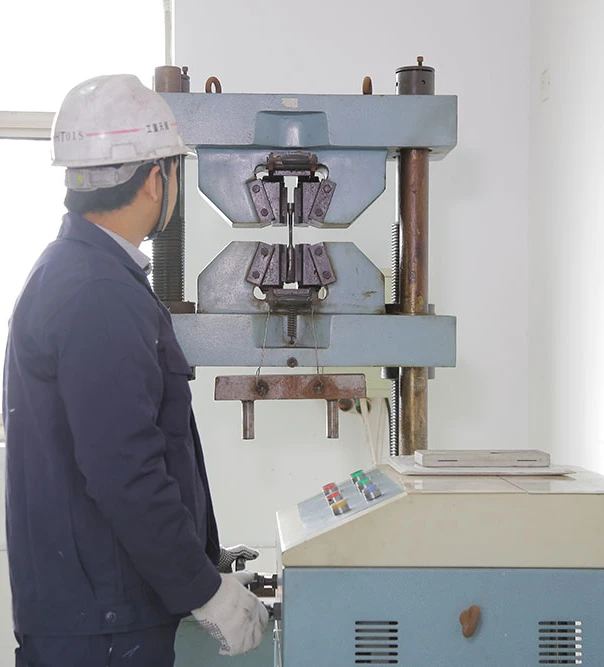
Zugprüfgeräte

Geräte zur Prüfung der Aufprallenergie
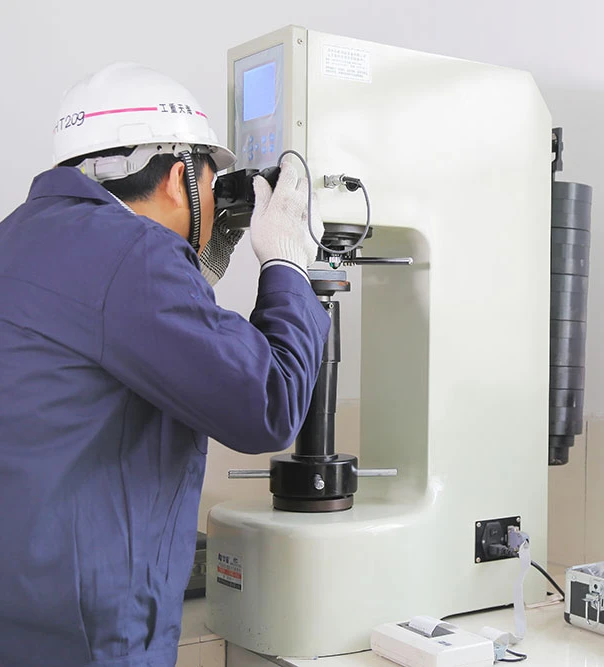
Brinell-Härteprüfgeräte
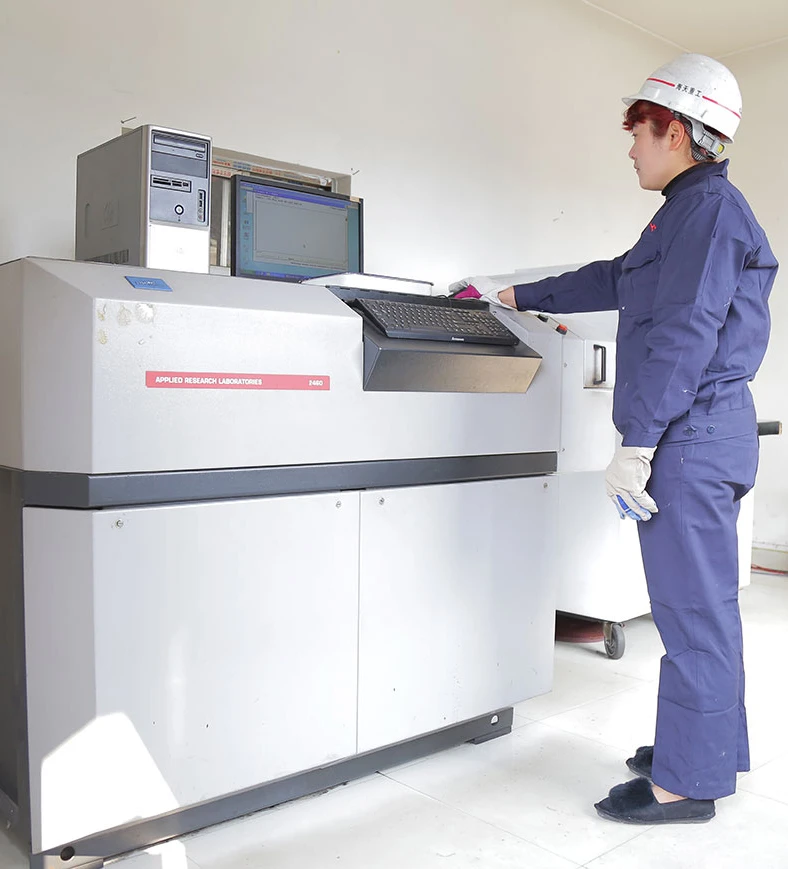
Ausrüstung zur Erkennung von Spektrometerkomponenten
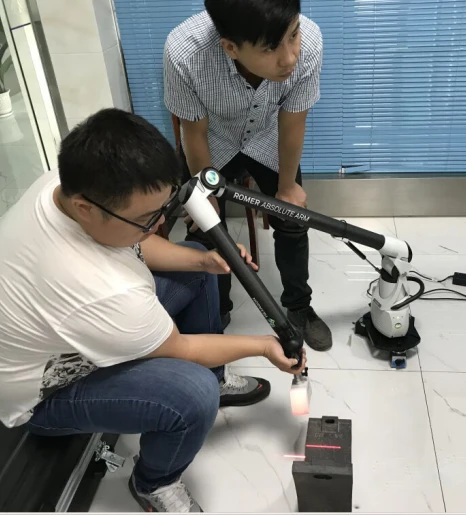
Triangulations-Koordinatenmessgerät
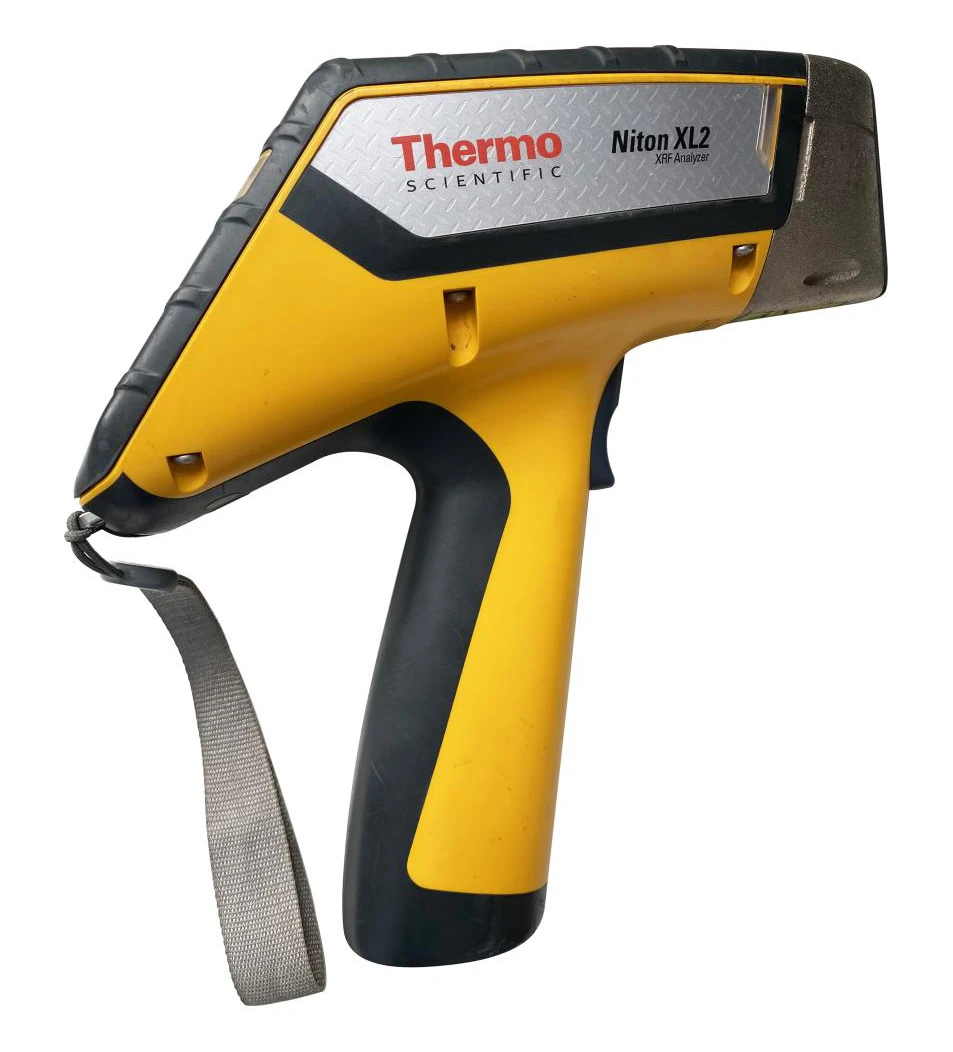
Handspektrometer
PROZESSFLUSS
-
01
Rohstoffauswahl
Im Herstellungsprozess verschleißfester Teile ist die Auswahl der Rohstoffe von entscheidender Bedeutung. Wir wählen sorgfältig hochwertige Legierungsmaterialien aus, um sicherzustellen, dass sie eine hervorragende Verschleißfestigkeit und Festigkeit aufweisen und so eine solide Grundlage für die Qualität der Produkte legen.
-
02
Schmelzvorgang
Nachdem die streng dosierten Rohstoffe in den Ofen gelangen, verwenden wir fortschrittliche Schmelztechnologie, um sicherzustellen, dass die Zusammensetzung und Temperatur des geschmolzenen Metalls den optimalen Zustand erreichen und einen gleichmäßigen und stabilen Metallfluss für die Formung des Produkts gewährleisten.
