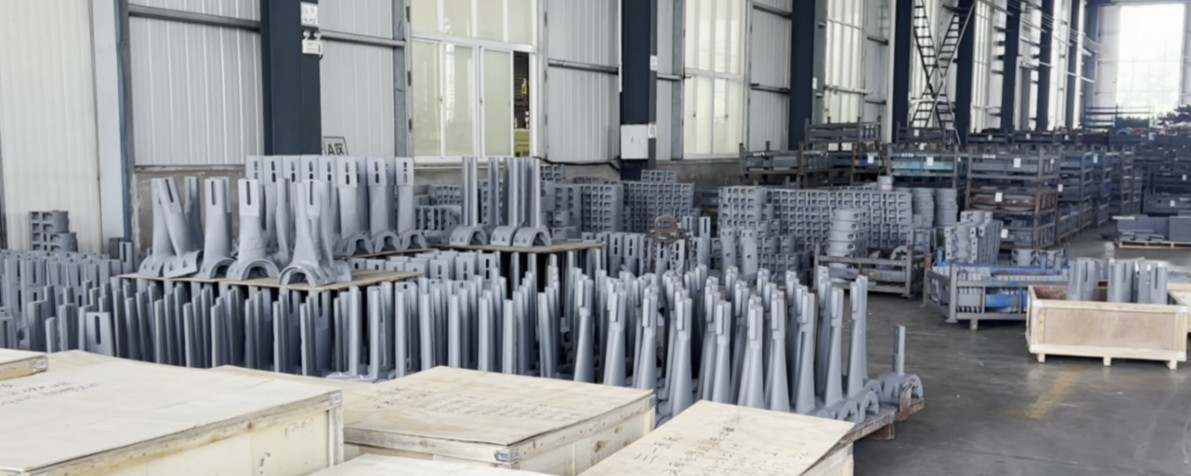
3D Printing-Based Rapid Development Solutions
Haitian Heavy Industry leverages cutting-edge industrial 3D printing technology to break through the limitations of conventional casting. With mold-free prototyping and agile development, we drastically reduce the lead time from design to production, especially for complex geometries and customized wear-resistant parts.
POPULAR WEAR PARTS FOR SALE
- Impact Crusher Parts
- Concrete Mixing Plant Parts
- Asphalt Mixing Plant Parts
-
OEM Lining Plate For Concrete Mixing Plant
-
Concrete Mixing Plant Iron Casting Scraper
-
Concrete Mixing Plant Wear-resistant Lining Plate
-
High Hardness Lining Plate For Concrete Mixing Plant
-
Wear-resistant Lining Plate
-
Mixing Arm For Concrete Mixing Plant
-
Impact Resistant Lining plate For Concrete Mixing Plant
-
Arm Protection-Concrete Mixing Plant
-
Mixing Arm-Concrete Mixing Plant
-
Concrete Mixing plant High-precision Scraper
-
Scraper-Concrete Mixing Plant
-
High Toughness Scraper For Concrete Mixing Plant
-
Concrete Mixing Plant Lining Plate
-
Concrete Mixing Plant High Wear-resistant Lining Plate
-
Concrete Mixing Plant Heat-resisting Lining Plate
-
Customizable Mixing Arm For Concrete Mixing Plant
-
Concrete Mixing Plant Wear Resistant Seal
-
Discharge Door ARC Liner
-
Lining Plate-Concrete Machinery
-
High Temperature Tolerance Lining Plate
-
Economical & Corrosion Resistance Blade
-
Diverse Choices Lining Plate
-
Concrete Scraper High Efficiency
-
High Strength Lining Plate
-
Corrosion Resistance Scraper
-
Full Series Lining Plate
-
General Lining Plate For Concrete Mixing Plant
-
Good Toughness Lining Plate
-
Strong Wear Resistance Lining Plate
-
High Temperature Resistance Plate
-
Good Strength Lining Plate
-
Lining Plate For Asphalt Mixing Plant
-
Lining Plate-Asphalt Mixing Plant
-
Asphalt Side Lining parts
-
Asphalt Machinery Series
-
Mixing Arm-Asphalt Mixing Plant
-
Spiral Blade For Asphalt Mixing Plant
-
Sealing element-Asphalt Mixing Plant
-
Scraper-Asphalt Mixing Blade
-
Spiral Blade-Asphalt Mixing Plant
-
Asphalt Side Lining
Solution Highlights
-
Technical Advantage: Efficient Development for Complex Structural Requirements
Our high-resolution 3D printers support accurate contour shaping and internal structure modeling, ideal for functional testing and mechanical performance validation of complex wear-resistant parts.