-
03
Gießen und Formen
Durch den exquisiten Gießprozess wird das geschmolzene Metall in die Form eingespritzt, um sich zu verfestigen und in eine bestimmte Form und Größe zu bringen. Unsere Handwerker sind professionell ausgebildet und beherrschen verschiedene komplexe Formprozesse, um sicherzustellen, dass Form und Größe der Produkte genau sind und die Qualität stabil ist.
-
04
Kugelstrahlen und Schleifen
Nach dem Entformen wird das Produkt einem Feinschleifprozess unterzogen, um Oberflächenfehler und Grate zu entfernen und die Oberfläche glatt und flach zu machen. Unsere Handwerker verwenden sorgfältige Techniken und hervorragende Fähigkeiten, um jedes Produkt zu pflegen und ihm ein perfektes Aussehen und eine perfekte Textur zu verleihen.
-
05
Wärmebehandlungsprozess
Nach dem Wärmebehandlungsprozess werden Struktur und Leistung des Produkts weiter stabilisiert und verbessert. Entsprechend den spezifischen Anforderungen des Produkts verwenden wir unterschiedliche Wärmebehandlungsverfahren, um ihm eine hervorragende Verschleißfestigkeit, Festigkeit und Korrosionsbeständigkeit zu verleihen und ihn an die Anforderungen verschiedener rauer Arbeitsumgebungen anzupassen.
-
06
Lackierung und Inspektion
Das Produkt ist lackiert, was nicht nur das Aussehen verschönert, sondern auch die Korrosionsbeständigkeit und Verschleißfestigkeit seiner Oberfläche verbessert. Anschließend durchläuft es einen strengen Inspektionsprozess, um sicherzustellen, dass alle Indikatoren des Produkts den Standardanforderungen entsprechen und den Kunden zuverlässige Produktgarantien bieten.
-
07
Lagereingang und Auslieferung
Abschließend wird das Produkt einer strengen Qualitätsprüfung unterzogen und sicher im Lager gelagert, sodass es jederzeit ausgeliefert werden kann. Sobald wir die Bestellung des Kunden erhalten haben, werden wir die Lieferung pünktlich, quantitativ und qualitativ abschließen, um sicherzustellen, dass das Produkt sicher und pünktlich beim Kunden ankommt.
QUALITÄTSKONTROLLE WÄHREND DER PRODUKTION
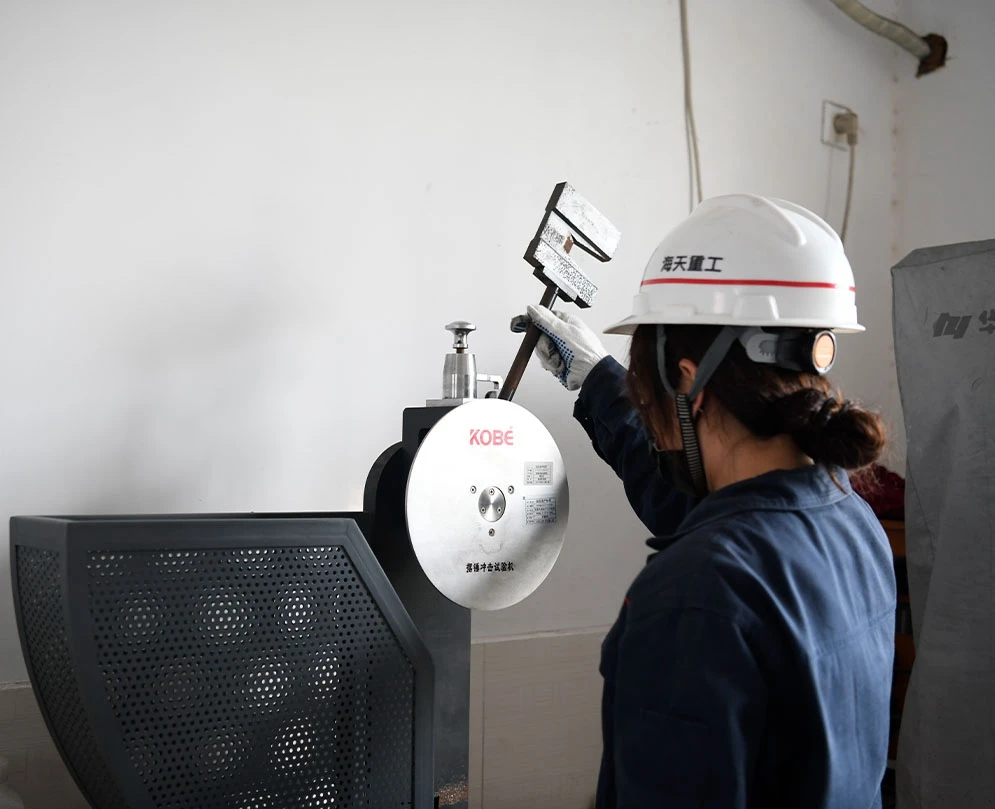
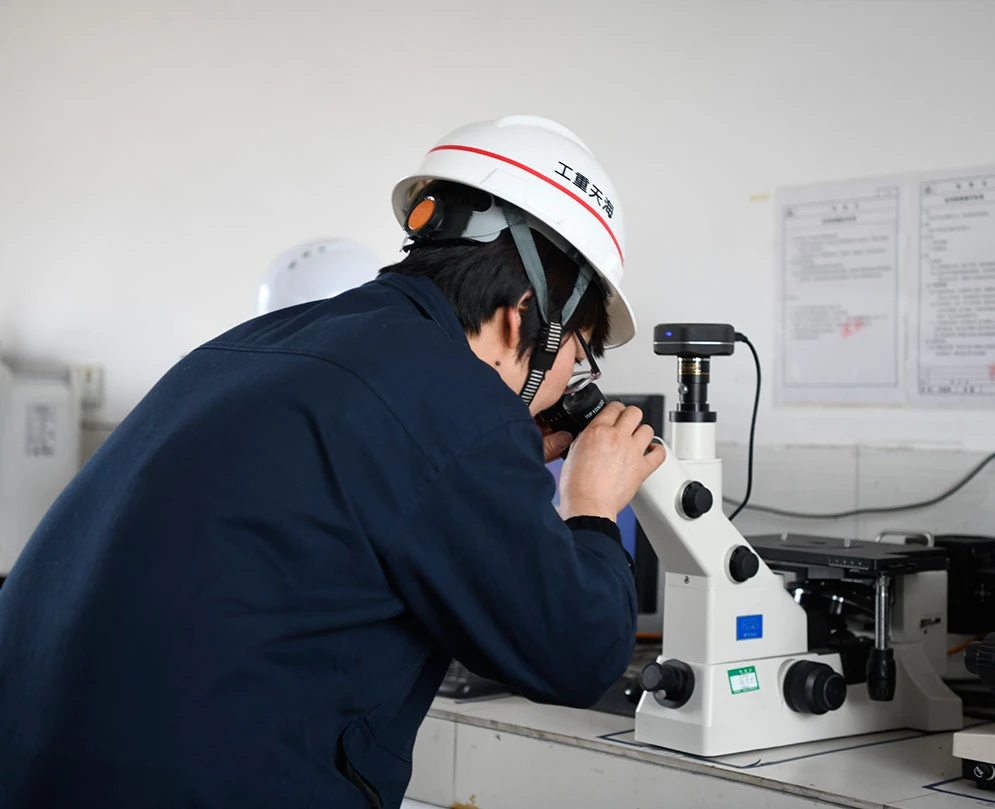
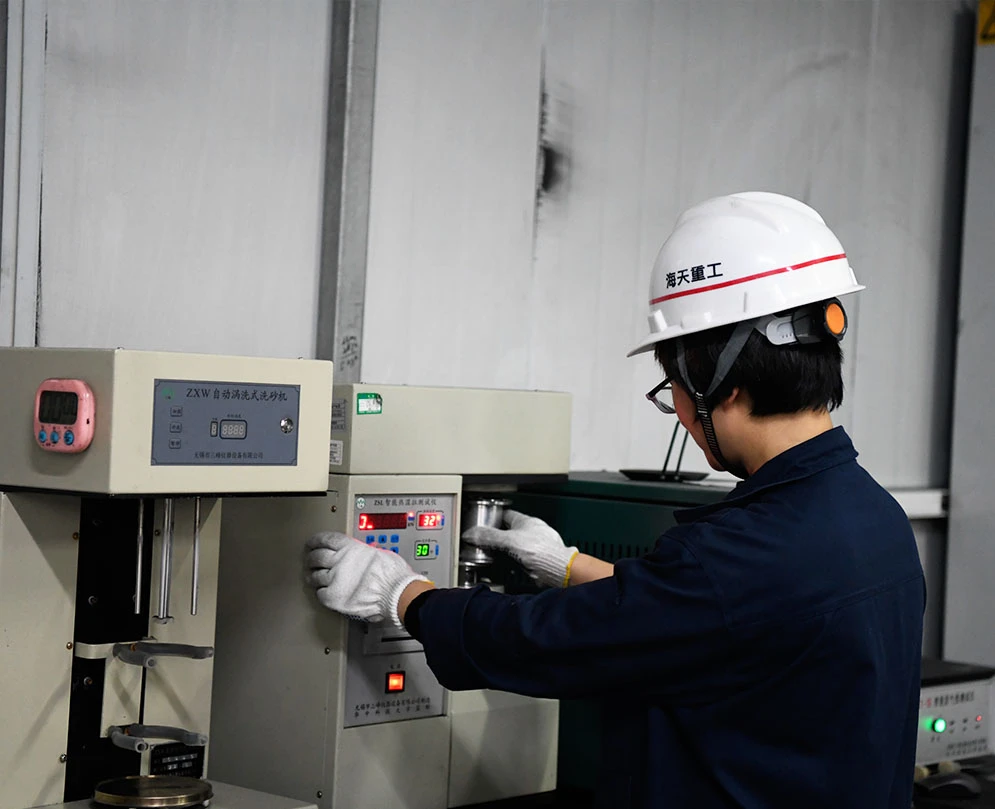