*High-Precision Dimensional Accuracy: Printing tolerance is controlled within ±0.3mm, ensuring precise dimensional replication and reducing trial-and-error costs.
*High Design Flexibility: Capable of forming intricate geometries, internal channels, and reinforcing ribs in a single build, minimizing post-processing work.
*Multi-Material Casting Compatibility: Suitable for a wide range of wear-resistant casting materials such as high-chromium cast iron, high-manganese steel, and alloy steel.
*Tool-Free Core Making: Eliminates the need for traditional mold tooling, saving over 60% in mold costs — ideal for prototype development and small-batch customization. -
Cost Control: Affordable Solutions for High-Performance Demands
Traditional mold development often costs thousands to tens of thousands of RMB, especially for custom components and new product development, which becomes a significant entry barrier for many clients.
Haitian Heavy Industry breaks this cost barrier through direct core printing via 3D printing technology:
①No tooling cost, minimizing upfront investment
②On-demand production during the sampling phase, avoiding inventory pressure
③One-time printing enables multiple sample iterations, enhancing design success rate
④Integrated with precision heat treatment and optimized alloy composition, extending service life and reducing long-term operating costs
Ideal for low-volume or multi-variety production, our 3D printing technology eliminates tooling costs and reduces upfront investment, making it extremely cost-effective for prototyping, pilot runs, or on-demand production. -
Rapid Delivery: Flexible Customization, Accelerated Development Cycle
Using industrial-grade sand 3D printers, we can bypass traditional wood or metal mold making. Complex casting patterns can be delivered within as little as 3 days, significantly shortening the product development cycle.
Our streamlined production pipeline—from technical drawing assessment and digital design to 3D sand core printing and precision casting—allows for sample delivery in as little as 7 days, making it ideal for fast-track projects, critical breakdown repairs, and prototype validation under tight deadlines.
We accept 3D drawings, physical samples, or scanned data. Our engineering team quickly generates printable digital models to meet your customized or non-standard wear parts development needs. -
Professional Engineering Team and Technical Services
Backed by a technical team of 23 senior engineers and 37 process consultants, we provide end-to-end support throughout your product development journey. Beyond product manufacturing, we deliver a complete set of tailored engineering solutions, including:
24-hour quotation turnaround——Drawing evaluation and design optimization——Joint analysis of structural integrity and wear resistance——One-on-one engineer follow-up and technical feedback——Application scenario matching and material recommendations——After-sales maintenance and technical support.
SERVICE WORKFLOW
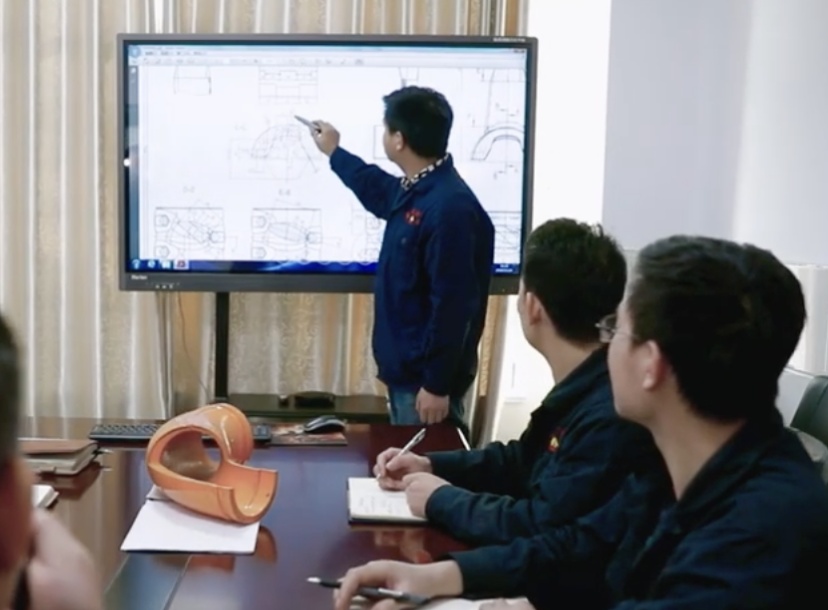
1. Requirement Consultation & Technical Evaluation
We establish an efficient communication channel with clients to deeply understand equipment conditions, operating environments, and performance requirements. Through comprehensive data collection and technical evaluation, we ensure the solution is precisely tailored from the start—eliminating guesswork and reducing resource waste.
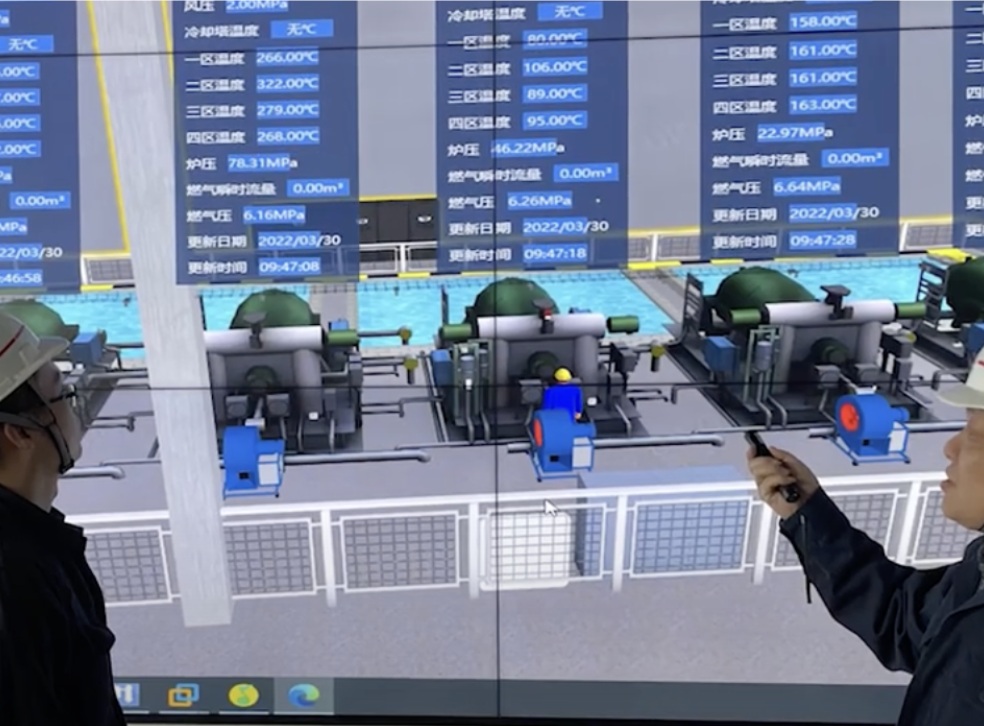
2. Customized Solution Development
Leveraging advanced CAE analysis and extensive material expertise, we tailor optimal part materials and structural designs for clients. Our solutions fully consider wear resistance, mechanical strength, and manufacturability, paired with transparent pricing and reliable lead times—helping clients maximize cost-effectiveness.