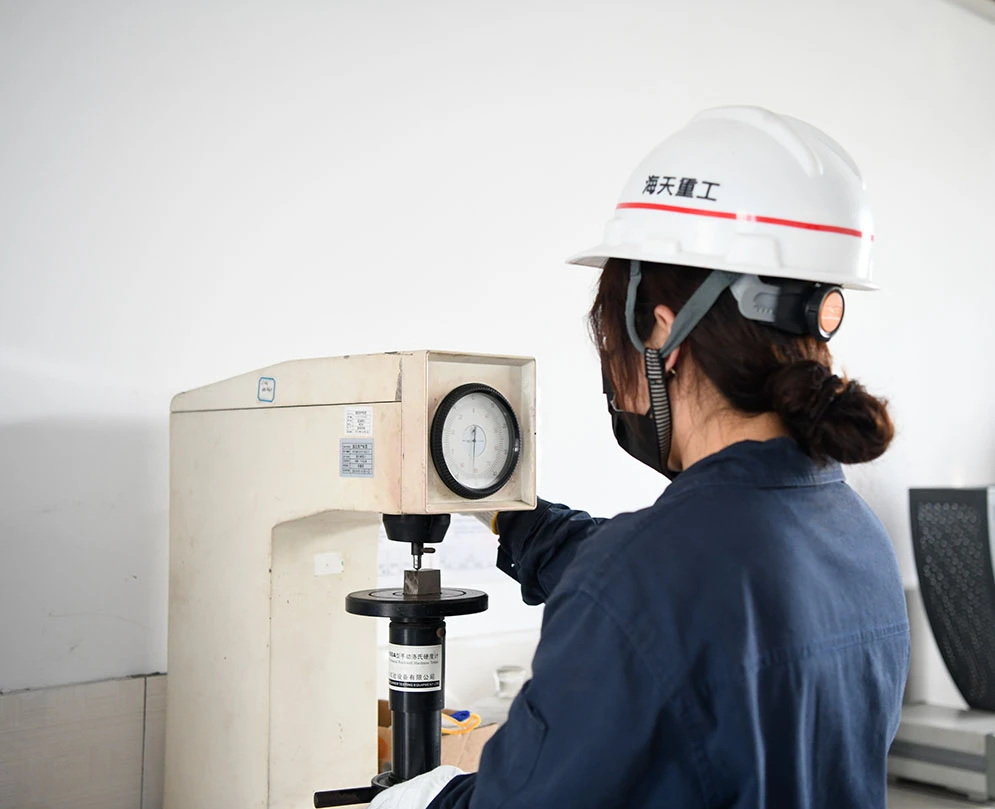
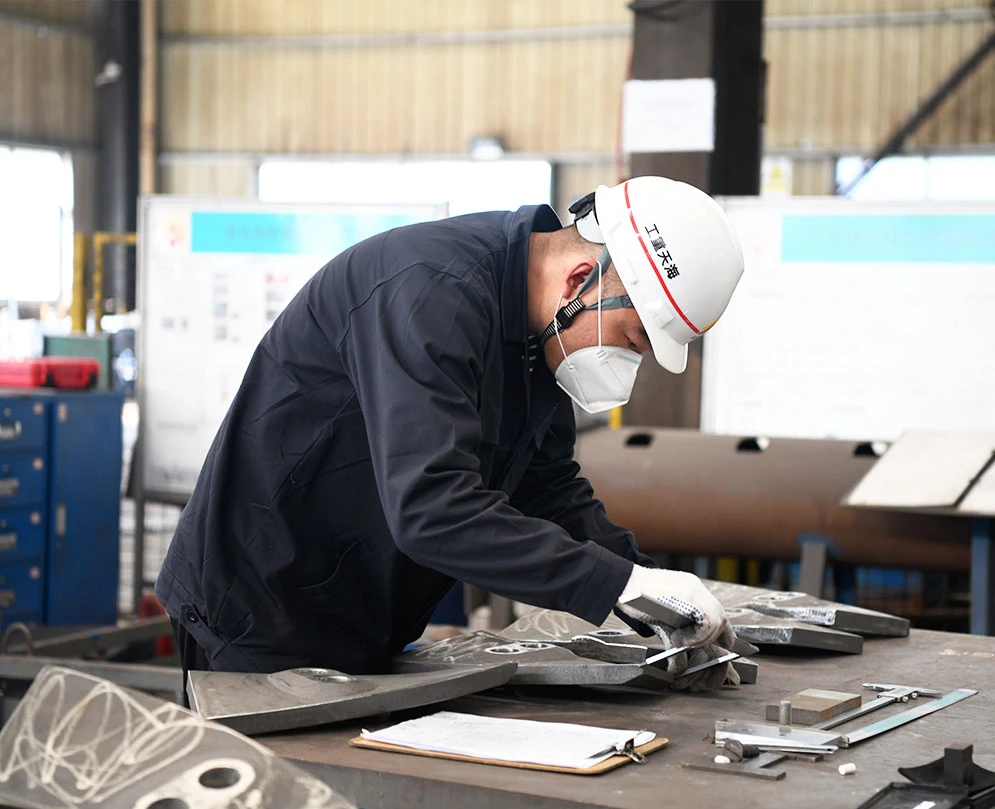
-
Prozessparametersteuerung
Temperaturkontrolle: Überwachen Sie die Temperatur während des Schmelzens, Gießens und der Wärmebehandlung, um sicherzustellen, dass das Metall im geeigneten Temperaturbereich behandelt wird, um die Produktqualität sicherzustellen.