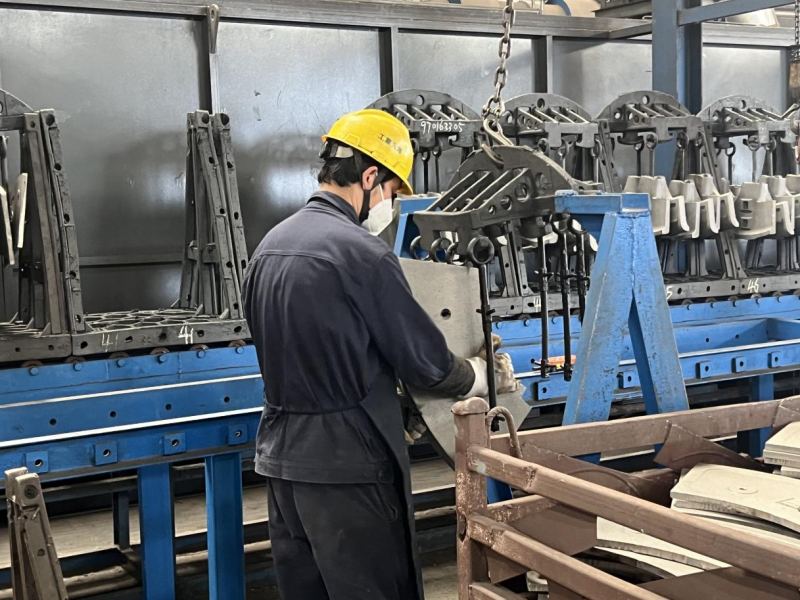
3. Efficient Tooling Development & Sample Validation
Our in-house tooling design and manufacturing team ensures short lead times and high precision in mold development. Samples undergo rigorous multi-dimensional inspections and field testing. Only upon client approval do we proceed to mass production, ensuring product performance and quality meet expectations.
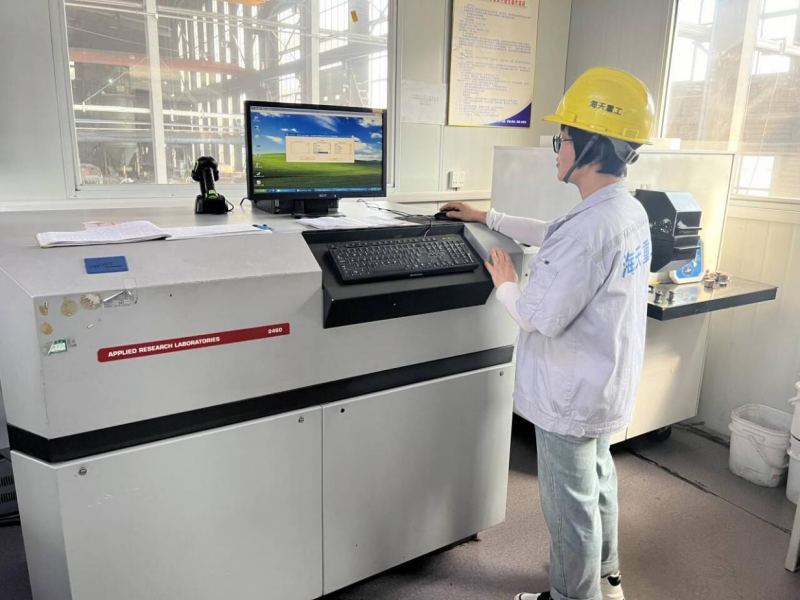
4. Comprehensive Quality Control System
We implement full-process quality monitoring including dimensional checks, chemical composition analysis, mechanical performance tests, and nondestructive examinations. Every product leaving our facility meets or exceeds industry standards. Detailed inspection reports are available for client review, enhancing transparency and trust.