Zeitkontrolle: Kontrollieren Sie die Zeit jedes Prozesses, um sicherzustellen, dass jeder Prozess vollständig und ohne Überschreitung ausgeführt wird, um Fehler zu vermeiden.
Druckkontrolle: Während des Gieß- und Formvorgangs werden Größe und Druckverteilung durch Vakuumieren durch eine transparente Membran gesteuert, um die Gleichmäßigkeit und Stabilität der die Form füllenden Metallflüssigkeit sicherzustellen.
-
Anwendung von Prüfgeräten
Metallurgische Mikroskoperkennung: Beobachten und analysieren Sie die Metallstruktur, um festzustellen, ob im Metall Defekte wie Poren und Einschlüsse vorhanden sind.
Ultraschallerkennung: Verwenden Sie Ultraschalltechnologie, um Fehler im Produktinneren wie Risse, Einschlüsse usw. zu erkennen und so die Qualität und Zuverlässigkeit des Produkts sicherzustellen.
Härtetest: Testen Sie die Härte des Produkts, um zu beurteilen, ob seine Verschleißfestigkeit und seine mechanischen Eigenschaften den Anforderungen entsprechen.
-
Automatisierte Produktionsanlagen
Automatisiertes Steuerungssystem: Verwenden Sie fortschrittliche automatisierte Steuerungssysteme, um den Produktionsprozess zu überwachen, eine präzise Steuerung und Anpassung der Produktionsparameter zu erreichen und die Produktkonsistenz und -stabilität zu verbessern.
-
Manuelle Qualitätskontrolle