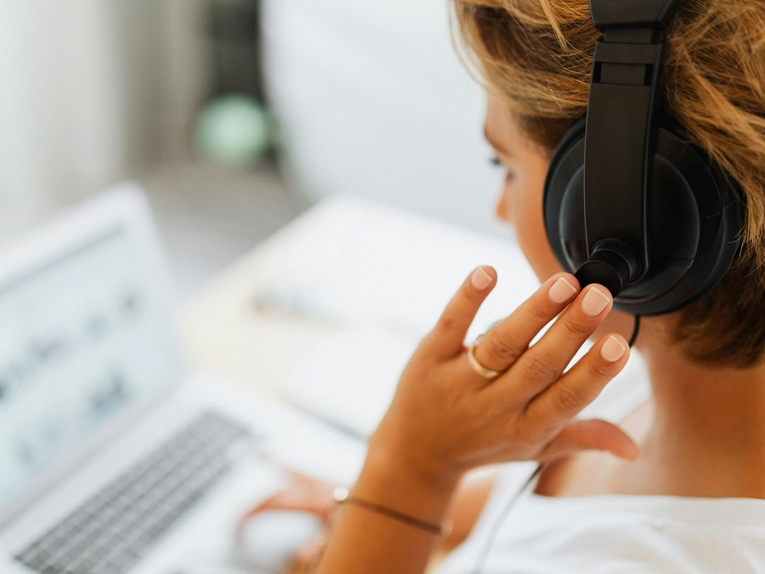
5. Professional Packaging & Global Logistics Support
We design diversified protective packaging tailored to product characteristics to ensure safety during transit. Integrating multimodal transport channels, we deliver worldwide quickly with real-time tracking—minimizing customer lead times.
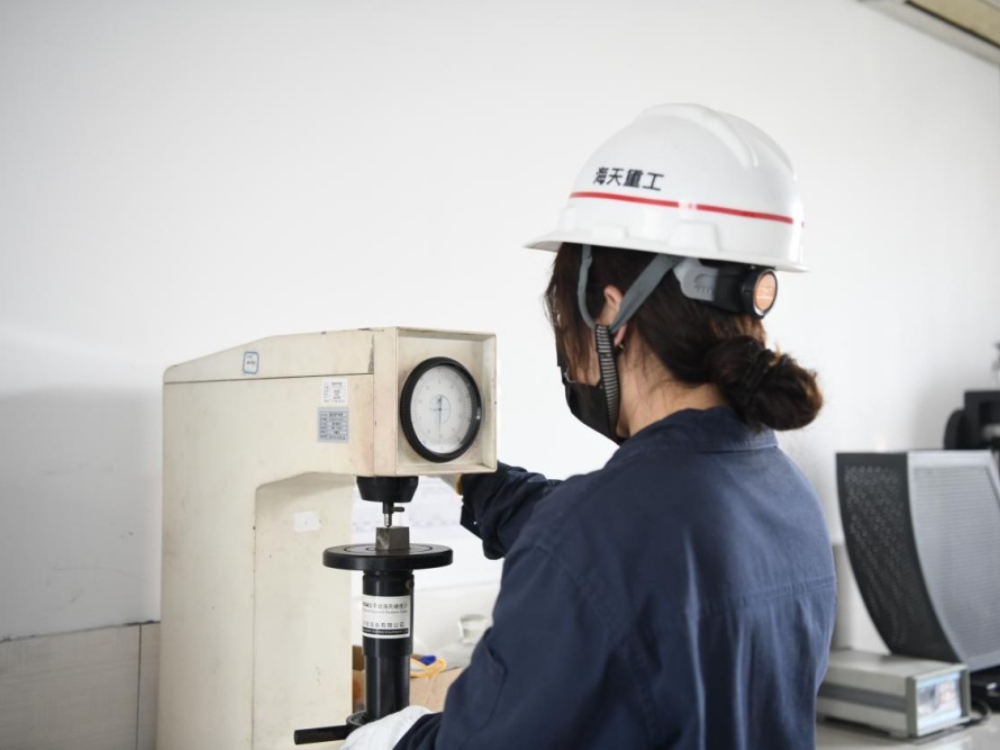
6. Continuous After-Sales Technical Support
Offering 24/7 response service with dedicated account managers, we swiftly resolve technical challenges encountered onsite. We continuously improve products based on client feedback, jointly ensuring stable and efficient equipment operation.