Inspektion durch Prozesstechniker: Prozesstechniker inspizieren regelmäßig die Produktionslinie, um sicherzustellen, dass die Ausrüstung normal funktioniert und die Produktionsparameter den Anforderungen entsprechen.
Betriebsüberwachung des Prozessbetreibers: Überwachen Sie den Betrieb des Prozessbetreibers, um sicherzustellen, dass der Betrieb standardisiert und genau ist, und reduzieren Sie die Auswirkungen von Betriebsfehlern auf die Produktqualität.
-
Datenanalyse und -verbesserung
Erfassung und Analyse von Qualitätsdaten: Sammeln Sie verschiedene Qualitätsdaten im Produktionsprozess, führen Sie statistische Analysen durch, finden Sie Probleme rechtzeitig und ergreifen Sie Verbesserungsmaßnahmen.
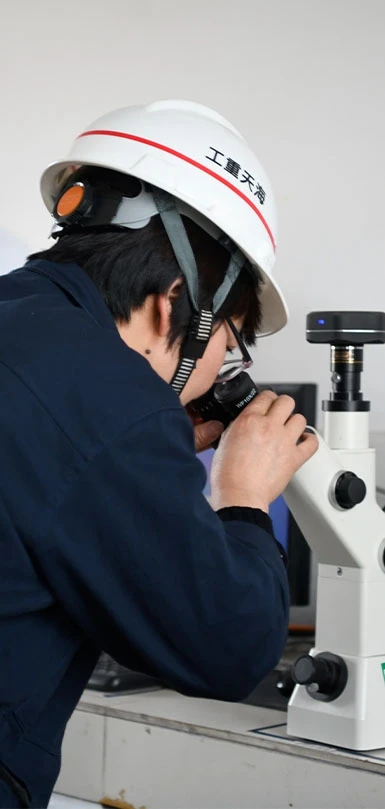
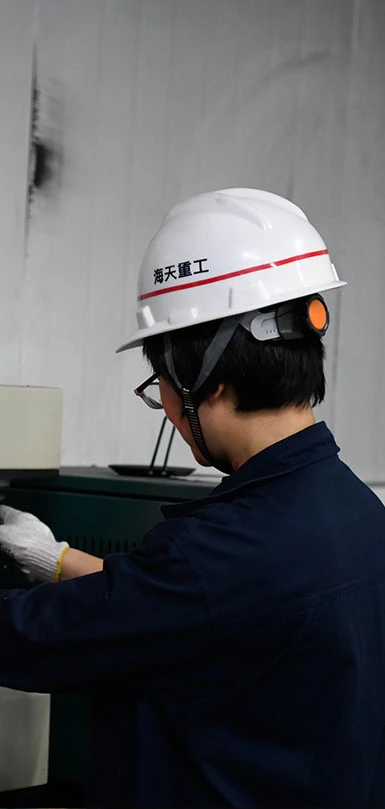
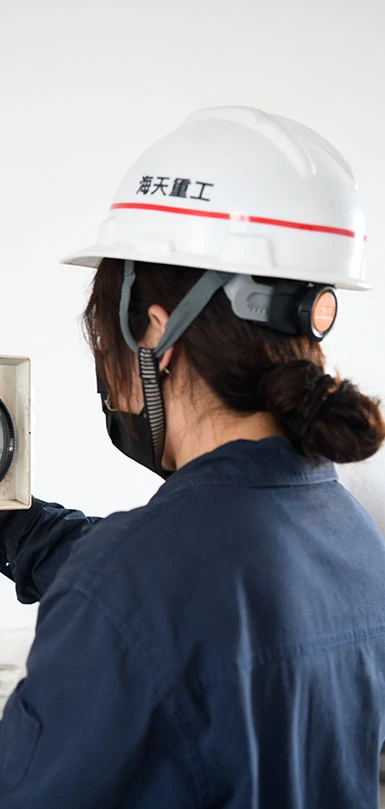
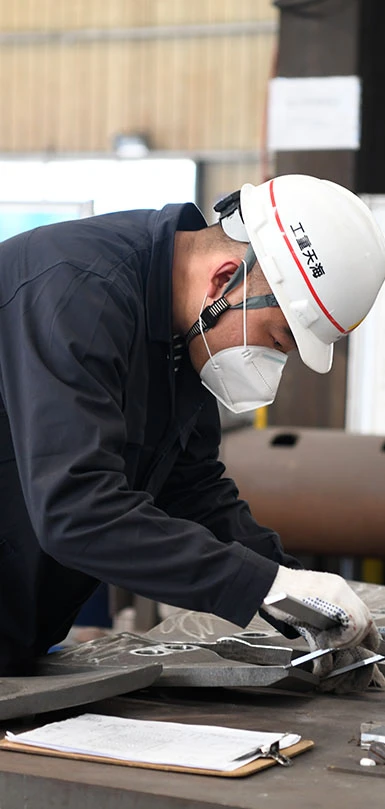
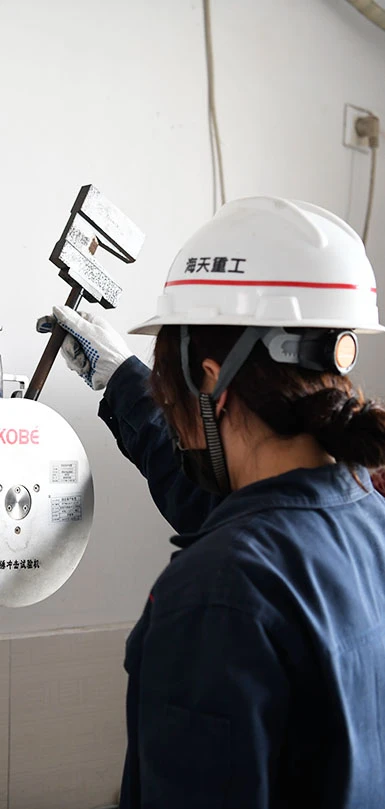
Wenn Sie Interesse an unseren Produkten haben oder Fragen haben, können Sie sich gerne an uns wenden.
Wir bieten professionelle Beratungsleistungen und maßgeschneiderte Lösungen entsprechend Ihren Anforderungen.
JETZT ANFRAGE SENDENKontaktinformationen
Tel.: 0555-71661667166199
Fax: 0555-6971198
Webseite: https://www.htwearparts.com
E-Mail: info@mashthi.com
Postleitzahl: 243141
Adresse: Xinshi Industrial Park, Bezirk Bowang, Stadt Ma'anshan, Provinz Anhui, China